Sharpdragon
Как Аккерманн Цемент делает цемент ( 65 фото )
Цемент - это один из основных строительных материалов. В основном он используется для изготовления бетона и строительных растворов. Кроме того, производство цемента – это еще и один из важнейших индикаторов развития реального сектора экономики. Российский цемент всегда был и есть качественным продуктом, и он востребован как в России, так и за рубежом. В 2023 году объем производства цемента в России вырос на 3,6%, до 63 млн тонн. И в мировом топе по его производству наша страна находится на 8 месте, и немалый вклад и заслуга в этом Оренбургской области. Представляете, я вроде уже бывалый ходок по заводам, а вот на цементном еще ни на одном не был. И вот я уже стою на проходной AKKERMANN CEMENT (ранее - Южно-Уральская горно-перерабатывающая компания).

На фоне капризной погоды здесь сразу видны яркие пятна, которые и настраивают на позитив.
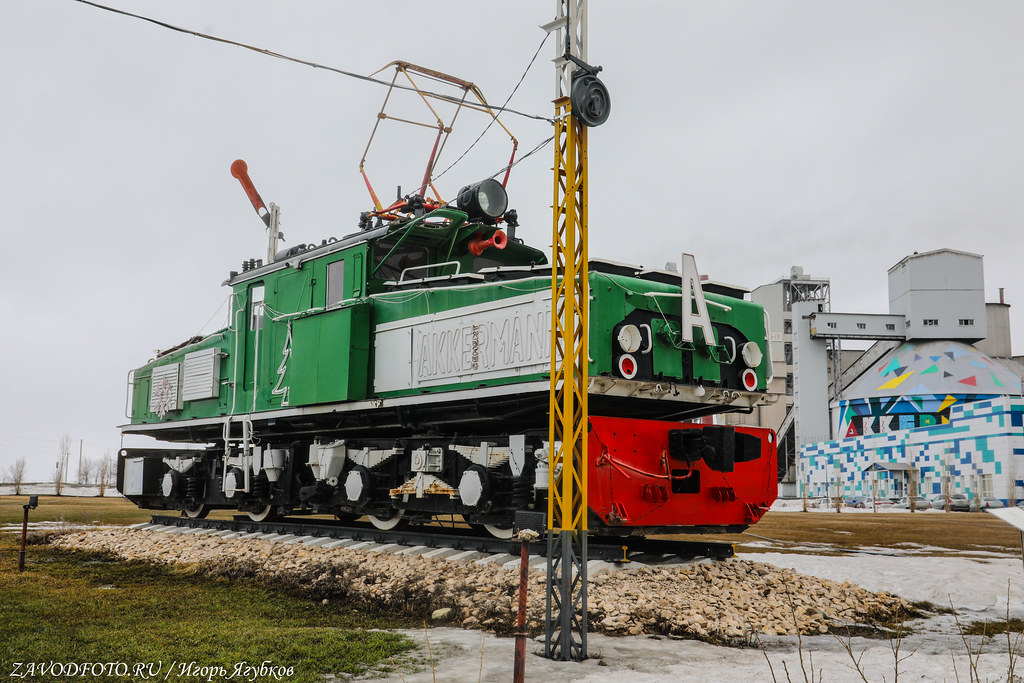
Привет-привет. Как оказалось, наш сегодняшний герой - это один из флагманов отрасли, да еще мы же почти земляки. Дело в том, что в семью AKKERMANN CEMENT входит и Горнозаводскцемент, тот самый, что из Пермского края.
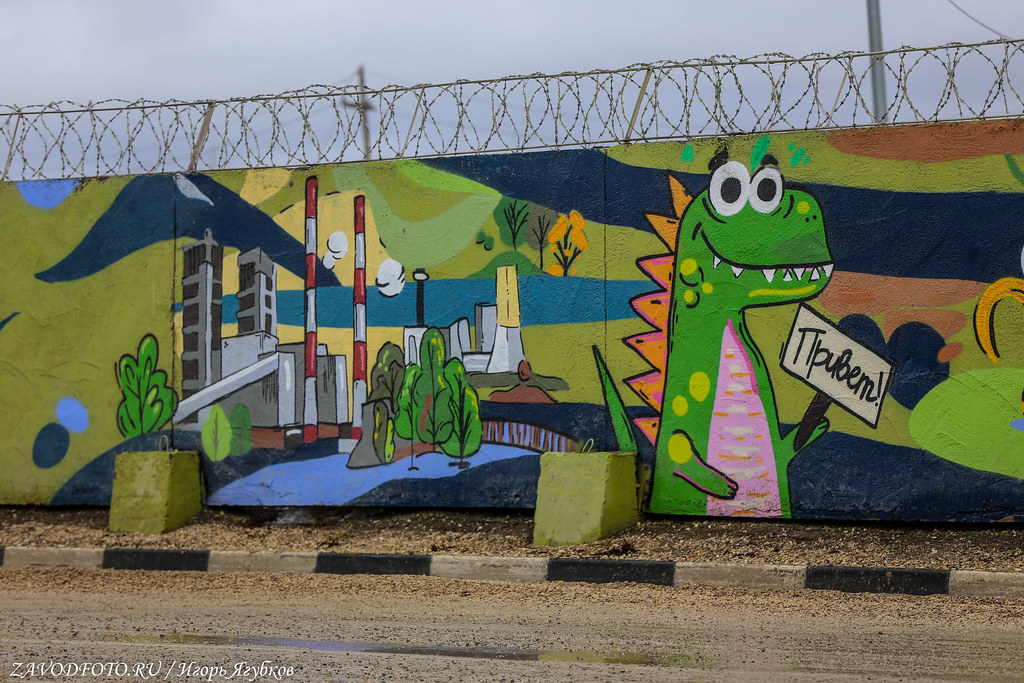
Название завода происходит от близлежащего поселка Аккермановка, на территории которого и располагается завод. По одной из версий благодарные потомки назвали поселок Аккермановка вблизи г. Новотроицка в честь немецкого горного изыскателя Фридриха Аккерманна. Он по инициативе Екатерины II оказался со своей семьей в Оренбургской губернии и получил надел земли недалеко от казачьей станицы Хабарное. До этого времени он объездил уже пол-России, серьезно изучил ее сырьевые запасы и догадывался об оренбургских залежах. Скрупулезно, с немецкой педантичностью и старательностью Фридрих подошел к изучению и этих мест. Уже через несколько лет Аккерманн отыскивает в окрестностях станицы Хабарное месторождение никеля, а позднее и залежи железных руд. Считается, что его данные сильно помогли первооткрывателю и советскому геологу Иосифу Леонтьевичу Рудницкому в обнаружении местных рудных месторождений.
Это такой нарядный один из силосов для хранения клинкера. Его высота составляет 42 метра, длина окружности здания 220 метров, общая площадь 9 000 м2.
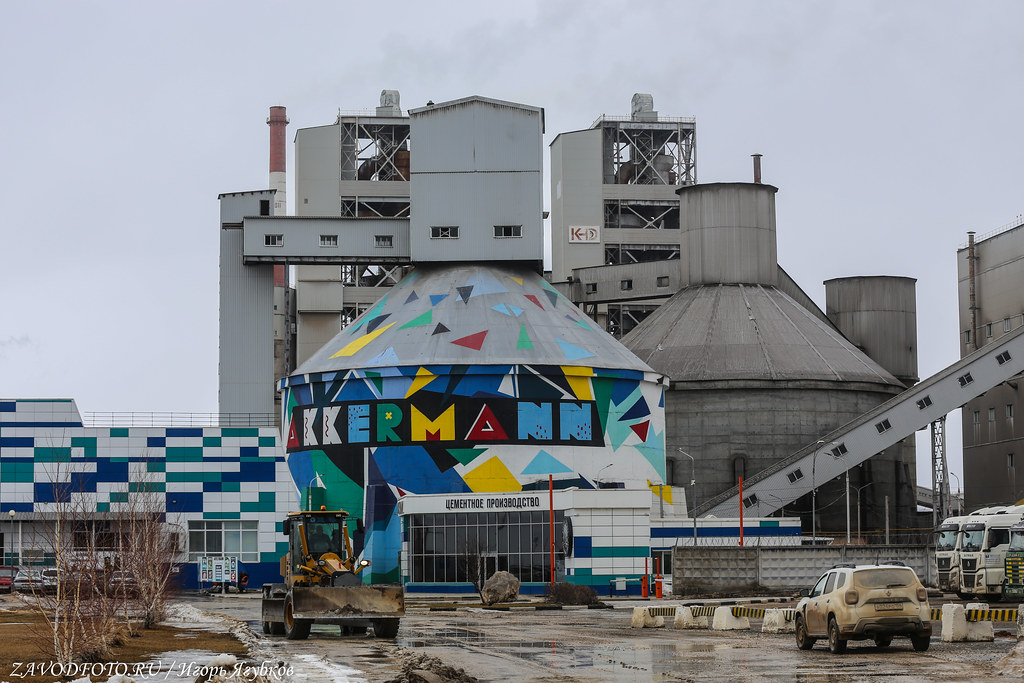
Завод в Новотроицке образован на базе цеха разработки шлаковых отвалов, ранее входившего в состав Орско-Халиловского металлургического комбината. 23 октября 2002 года создается ООО «Южно-уральская Горноперерабатывающая Компания». В 2005 году в её состав входят Аккермановский рудник и известково-обжиговый цех. Сам Аккермановский рудник начали разрабатывать в начале 50-х годов прошлого века. В 2006 году принимается решение о строительстве современного цементного производства. Ответственным за его проектировку был назначен Сибниипроектцемент. На оснащенность завода денег решили не жалеть, тогда выбирали из лучшего в мире. Выбор пал на оборудование немецкой компании KHD HUMBOLDT WEDAG (ZAB Zementanlagenbau GmbH Dessau) – мирового лидера в производстве цемента сухим способом. 15 ноября 2010 года происходит торжественное открытие первой очереди производства, мощность которой составляет 1 млн 300 тысяч тонн цемента в год. А в мае 2013 года здесь запускают вторую очередь с аналогичной мощностью. В 2020 году ООО «Южно-уральская Горноперерабатывающая Компания» получает новое имя ООО «АККЕРМАНН ЦЕМЕНТ».
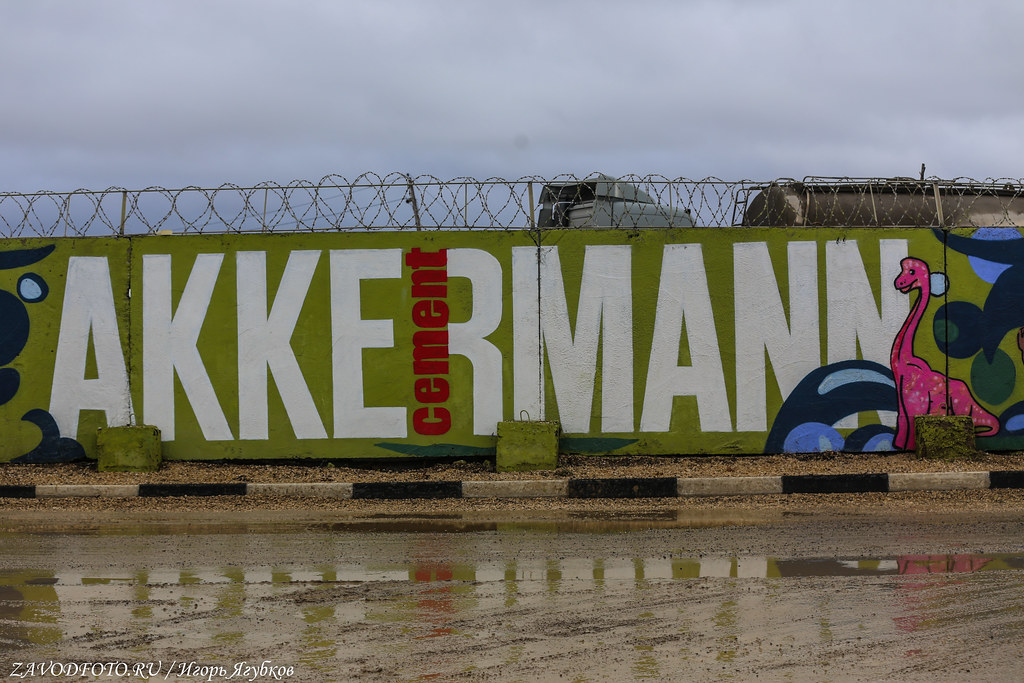
Сегодня Группа предприятий под брендом AKKERMANN (два цементных завода) входит в пятерку крупнейших отечественных производителей цементной продукции. Их цемент широко представлен в 22 регионах нашей страны и Казахстана.
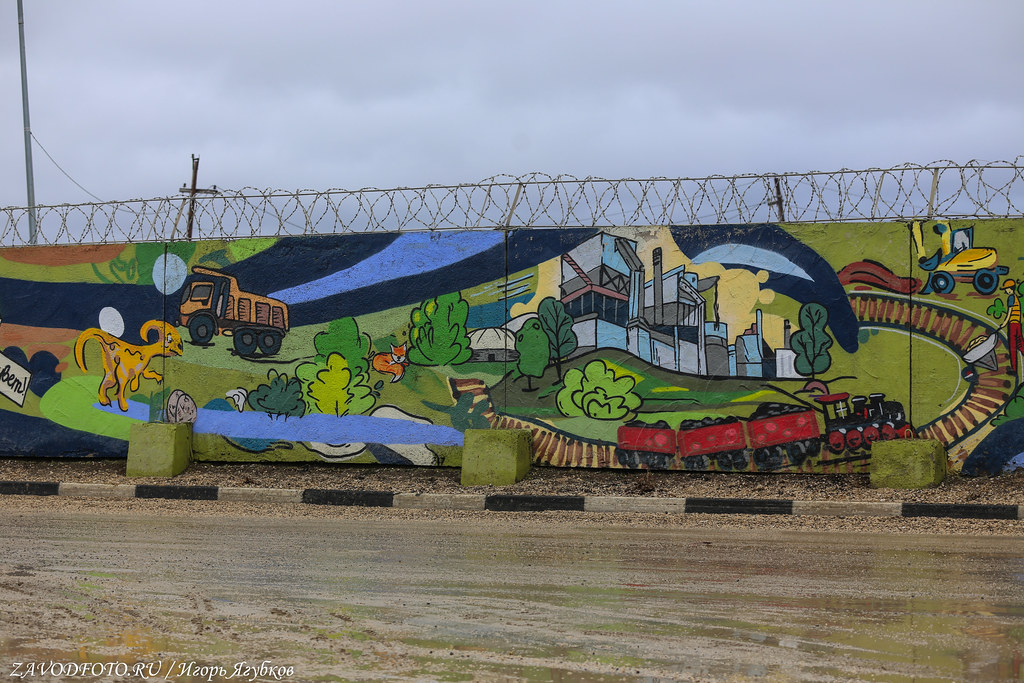
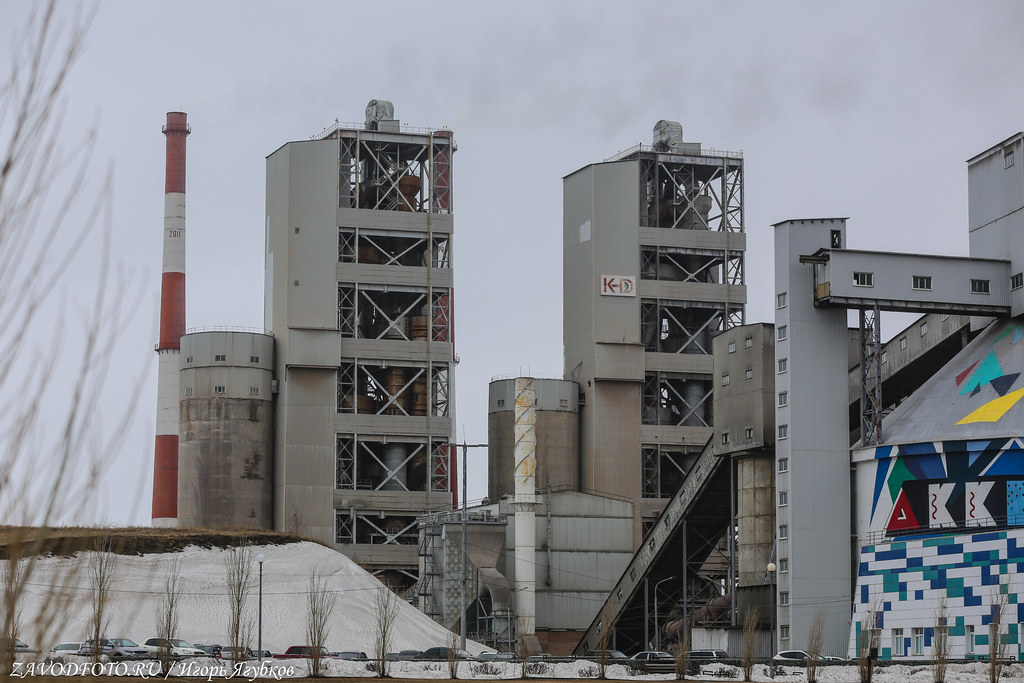
Цемент - это незаменимый материал, без которого нельзя представить ни один строительный объект. Уникальность материала неоспорима, ведь так или иначе он участвует практически во всех строительных этапах. Современные комбинаты используют три базовых метода изготовления цемента, которые зависят от метода подготовки сырьевого материала к обжигу: мокрая технология, сухая и полумокрая (комбинированная). Вроде бы время идет, а на производствах цемента достаточно сложно придумать что-то новое с точки зрения рецептуры или технологий. Каждая компания старается брать большими коммуникациями, цифровизируют продажи, сервисом, скоростью доставки. Даже тот факт, что компании из отрасли стали открываться, это же огромный плюс, и большее доверие к продукции. Кстати, любой из вас может попасть и сюда, завод АККЕРМАНН ЦЕМЕНТ с модным нынче промтуризмом дружит.
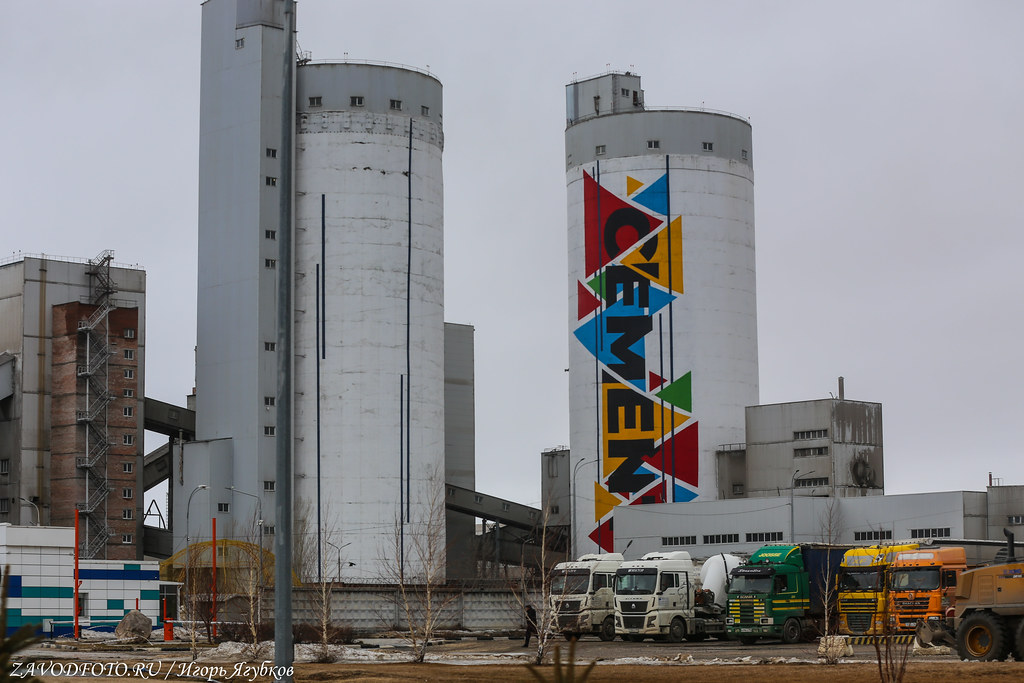
Предприятие полностью автоматизировано. Все производственные участки, от приемки сырья до отгрузки готовой продукции, оборудованы датчиками, сигналы от которых аккумулируются и выводятся на мониторы в центральном пульте управления.
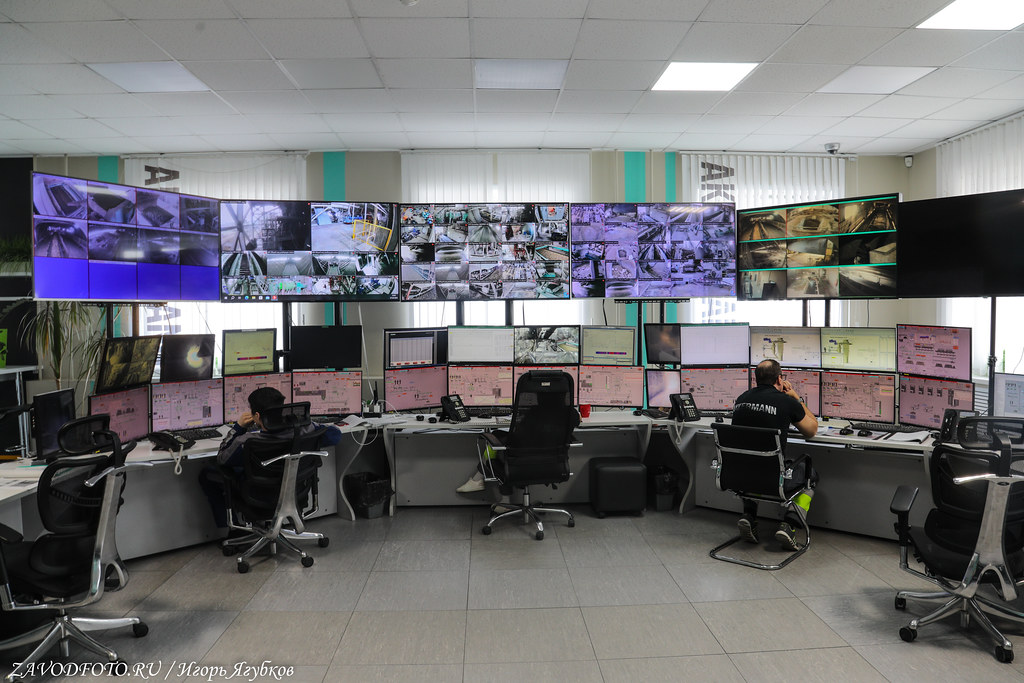
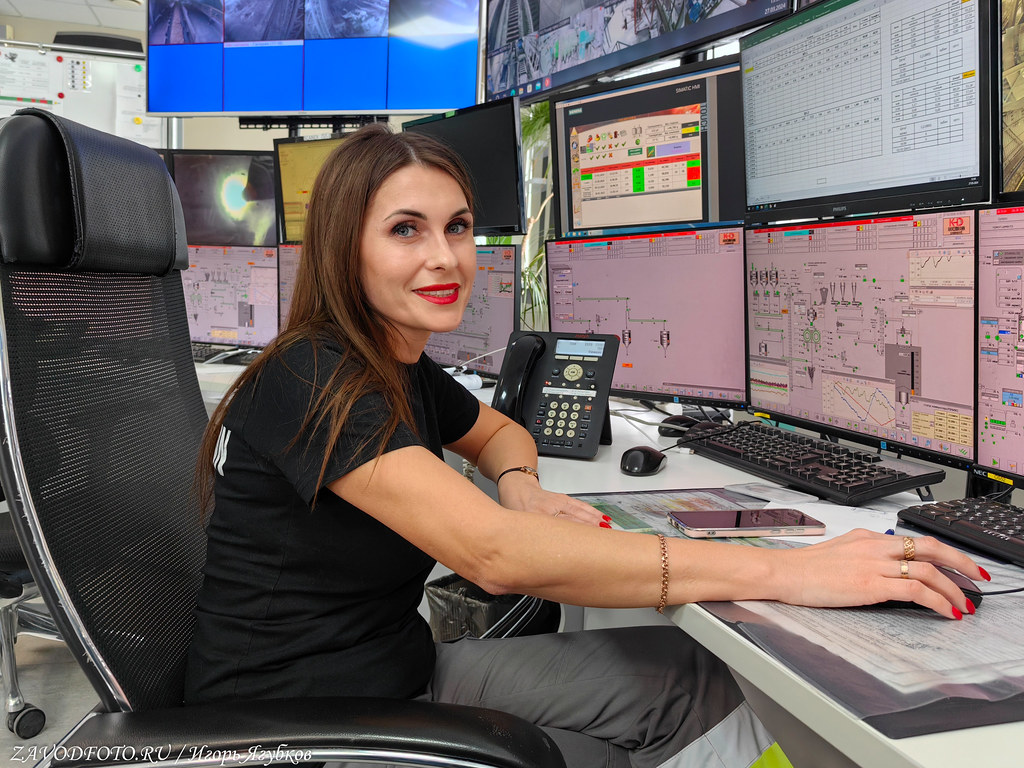
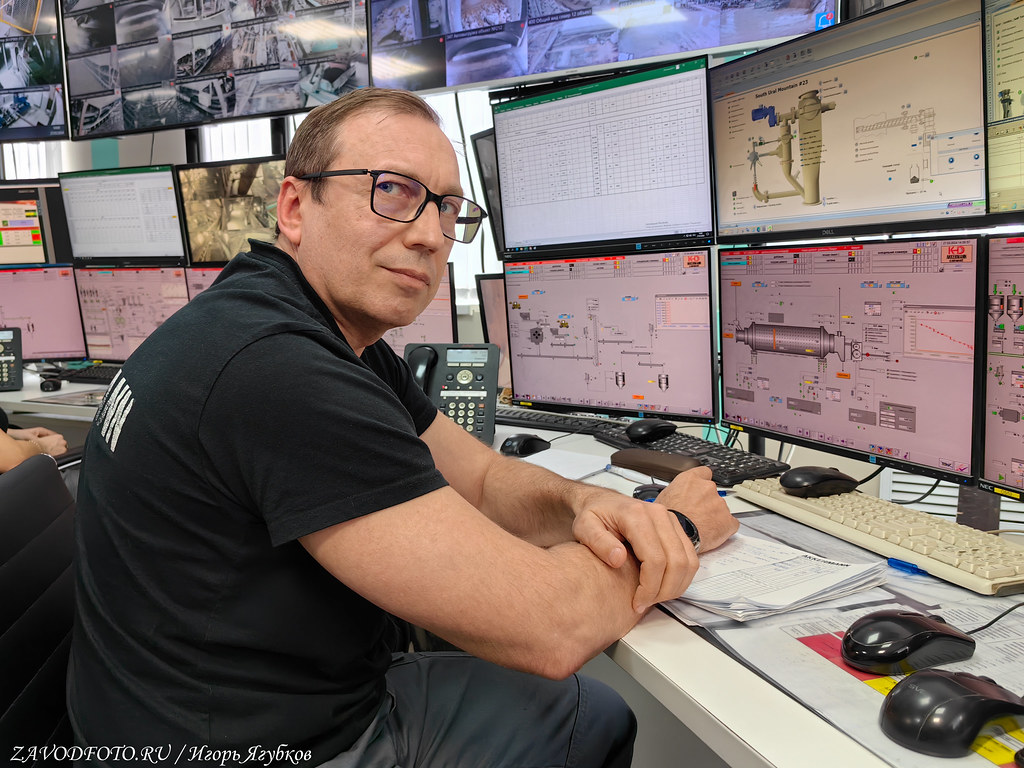
Прямо на ЦПУ можно подвигаться здоровья ради
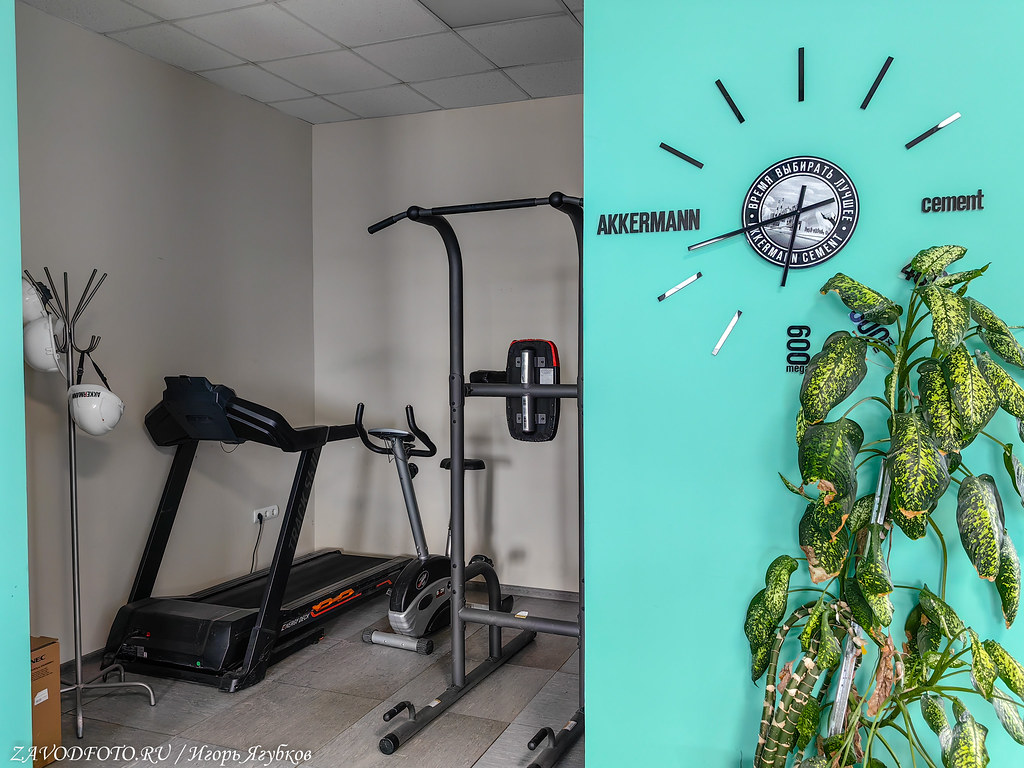
или перекусить...
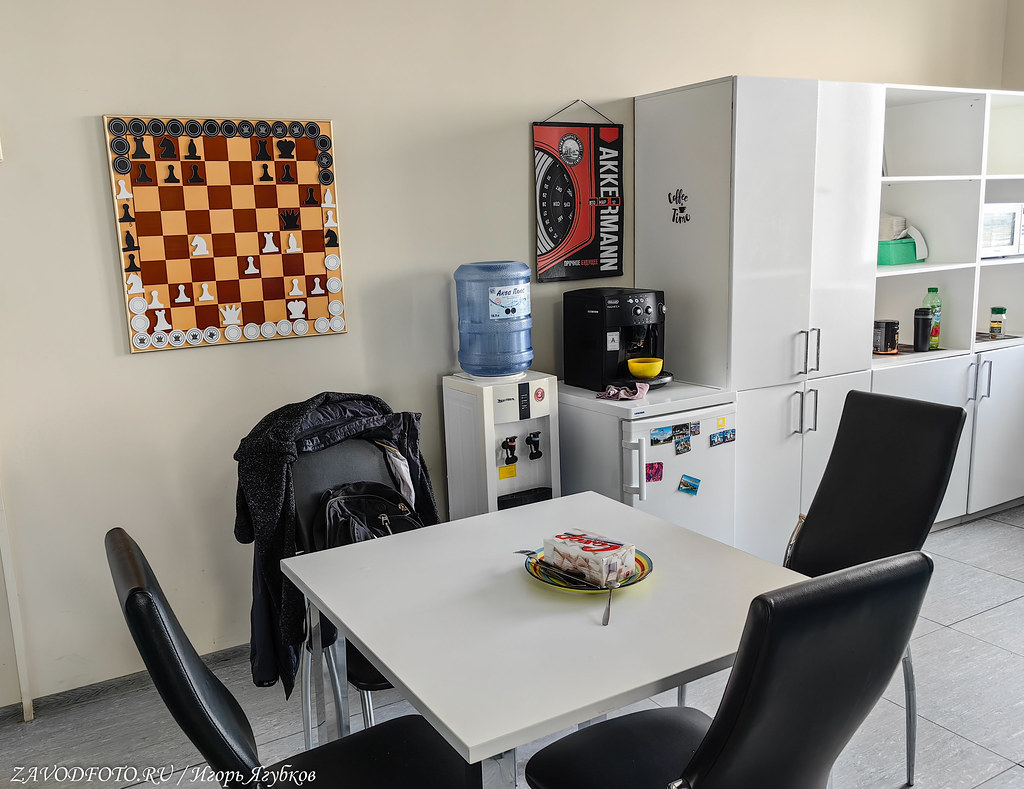
Мощности новотроицкого предприятия позволяют выдавать до 2,3 млн тонн продукции в год. Свой цемент они делают сухим способом. Данная технология более новая. Ведь сухой способ производства (есть еще и мокрый) более экономичен и экологичен, ведь при нем потребляется меньше пресной воды и топлива, а значит экономятся природные ресурсы и снижается уровень выбросов в окружающую среду.
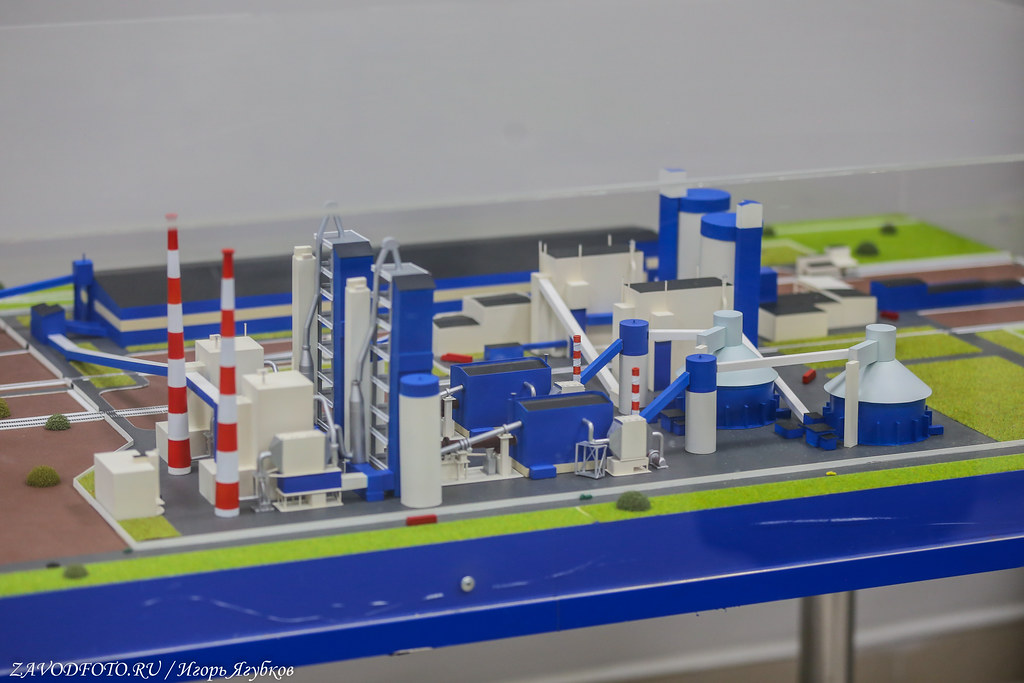
Производство цемента включает четыре основные стадии. Первая стадия - это добыча и подготовка сырьевой смеси. Далее её доводят до ума. На третей стадии сырье обжигают. А на четвертой происходит помол клинкера и добавок. Собственно наш цемент и готов. Стоит отметить, что здесь продукцию делают в том числе по особой технологии. Вместо известняка и глины в цемент добавляют металлургический шлак от «Уральской стали» - таким образом, плюсом перерабатываются отходы производства и не расходуются природные запасы. Завод утилизирует металлургические шлаки в объеме миллиона тонн в год. Запаса этого шлака хватит как минимум на 100 лет. Между прочим, добываемый на Аккермановском месторождением известняк являются первосортным сырьем и считаются лучшими на Урале. Именно он и становится основой цемента, который изготавливается на заводе «АККЕРМАНН ЦЕМЕНТ».
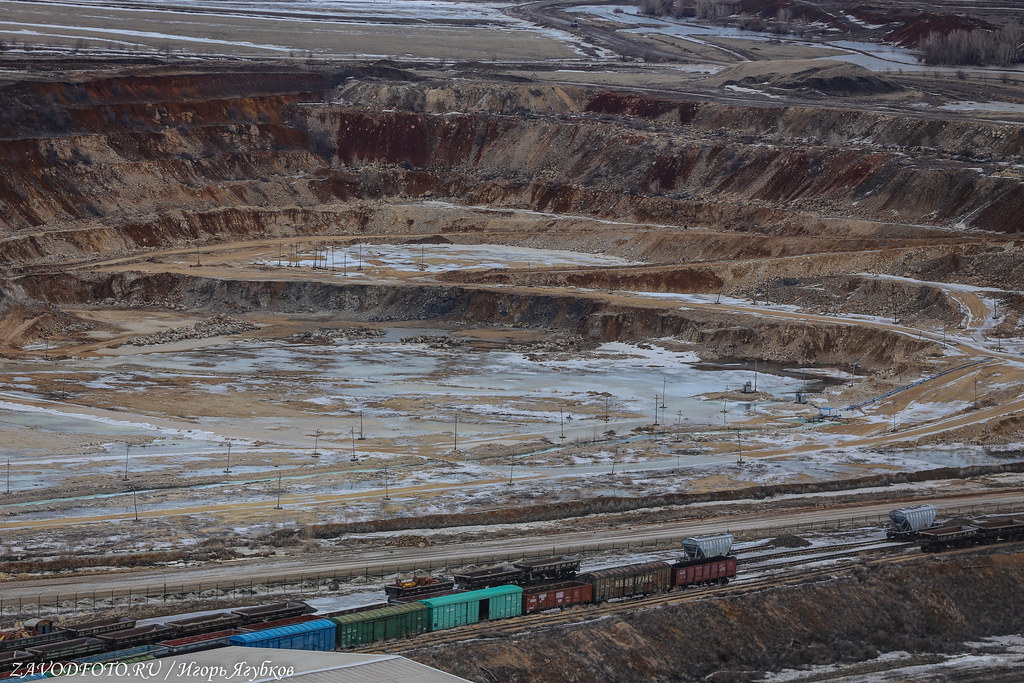
Итак, сырьем для производства цемента выступают известняк, глина и металлургические шлаки (отходы металлургического производства, доменного и электроплавильного). Известняк, добытый в карьере, дробится и подается на склад известняка. К нему далее добавляется около 12 % глины. Таким образом, получается смесь, которую называют микс. Её далее отправляют на другой объединенный склад. Объединенный склад у них разделен на две части, одна часть для микса, а другая часть для шлаков. На каждой из частей формируются по два штабеля. Пока один формируется, другой отправляется в производство. Далее всё сырье подается в отделение помола и сушки, чтобы эту смесь превратить в муку.
Один из складов сырья.
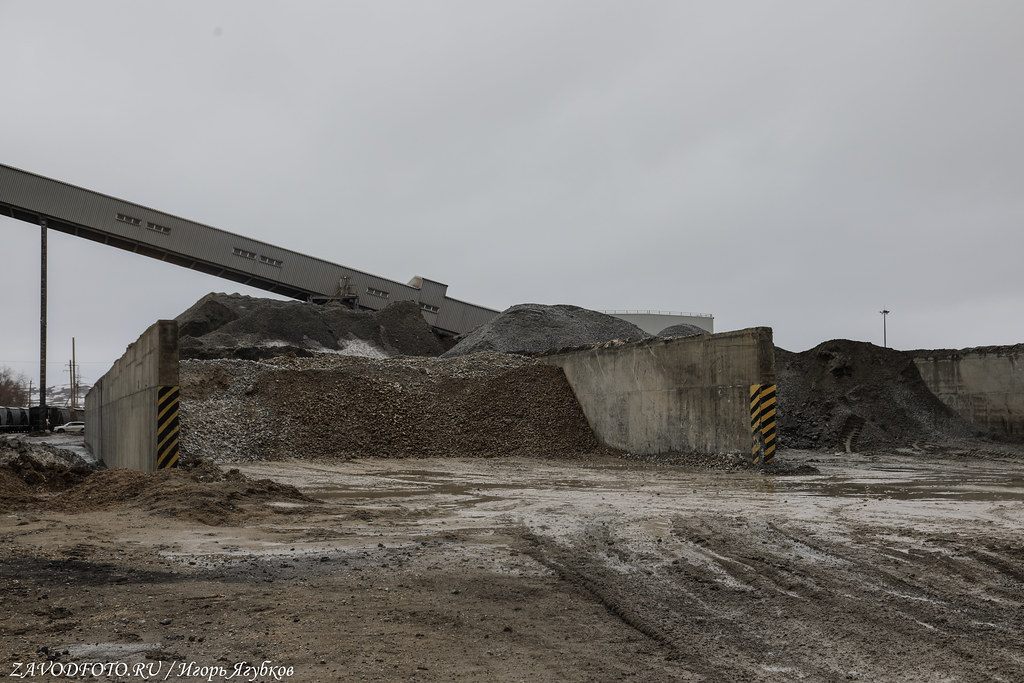
Для производства сырьевой муки используется роллер-пресс. Примерная дозировка микса шлака доменного и шлака ЭСПЦ (электросталеплавильного) составляет 70 %, плюс 25 % чисто доменного и 5 % шлака ЭСПЦ. Всего на предприятии две совершенно одинаковые производственные линии. Вот как раз мы сейчас находимся в отделении помола и сушки сырья, где работает роллер-пресс первой линии.
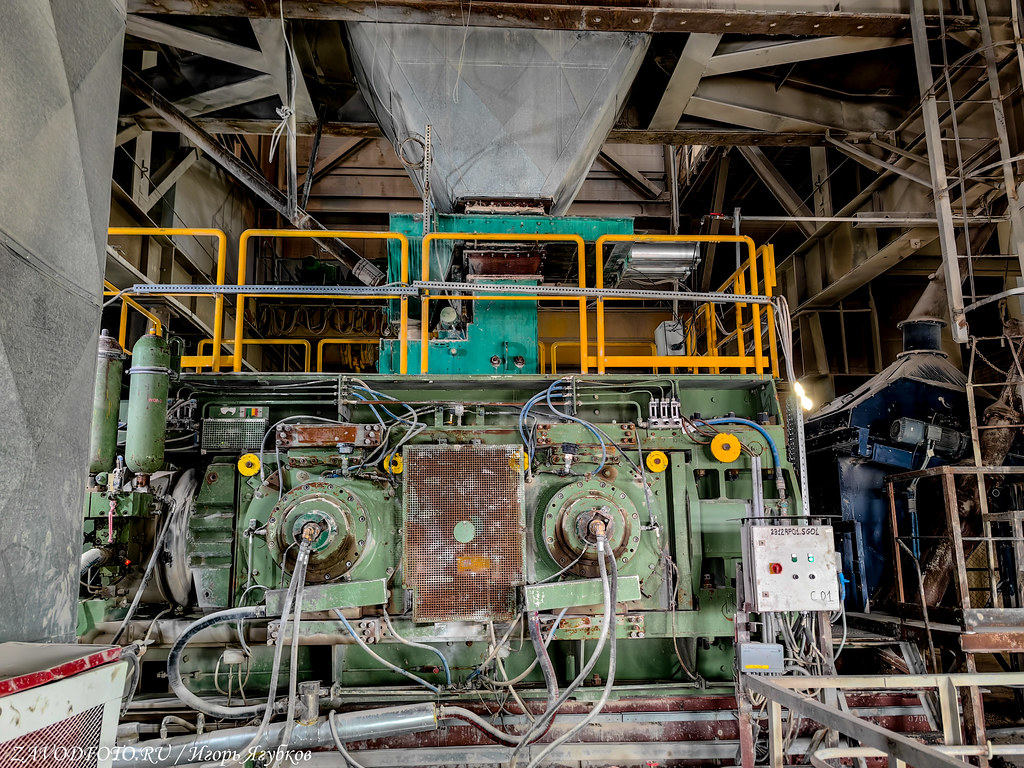
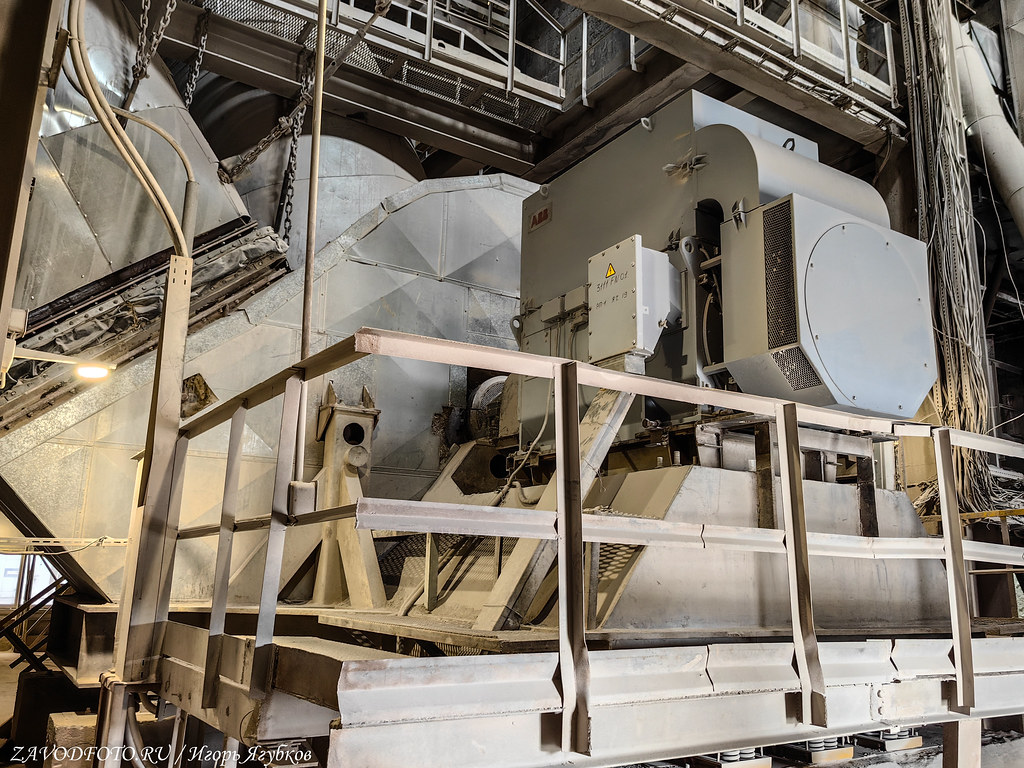
Это самый большой бункер для подачи известняка и глины. Порядка 70 % подается этого компонента. Бункер микса вмещает 600 тонн.
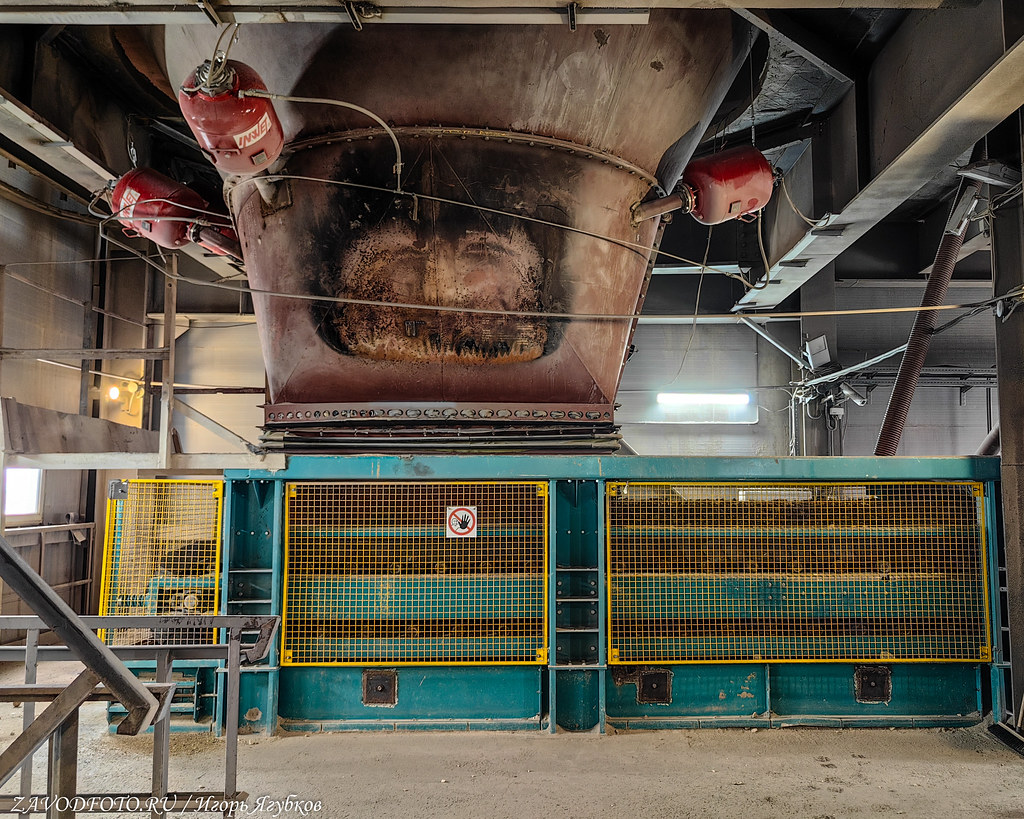
По соседству ещё два бункера поменьше со шлаками металлургического производства. Эти бункера вмещают в себя по 150 тонн.
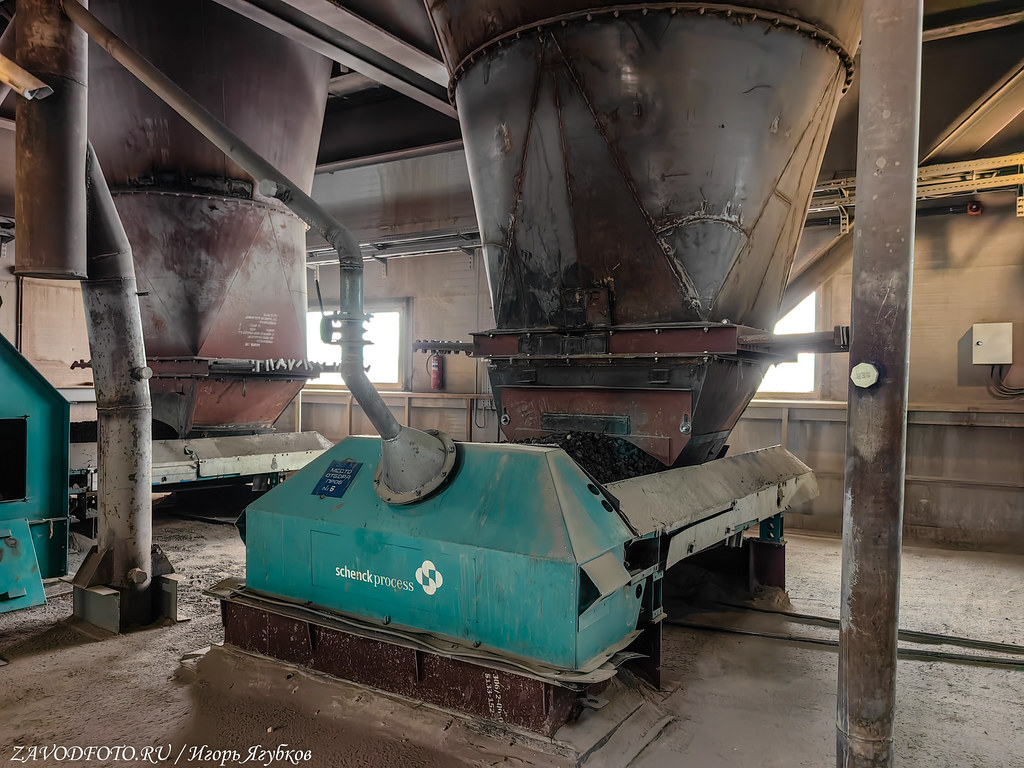
Вся эта солянка по конвейеру подается и в итоге смешивается. Специальный металлосепаратор отслеживает, чтоб ненужные частицы не попали в работу.
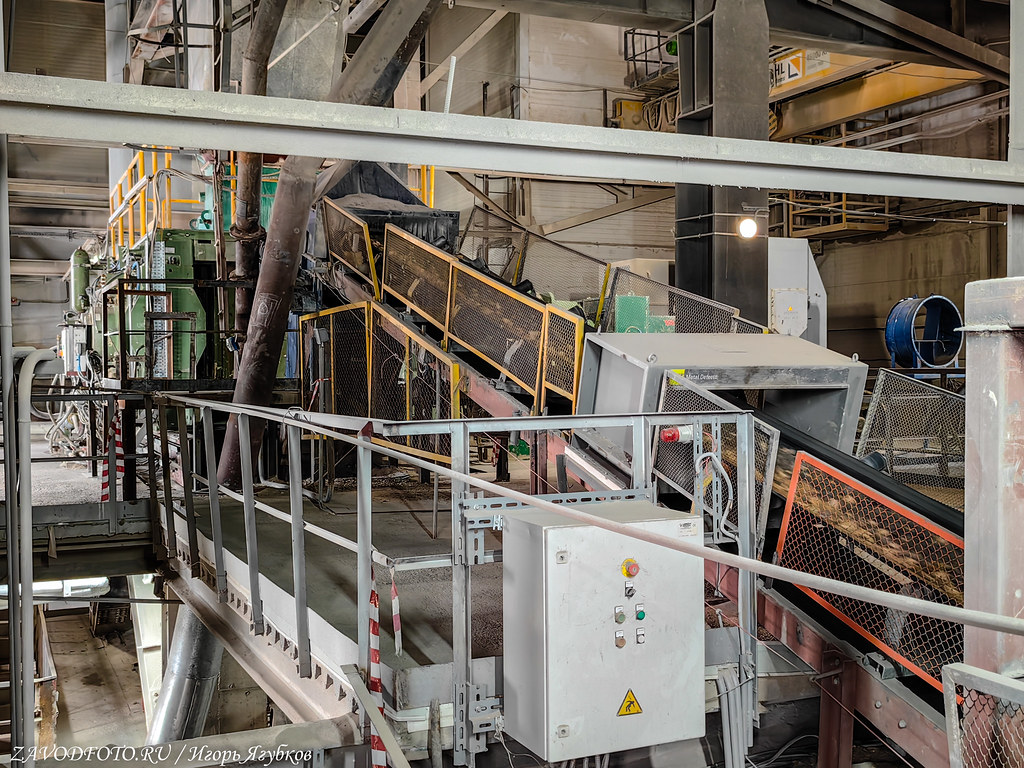
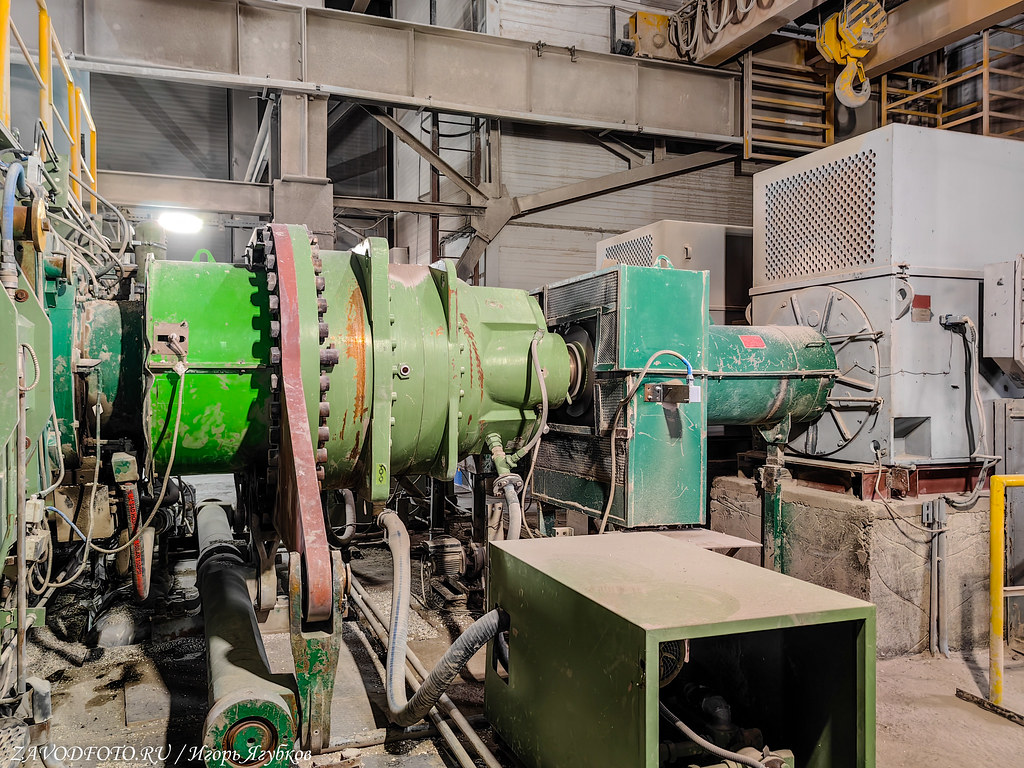
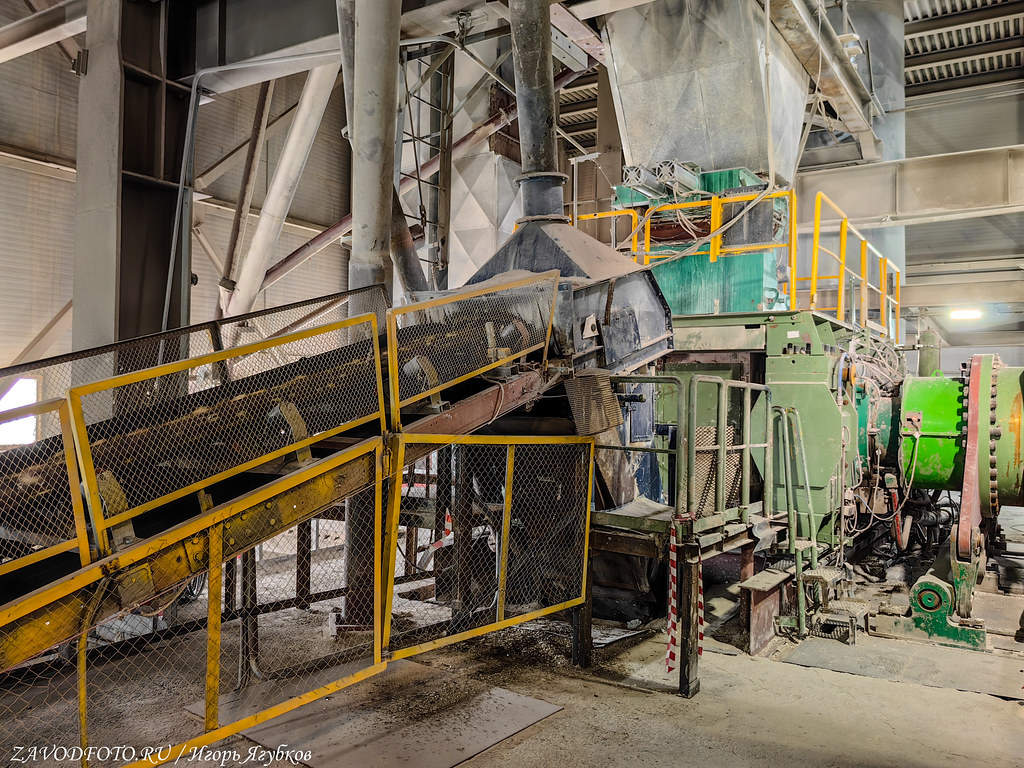
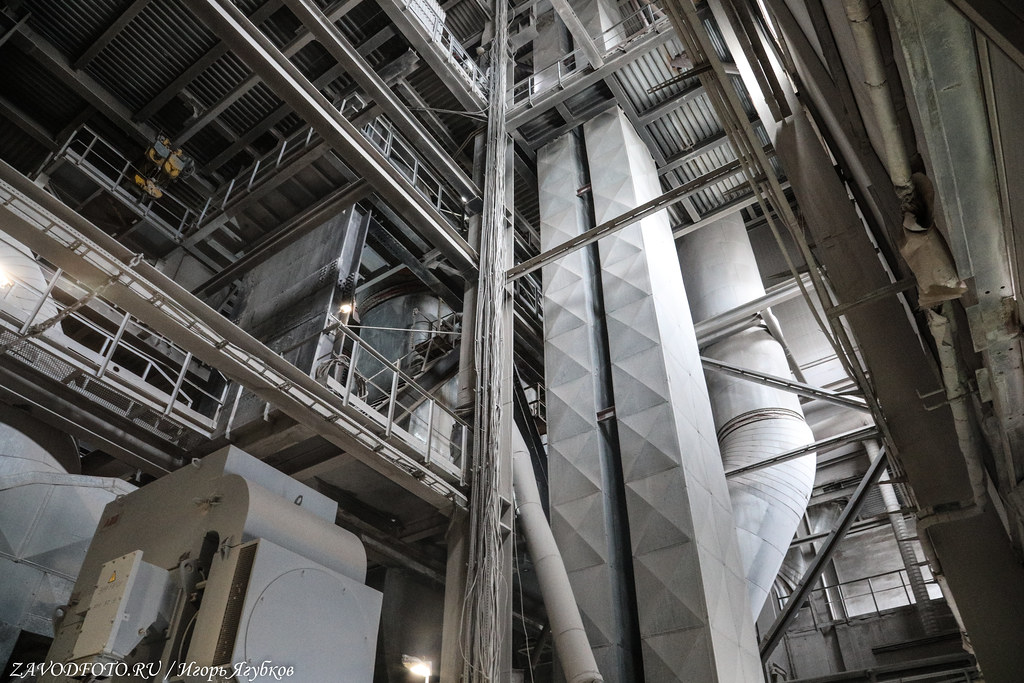
На этом участке идет оперативный отбор проб муки, и по пневмопочте заборы отправляются сразу в лабораторию.
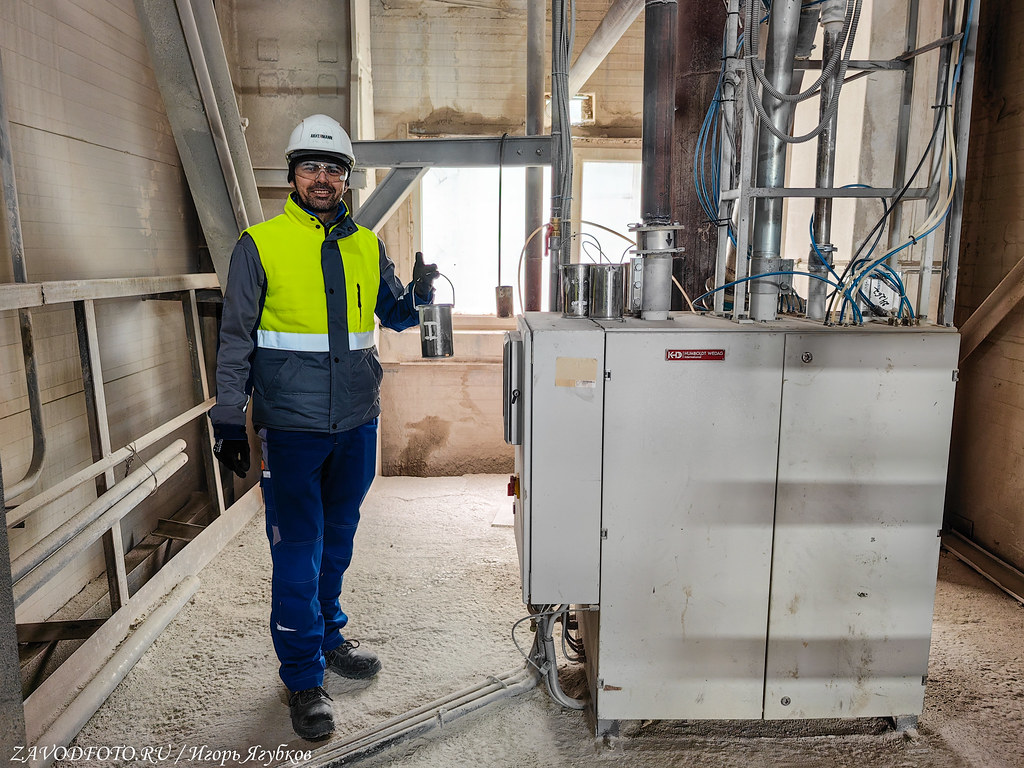
На следующей стадии эстафету подхватывают вращающие печи длиной 62 м. В них происходит процесс обжига клинкера. Обжиг смеси и получение клинкера - это самая важная стадия. Всё дело в том, что эксплуатационные свойства цемента напрямую зависят от качества клинкера, температуры и времени обжигания. Так как в естественных условиях основные компоненты сырьевой смеси не вступают в химическую реакцию друг с другом, поэтому процесс взаимодействия между глиной, известняком и другими компонентами запускается при нагревании.
Температура в печах может достигать до 1400°C. Сырье на максимальной производительности в печи находится порядка 20-25 минут.
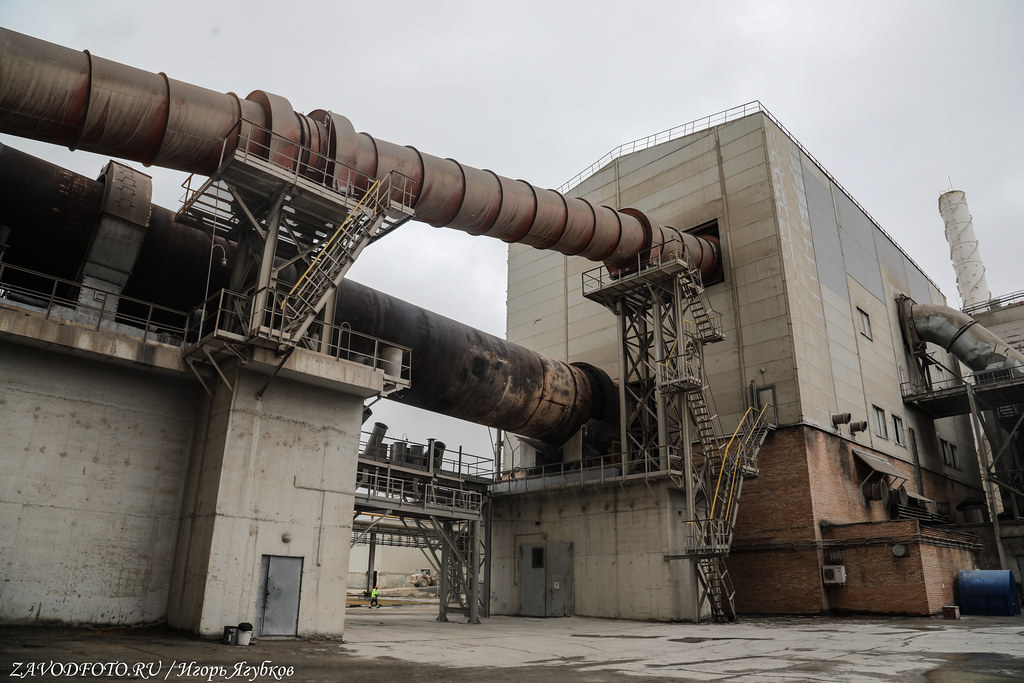
По мере прохождения сырья через печь происходят различные сложные химические реакции. Декарбонизация: известняк (карбонат кальция) разлагается на оксид кальция (негашеную известь) и углекислый газ. Дегидратация: вода удаляется из глинистых (алюмосиликатных) минералов, что приводит к образованию алюмината кальция и силикатных соединений. Реакция железной руды. Железная руда реагирует с оксидом кальция с образованием феррита кальция, важнейшего компонента цементного клинкера.
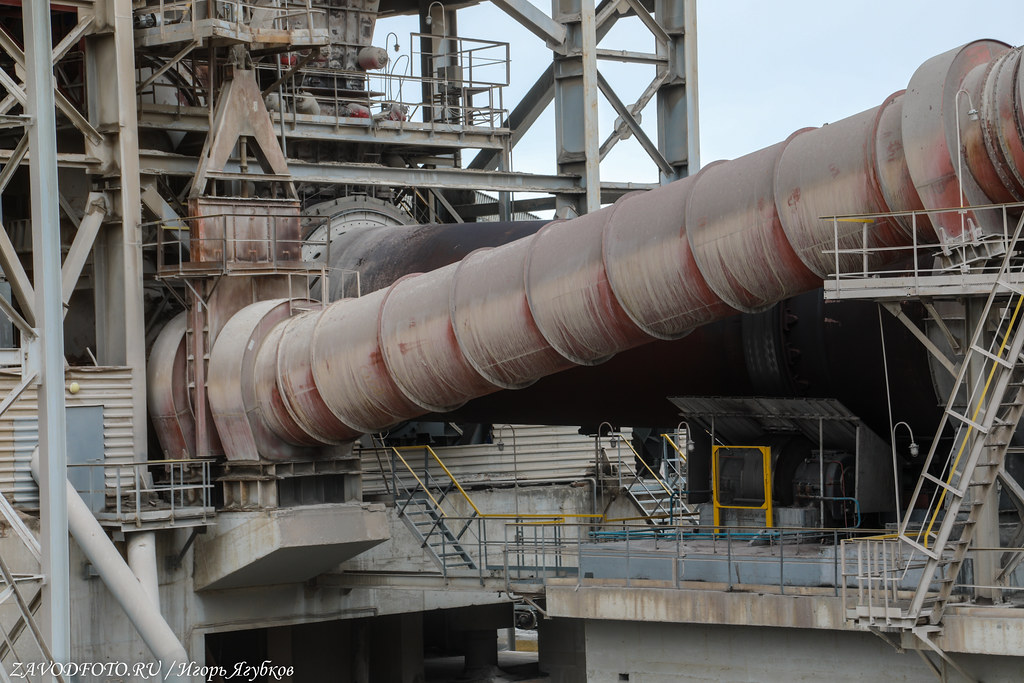
Кстати, печи сухого способа производства примерно в два раза короче печей мокрого способа при равной или даже большей производительности. Уменьшение длины печи связано с двумя основными факторами: во-первых, в печах сухого способа в принципе отсутствует зона сушки, во-вторых, часть процессов выносится из печи в запечные теплообменные устройства.
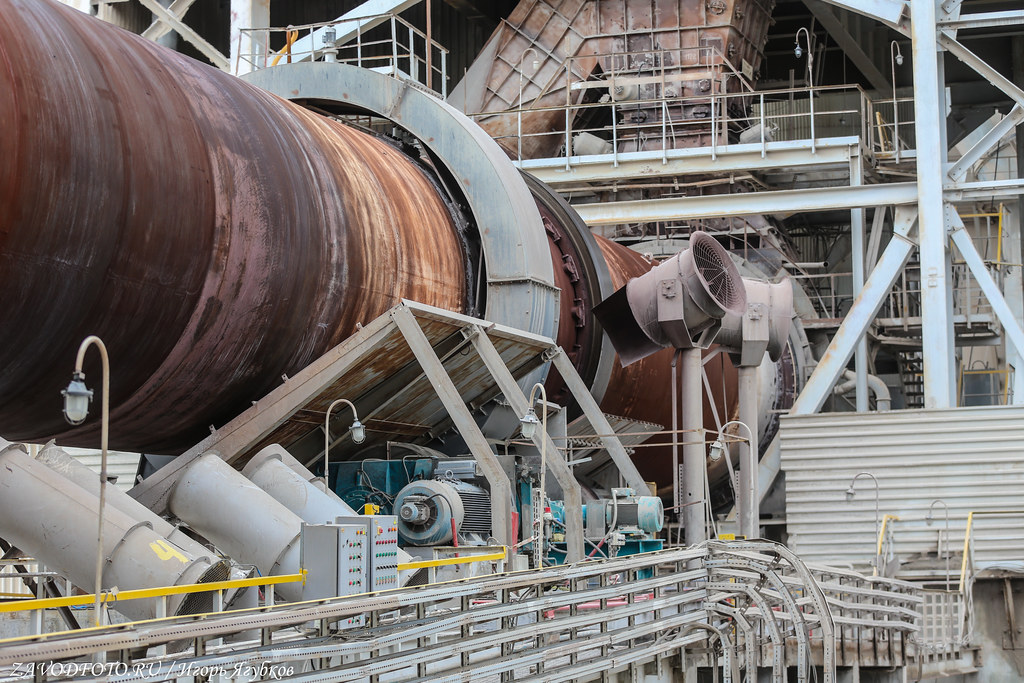
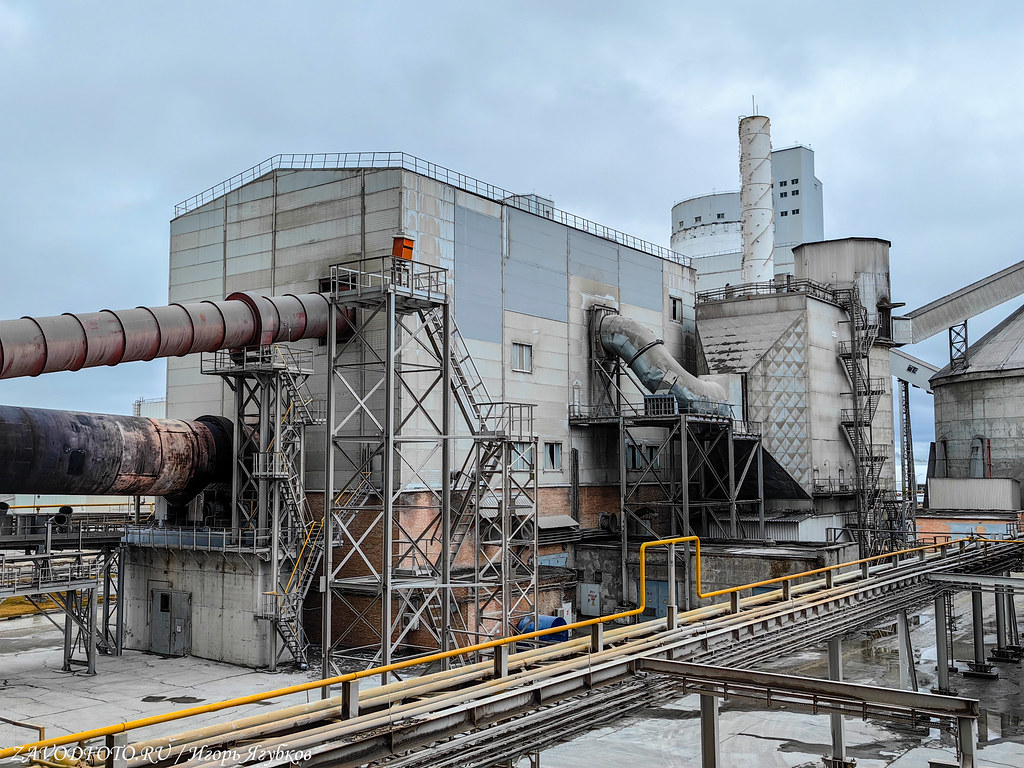
Чтобы с природой шутки не шутить, на заводе предусмотрены электрофильтры для очистки отходящих газов от пыли.
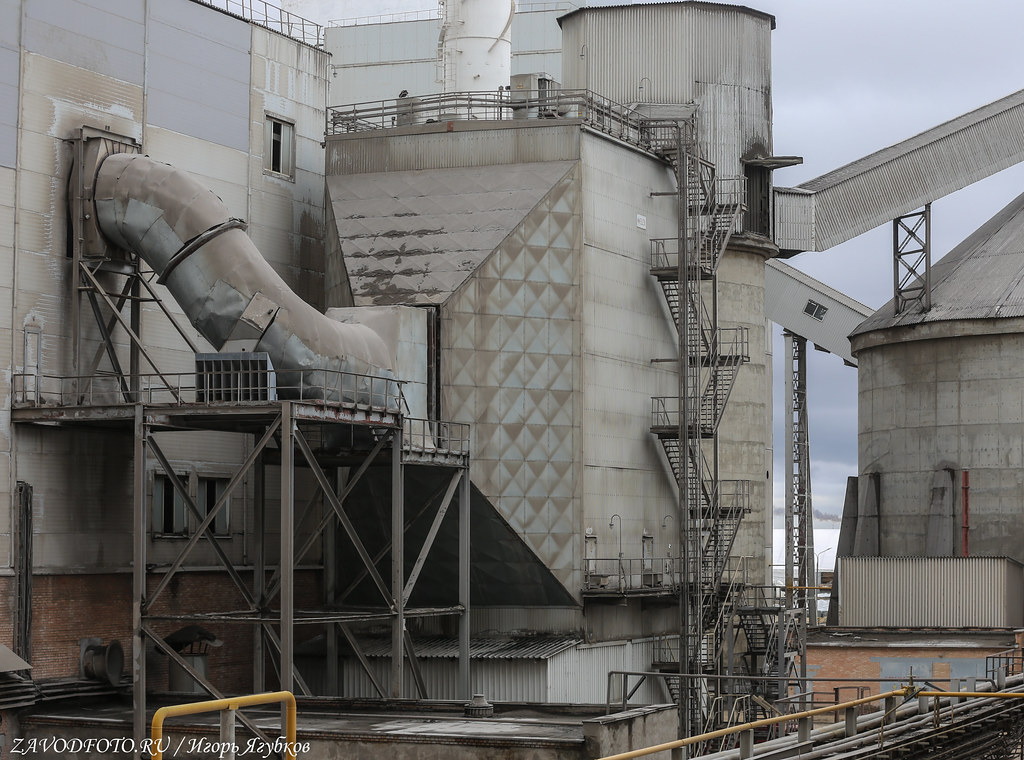
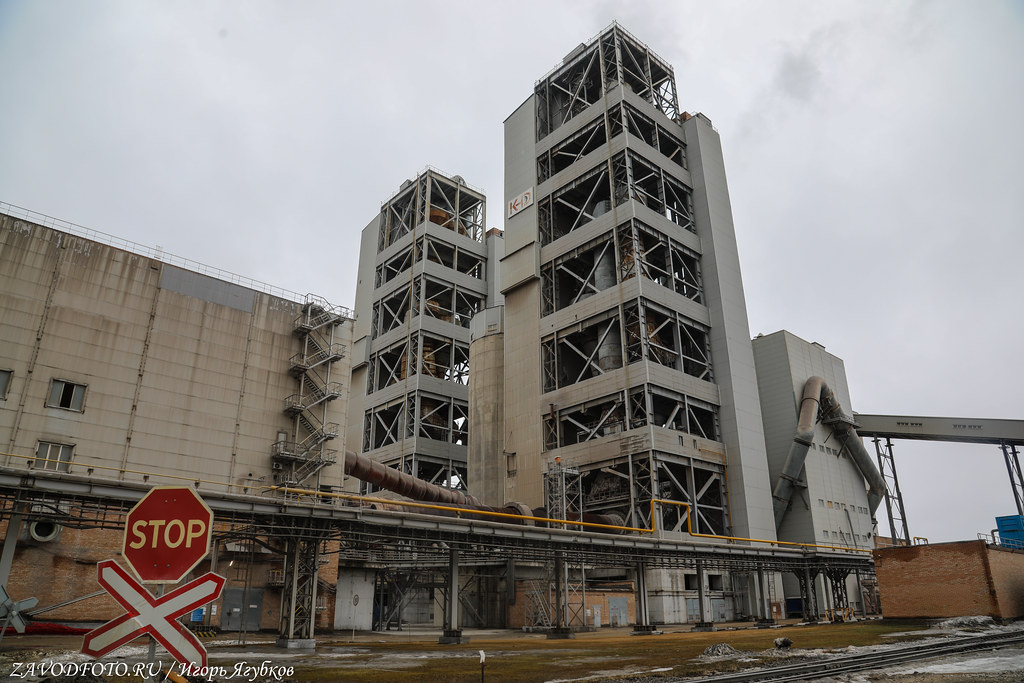
Что ещё для счастья надо? Правильно - залезть повыше. Мы на высоте где-то 140 метров.
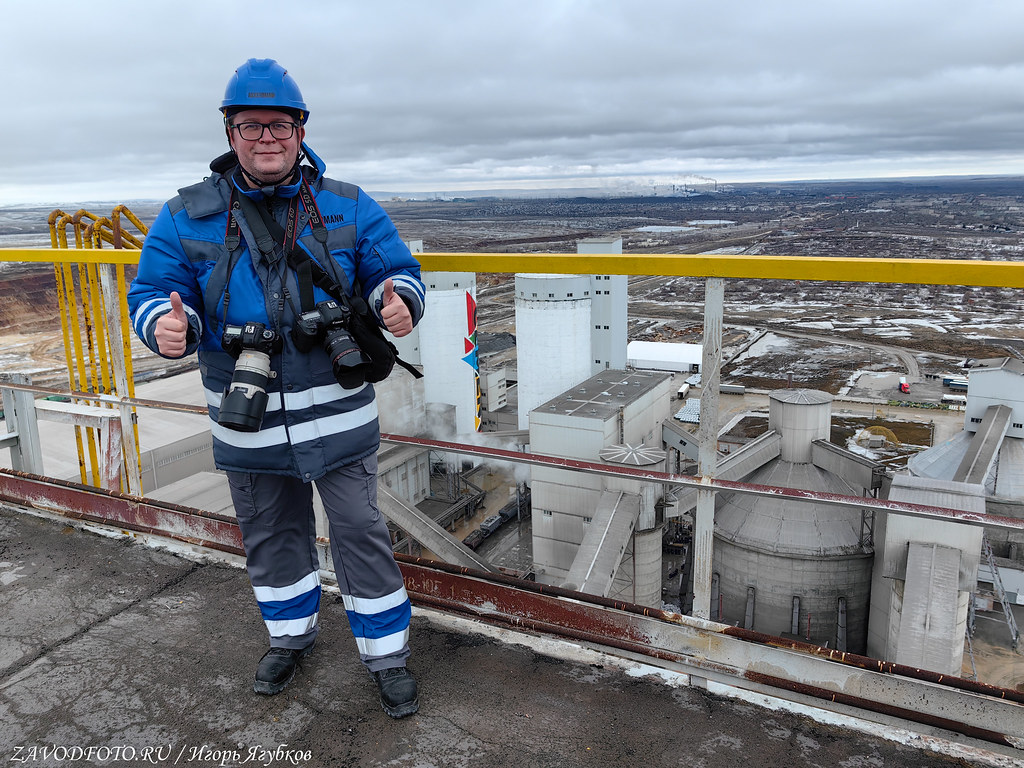
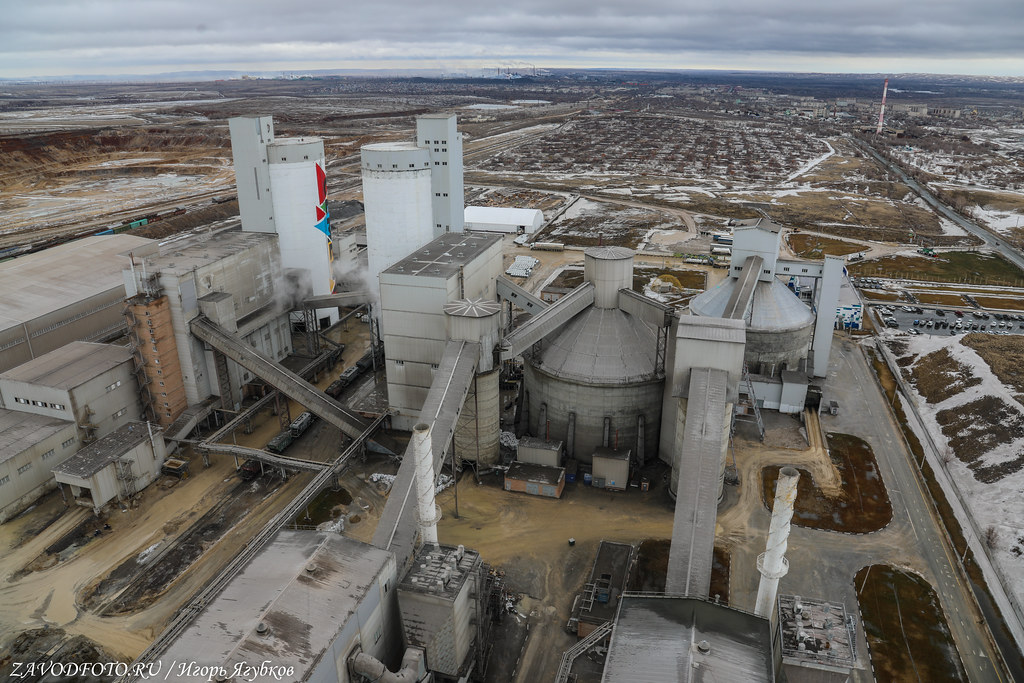
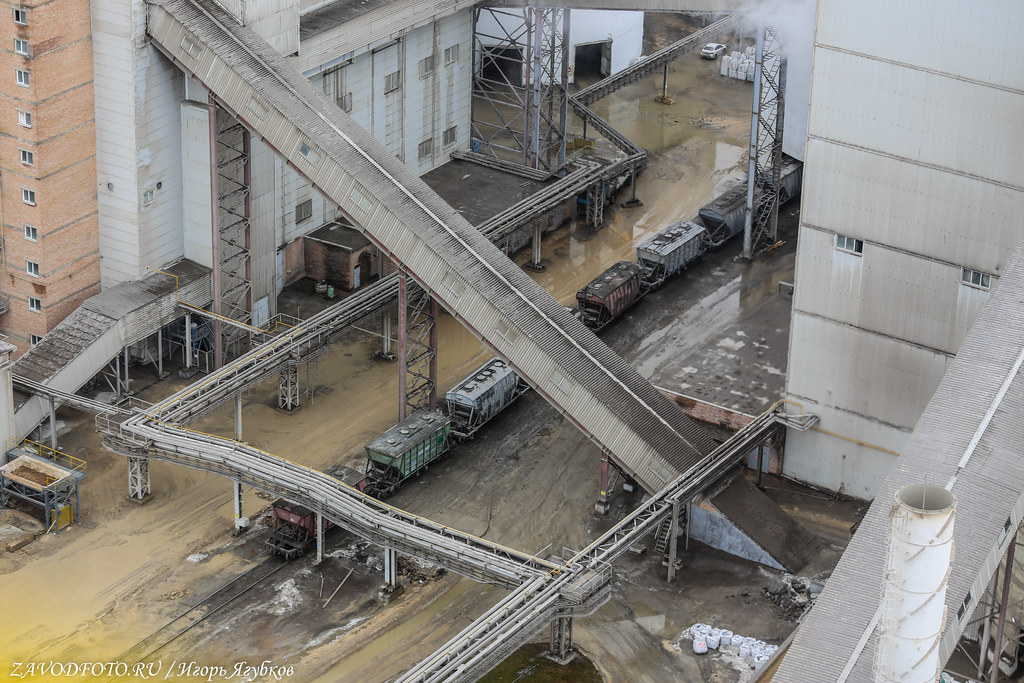
Эти два великана - многосекционные силосы для цемента. Внизу у них предусмотрена отгрузка в ж/д и автотранспорт.
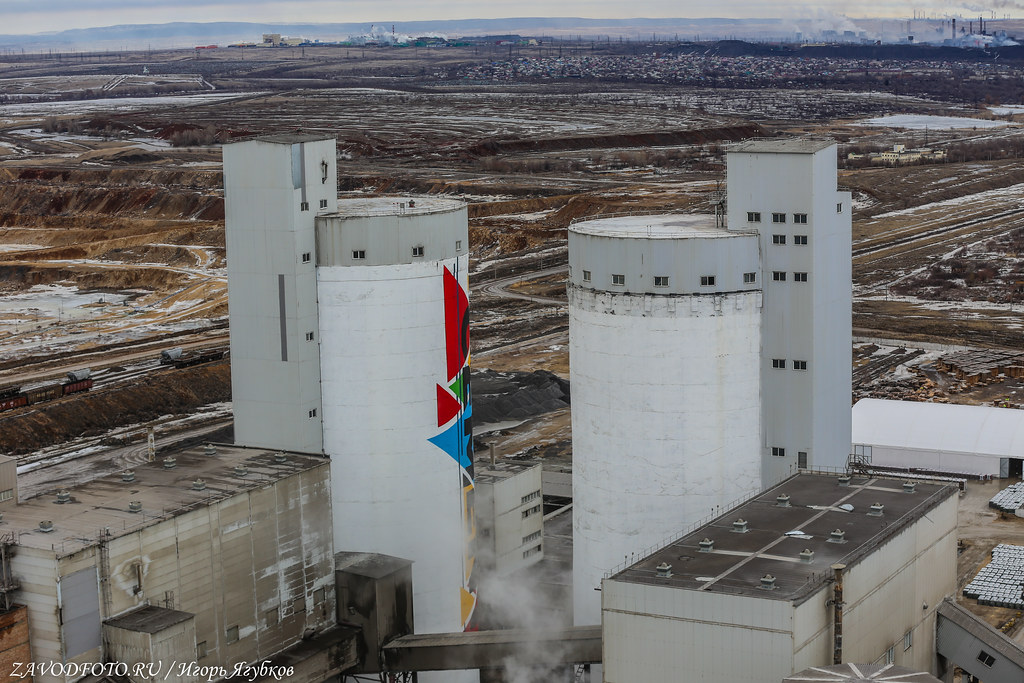
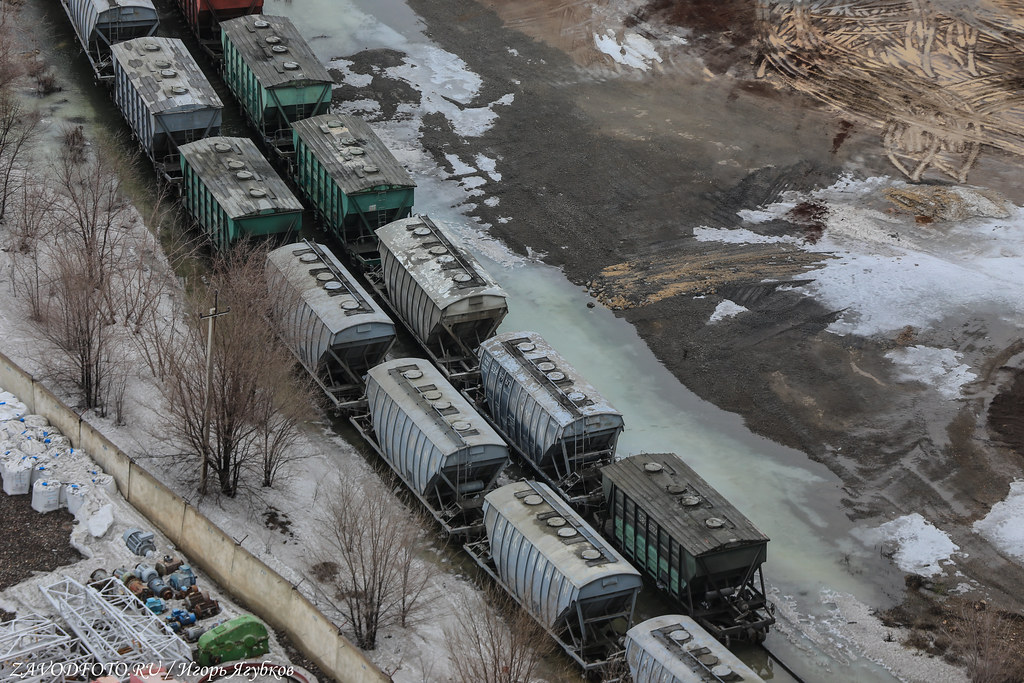
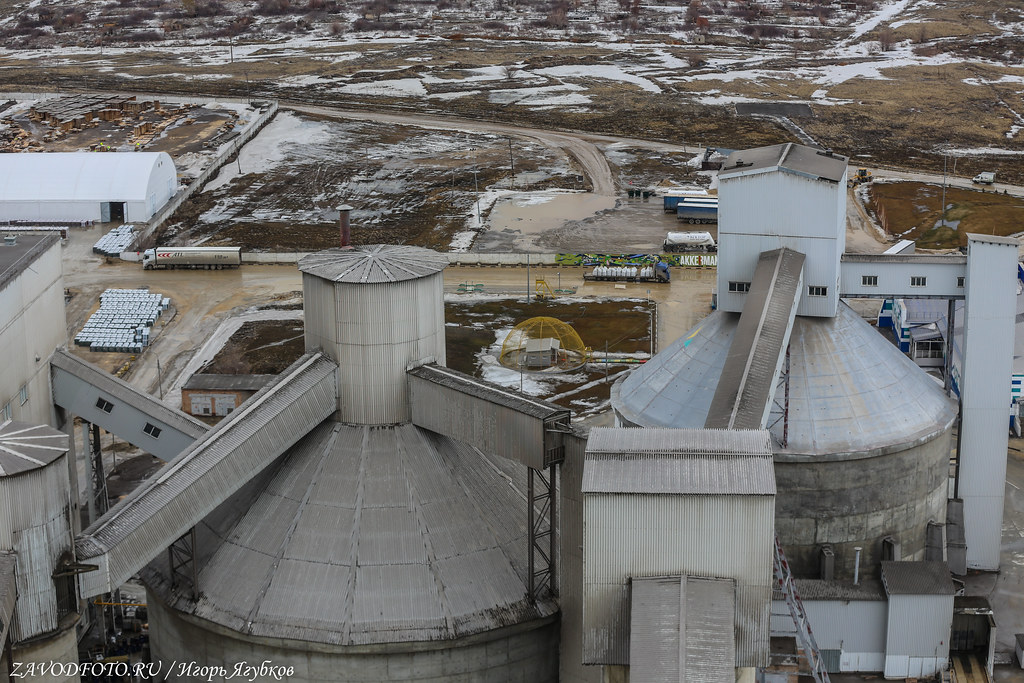
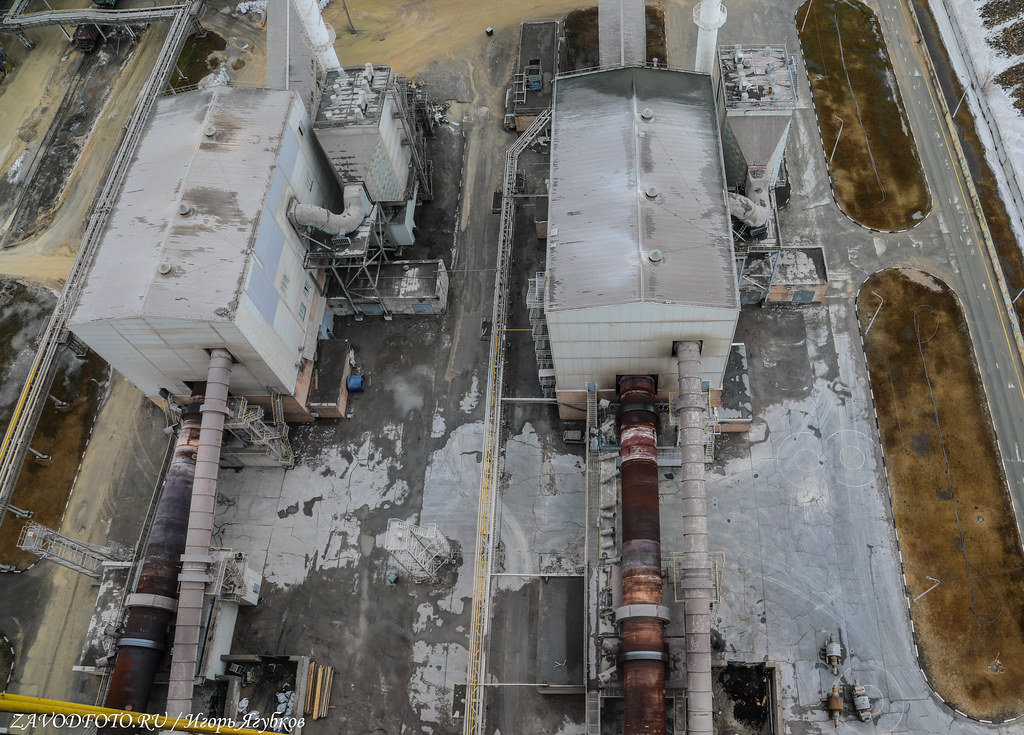
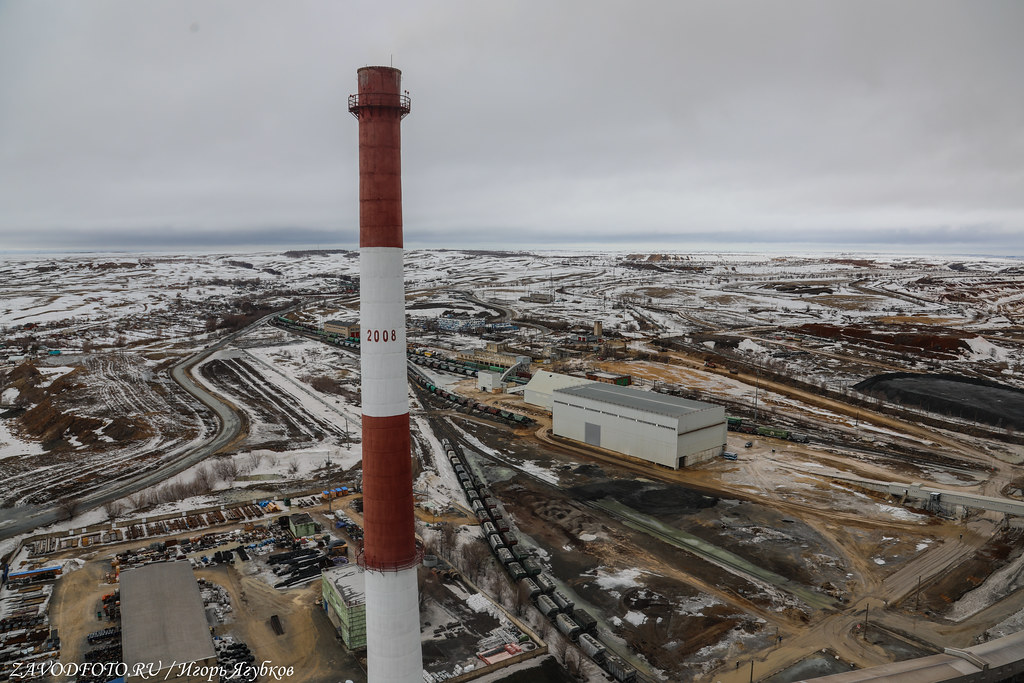

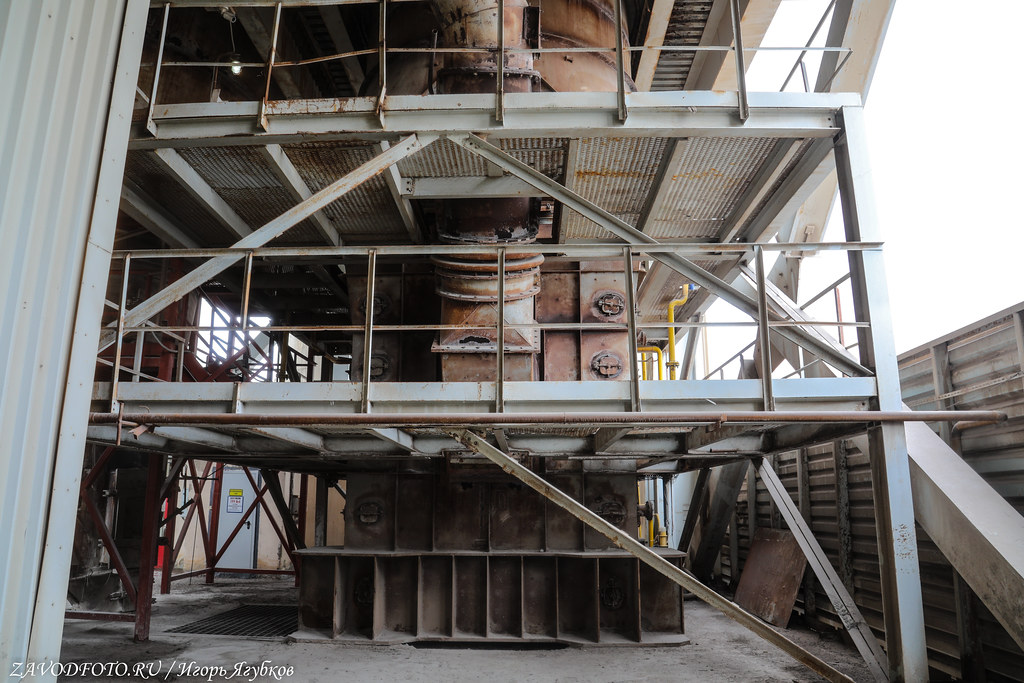
Перед нами главная горелка печи. Потребляет в среднем 5 000 м3 газа в час. В час она производит около 106 тонн клинкера в час. Цементный клинкер является основным ингредиентом в производстве цемента. Как мы уже поняли, это мелкий порошок, получаемый путем нагревания смеси известняка, глины и других минералов при высоких температурах. Впервые он был получен французом Луи Вика в 1817 году. Название клинкер происходит от его сходства с обожженным кирпичом (Клинкерный кирпич).
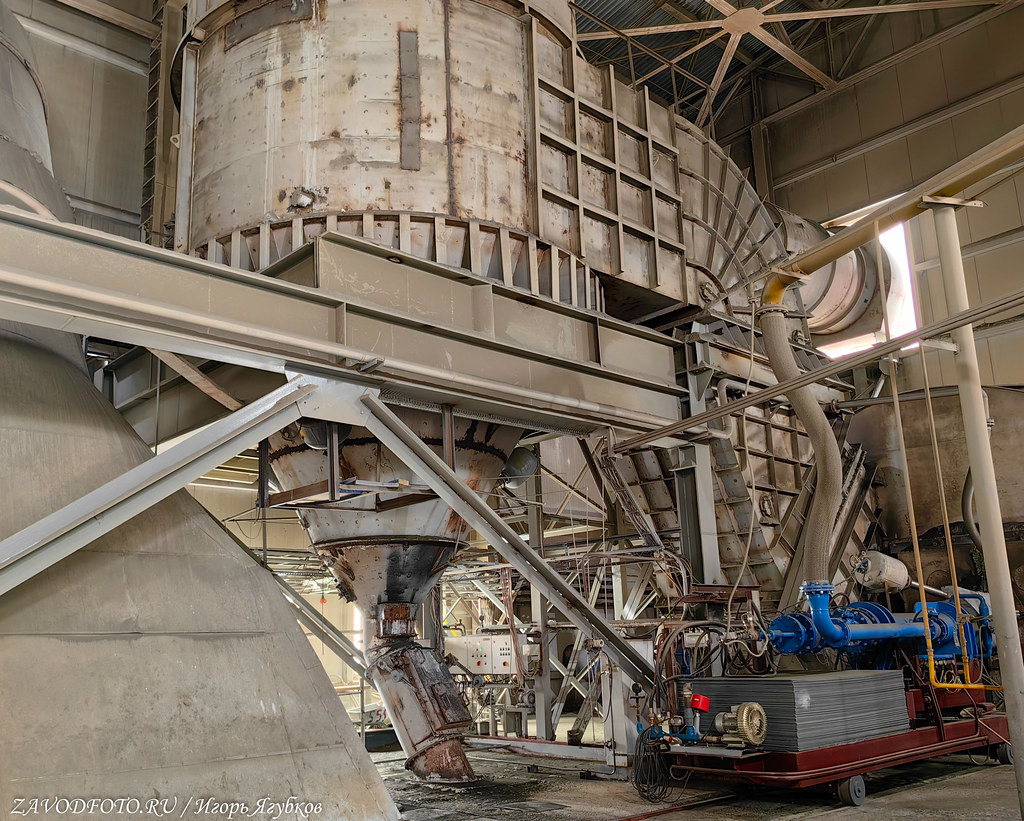
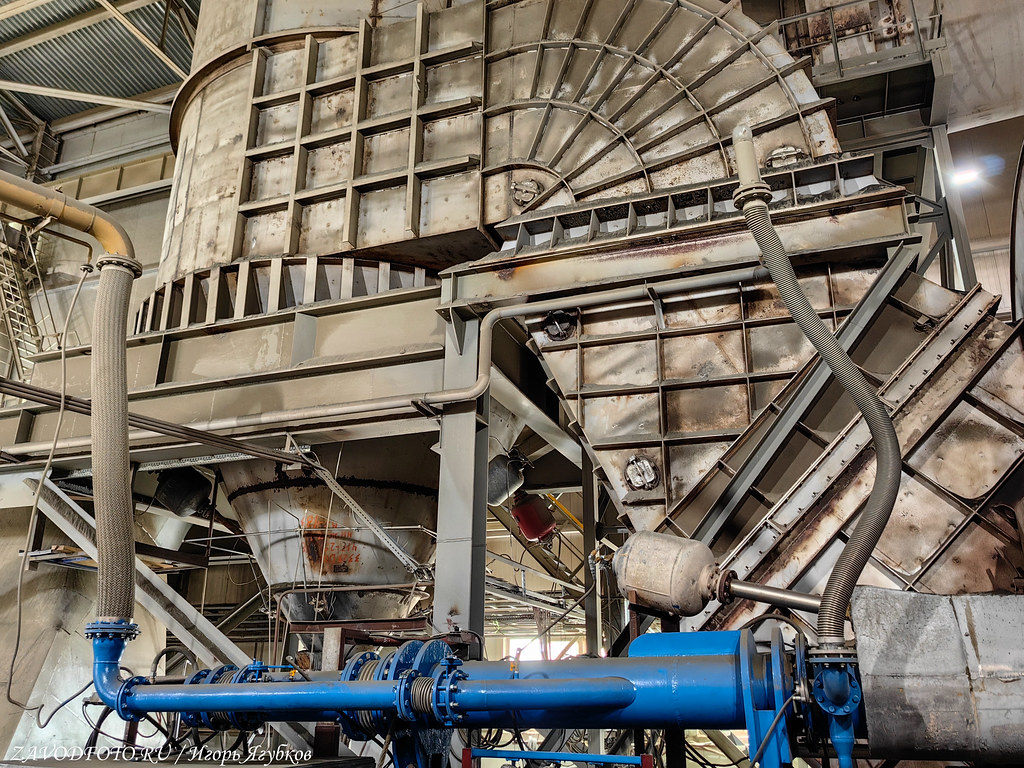

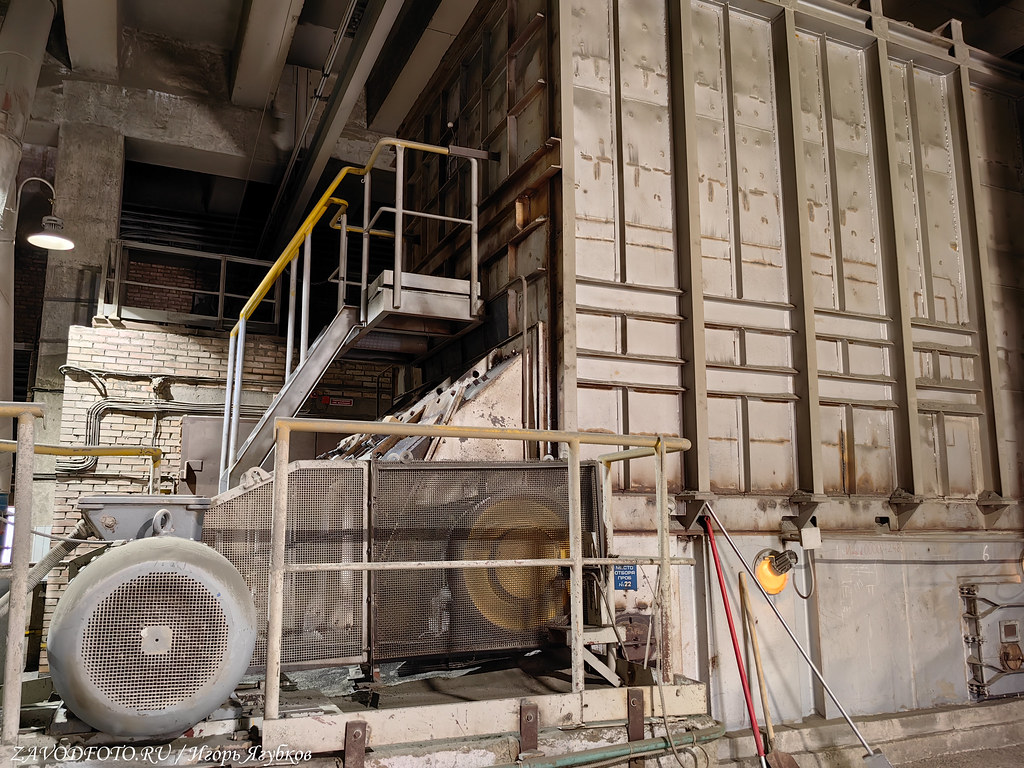
А это умный анализатор свободной извести по имени KLC 3. Вообще на предприятии много времени и сил отдают проверке на качество. К примеру, в соответствии с технологической документацией производства сырьевые материалы отбираются до 3-4 раз в смену, а пробы цемента и клинкера - каждые 2 часа. Оперативный контроль качества обжига клинкера осуществляют путем определения содержания свободной окиси кальция в клинкера, как химическим, так и петрографическим методом. Методом рентгеновской дифракции традиционно определяется фазовый состав материалов. Кроме того, рентгеновская дифрактометрия является наиболее прямым и эффективным способом определения количественных соотношений кристаллических и аморфных фаз материалов, определения их микроструктурных свойств, таких, как размеры кристаллитов, микродеформации, а также величина остаточных напряжений.
Не секрет, что повышенное содержание щелочей в цементе (более 0,8%) вызывает щелочную коррозию бетона, а это способствует образованию трещин. А повышенное содержание свободной окиси кальция CaOсв (более 1,5%) и окиси магния MgO (более 5%) оказывает значительное влияние на равномерность изменения объема при твердении цемента, вызывает усадочные деформации в бетонах. Повышенное содержание хлор-ионов Cl- - более 0,1% сказывается на возникновении коррозии арматуры в бетоне. Тонкость помола, гранулометрический состав цемента и удельная поверхность влияет на показатель НГЦТ, а, соответственно, на водопотребность цемента и бетонной смеси. Чем тоньше помол – тем больше воды потребляет цемент, и тем активнее происходит процесс гидратации. Сроки схватывания позволяют оценить время живучести (сохраняемости свойств) бетонной смеси, то есть в течение какого времени она останется подвижной и ее можно будет без проблем уложить в опалубку.
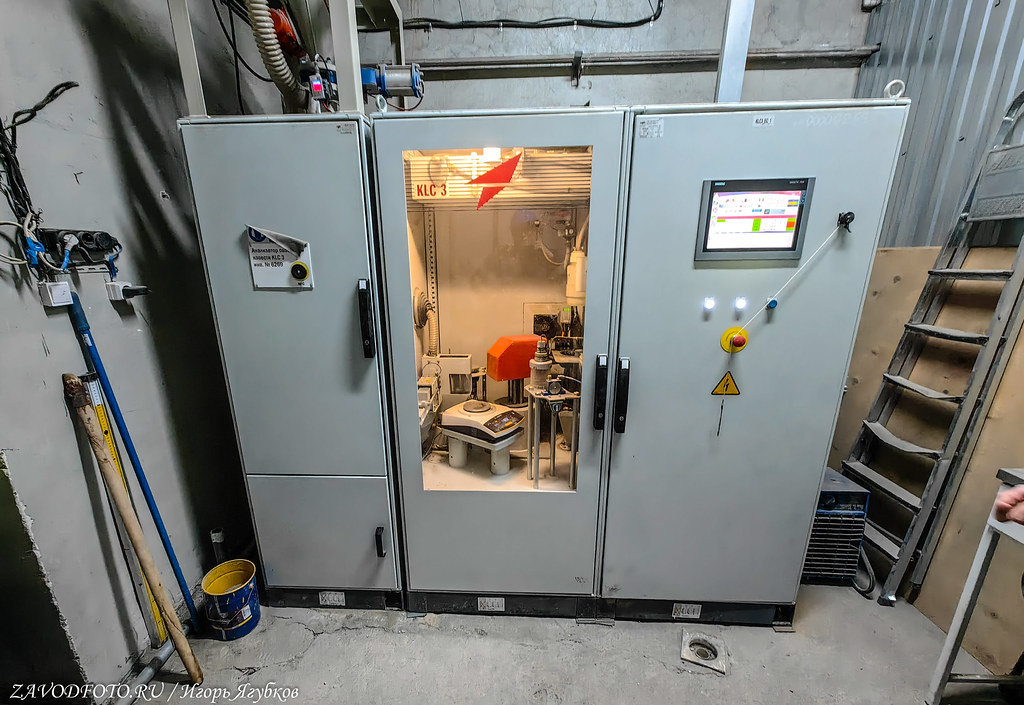
Далее клинкерную массу охлаждают, и отправляют в силосы ожидать дальнейшей переработки.
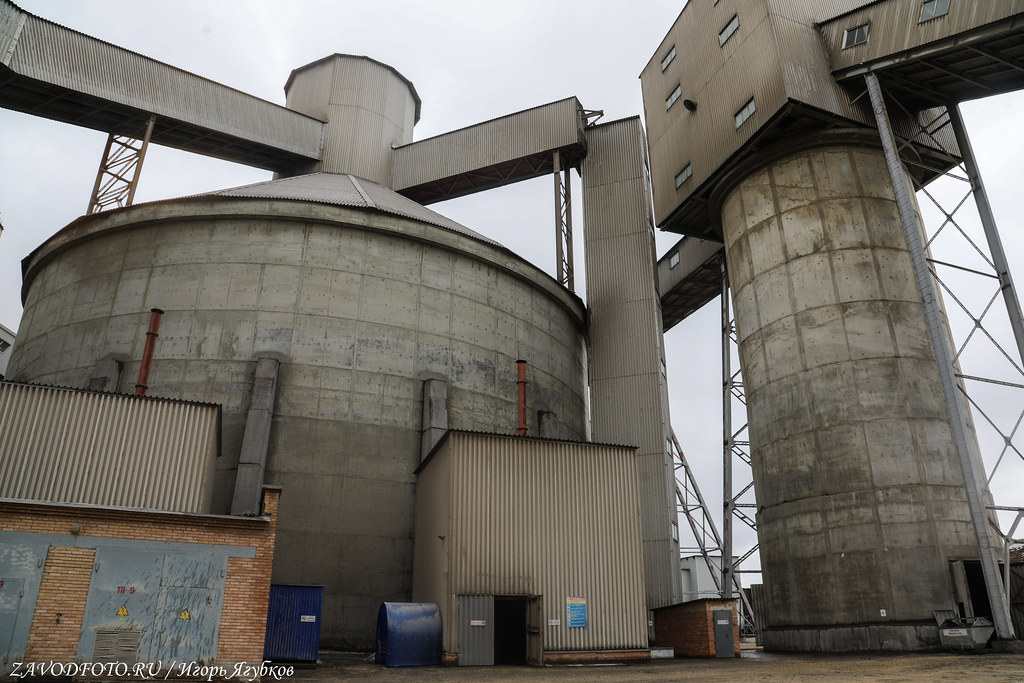
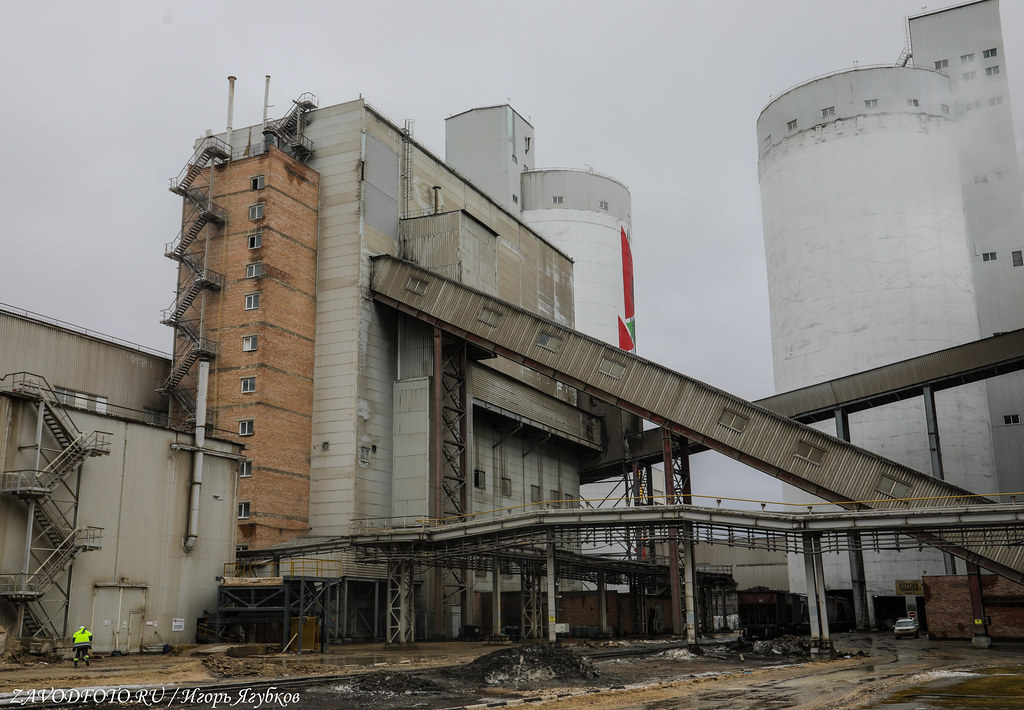

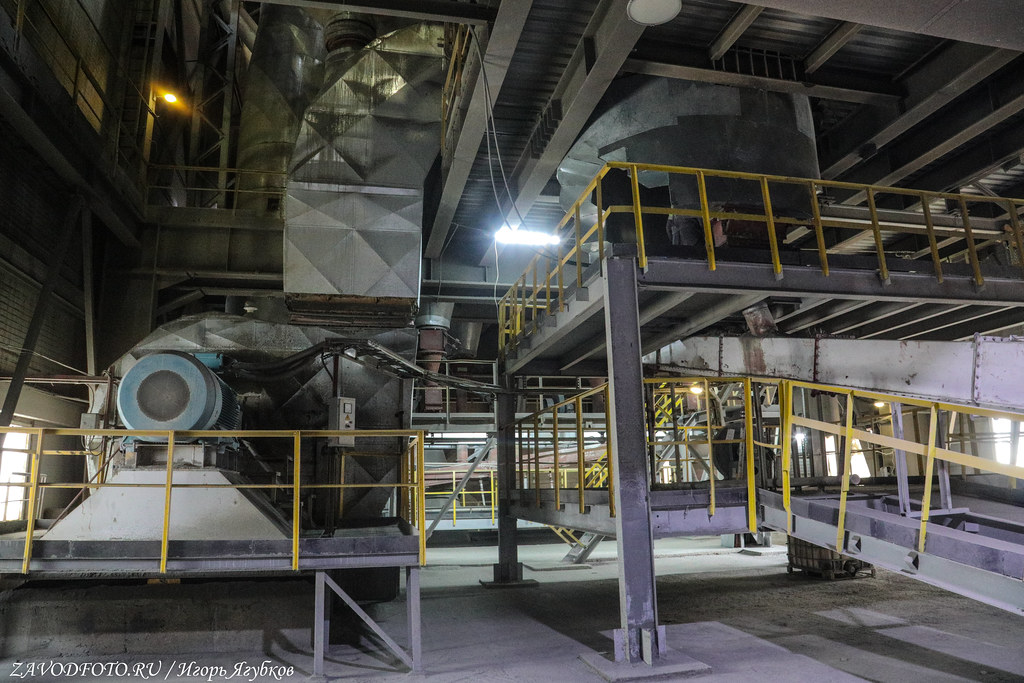
Дробилка для гипса.
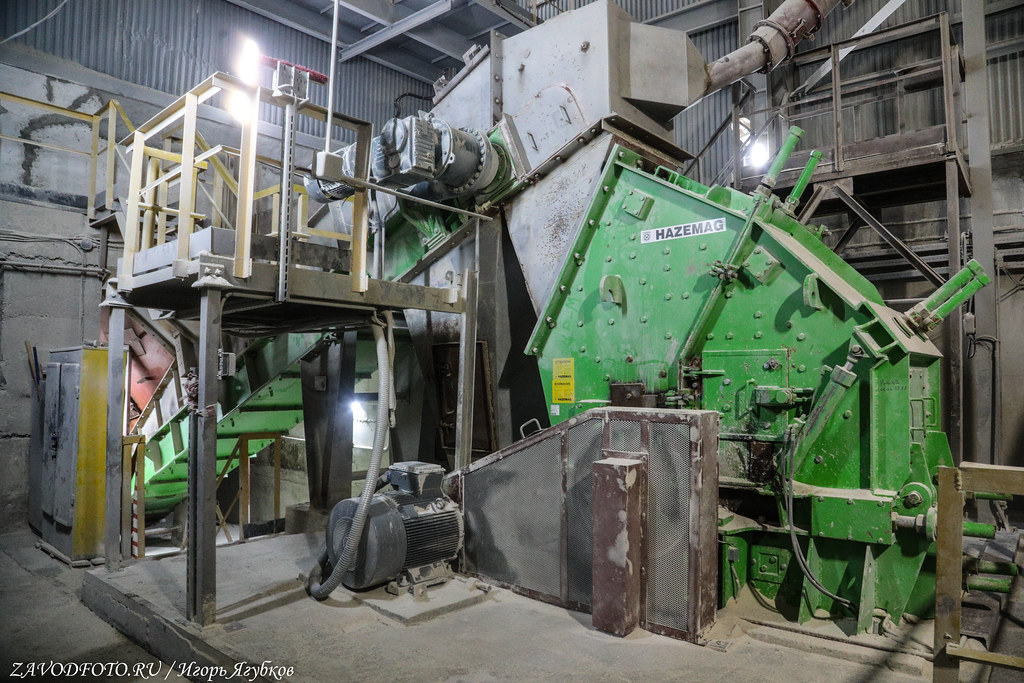
В настоящее время на заводе работают около 1300 человек.
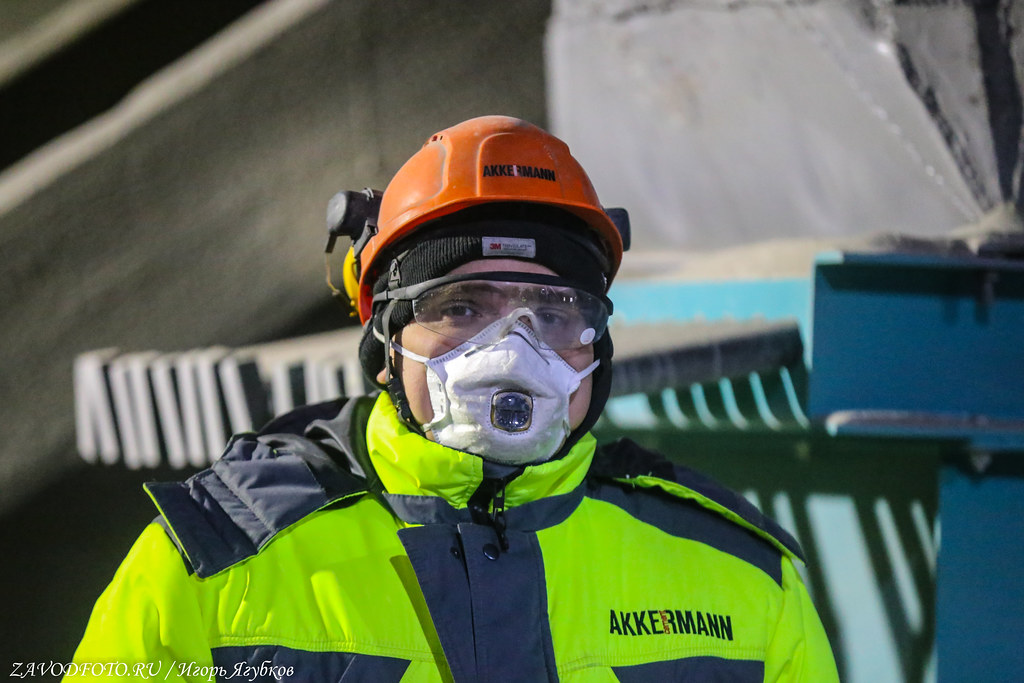
Дозаторы известняка
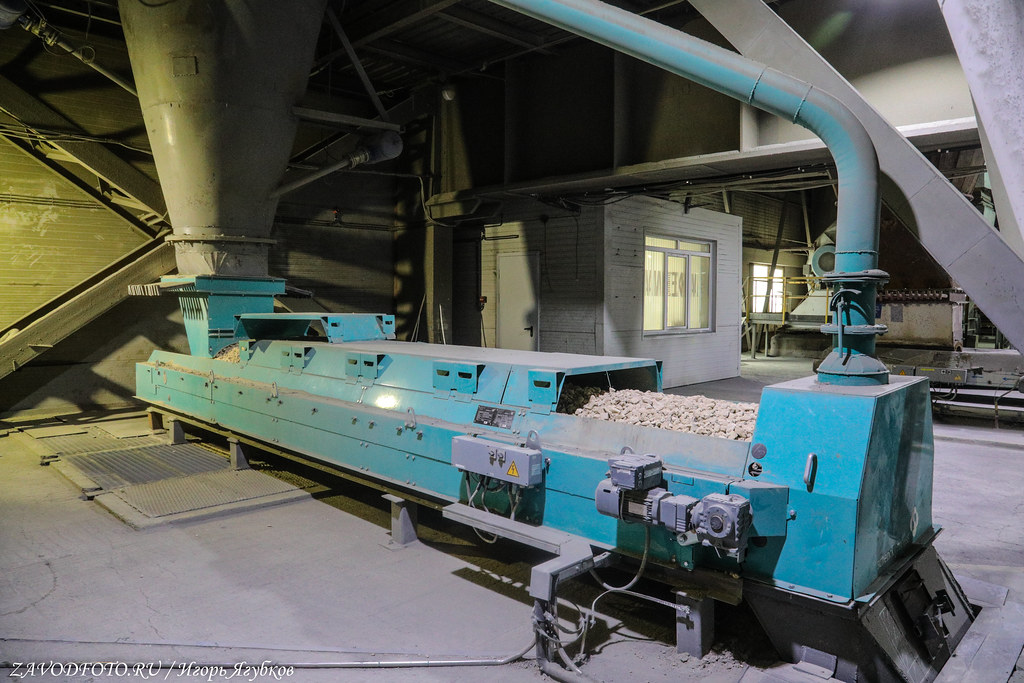
Теперь переходим непосредственно к производству цемента. Тонкоизмельченную смесь цементного клинкера смешивают с небольшим количеством других материалов, измельчают и получается цемент нужной марки. Все это происходит в мельнице. Она делает 14 оборотов в минуту.
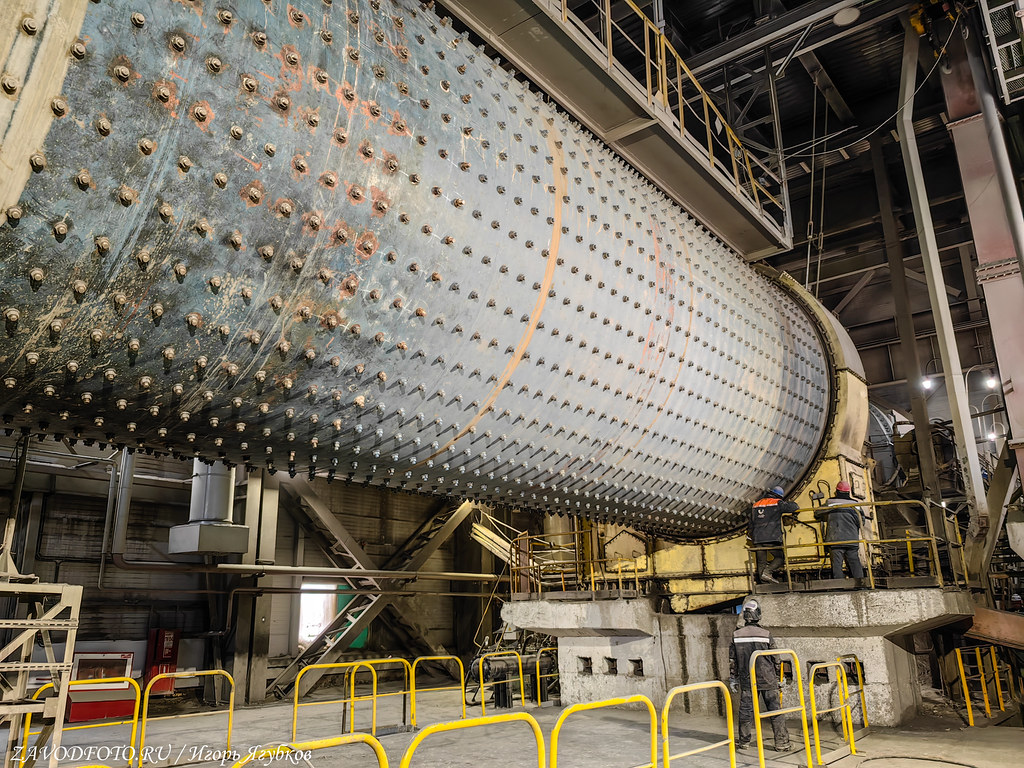
Правильно измельчать помогает вот такое умное ухо.
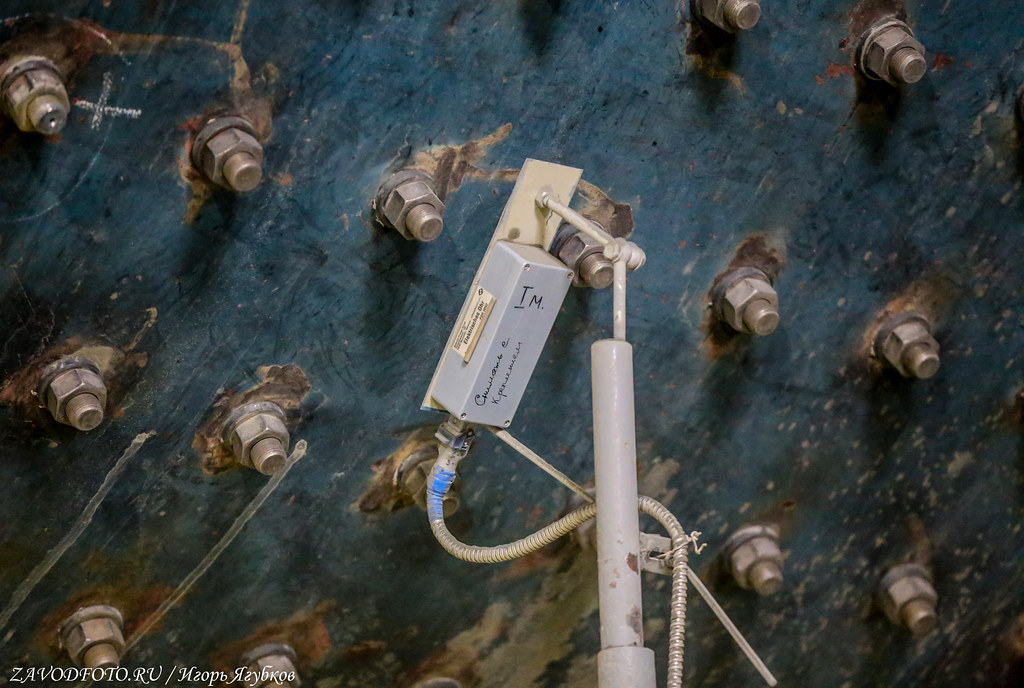
На этой установке получают нано-цемент. Он относится к цементам нового поколения по сравнению с портландцементом.
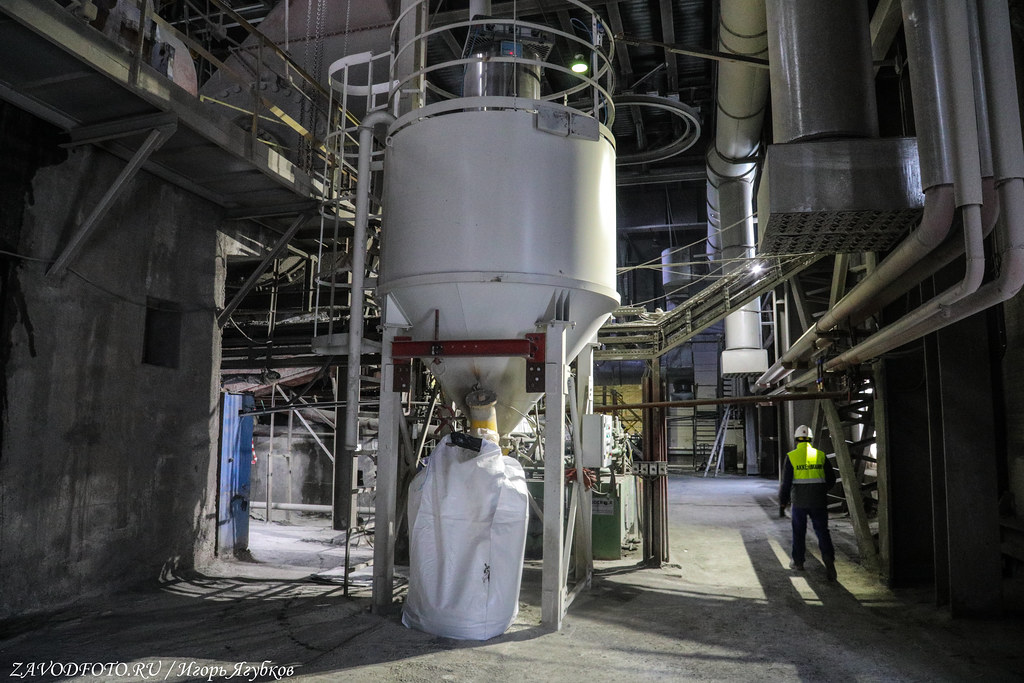
Далее цемент упаковывают в мешки по 50 кг и по 1 тонне. Его грузят в автотранспорт или вагоны. С территории завода уходит по 60-90 цементовозов в день. Так и начинается путешествие цемента под брендом AKKERMANN по России и не только.
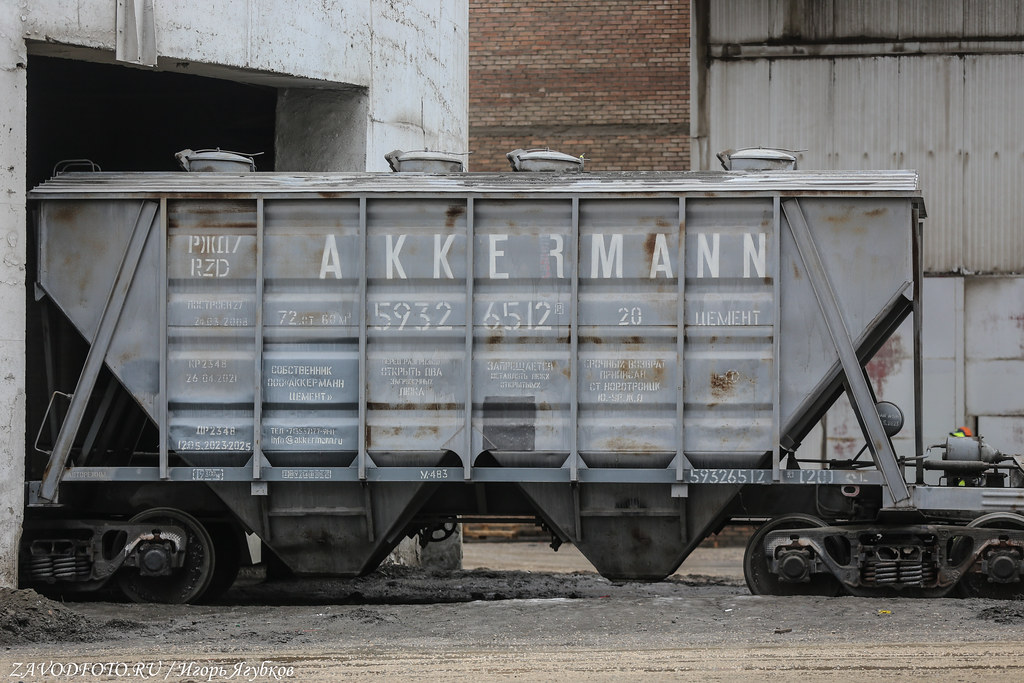
Большое спасибо компании ООО «АККЕРМАНН ЦЕМЕНТ» за открытость и тёплый приём! И в этот раз хочется снова упомянуть особую экономическую зону (ОЭЗ) «Оренбуржье», они такие молодцы, что готовы не только про себя рассказывать, но и со мной делиться полезными контактами, ведь благодаря им я попал и на это предприятие. Я добро помню, поэтому мне несложно и их в ответ похвалить. ОЭЗ «Оренбуржье» входит в ТОП самых инвестиционно привлекательных экономических зон в своей категории в России! Всего за несколько лет они смогли привлечь уже 15 резидентов, и это, я так понимаю, только начало. Территориально данная ОЭЗ располагается на двух площадках: в Оренбурге (380 га) и в Орске (180 га).
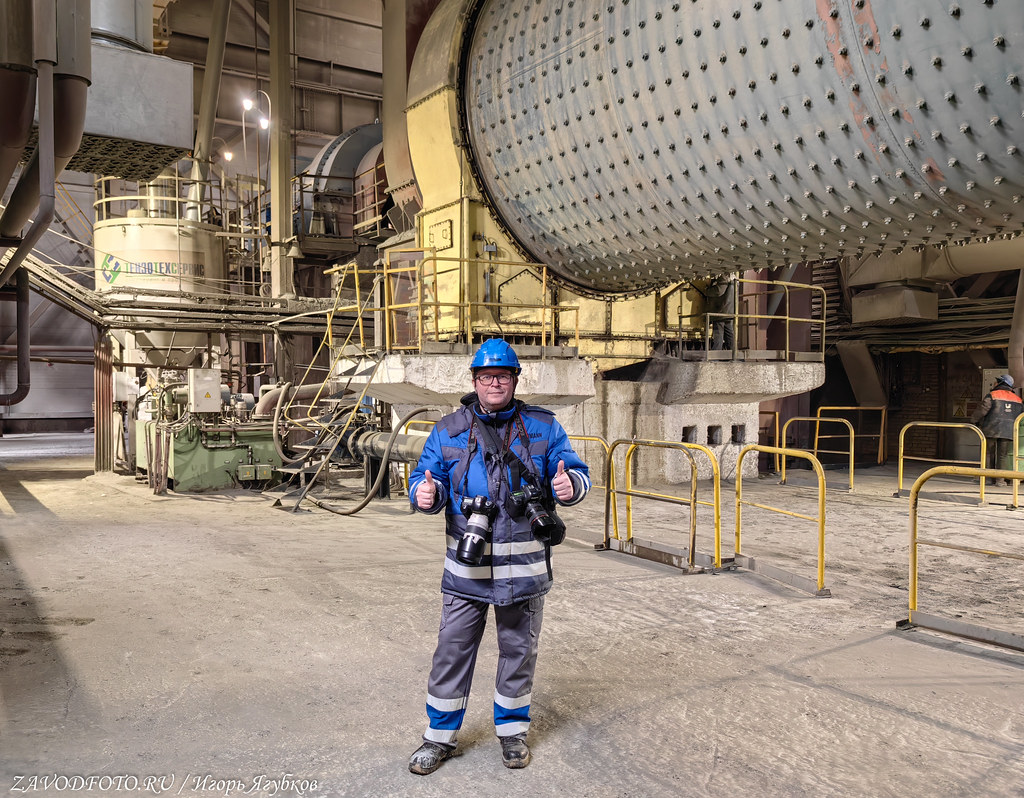
Ещё из моих поездок в Оренбургскую область:

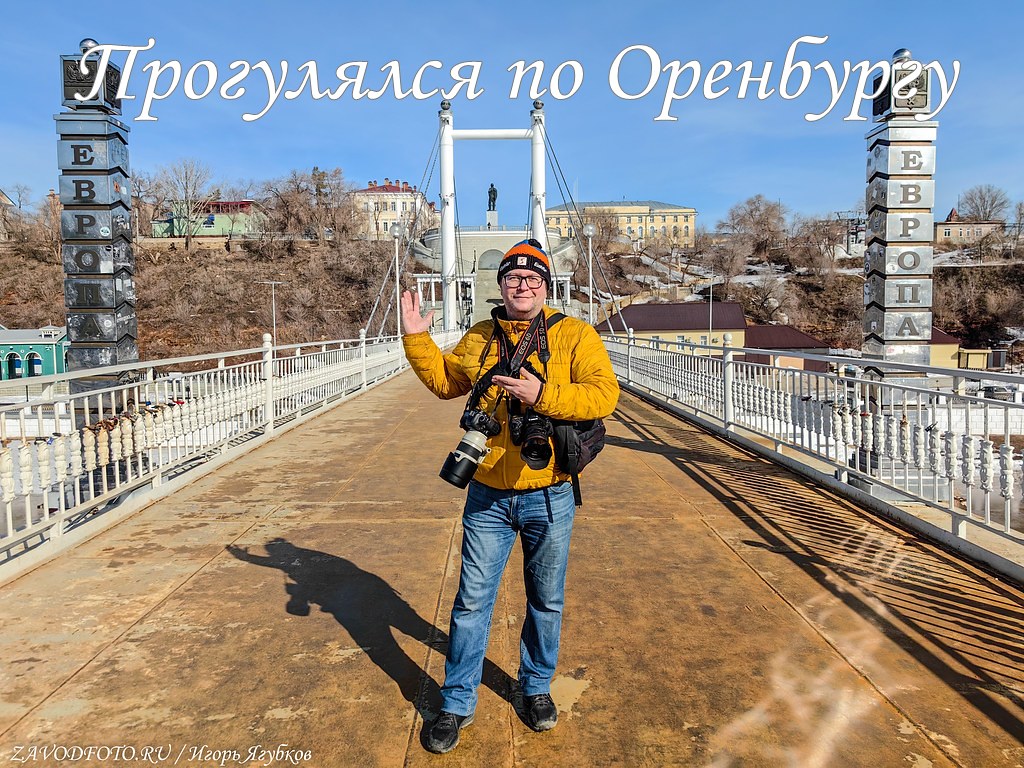
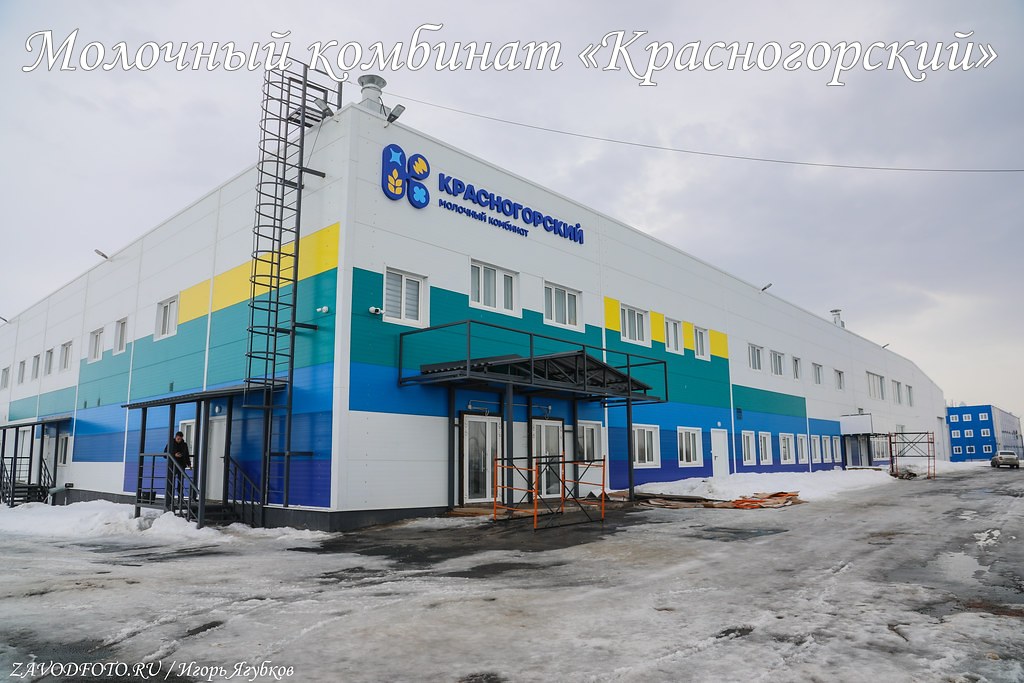

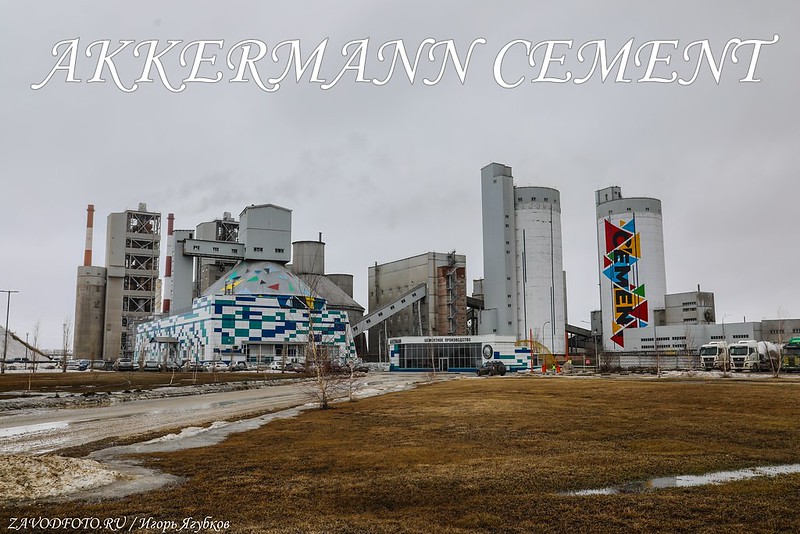
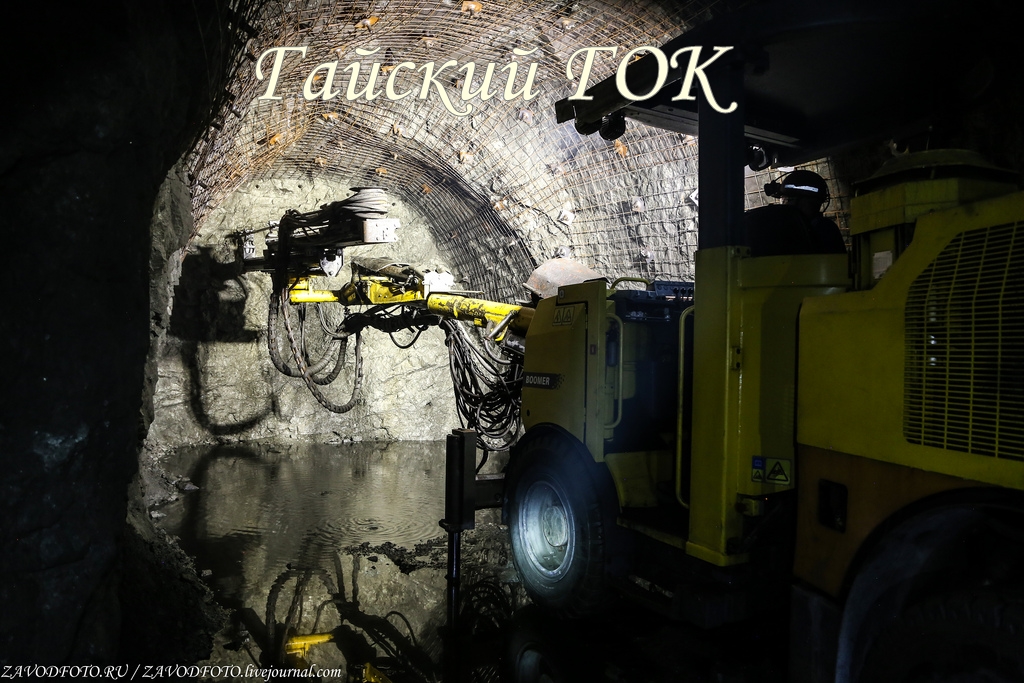
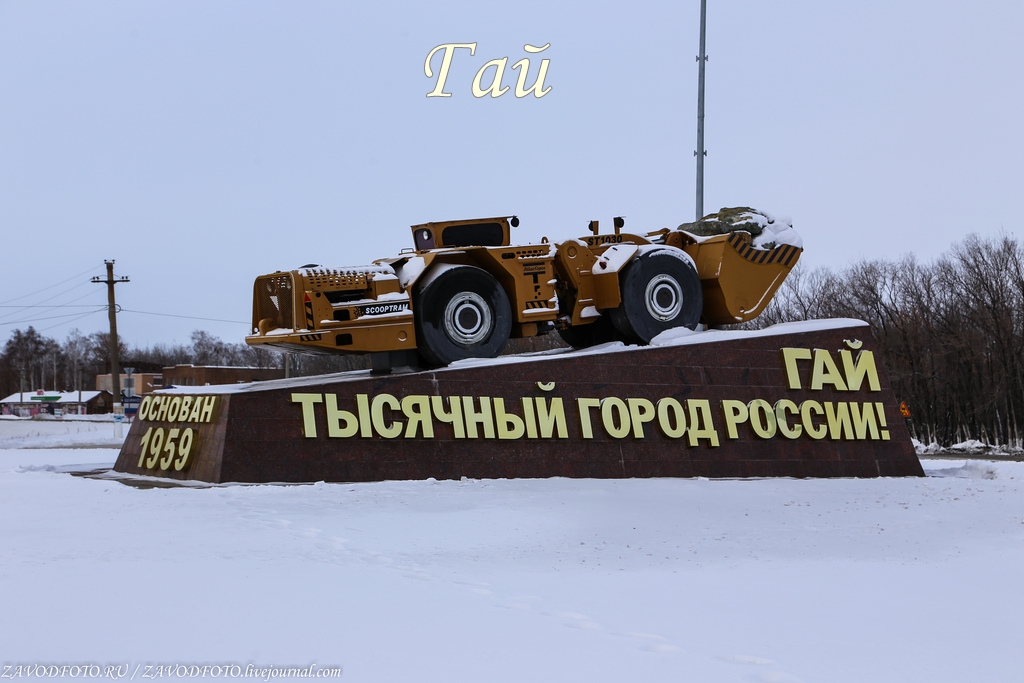
P. S. Уважаемые собственники и акционеры, представители пресс-служб компаний, отделы маркетинга и другие заинтересованные лица, если на Вашем предприятии есть, что показать - "Как это делается и почему именно так!", смело приглашайте в гости. Для этого пишите мне сюда: akciirosta@yandex.ru Берите пример с лидеров! На данный момент я уже лично посетил более 600 предприятий, а вот и ссылки на все мои промрепортажи:
Почему наша промышленность самая лучшая в мире: http://zavodfoto.livejournal.com/4701859.html
Я всегда рад новым друзьям, добавляйтесь и читайте меня в:
Дзен / LiveJournal / ВК / Одноклассники
Есть возможность внести свою лепту в развитие блога, будем рады донату (реквизиты карты): 5536 9177 1972 2396

На фоне капризной погоды здесь сразу видны яркие пятна, которые и настраивают на позитив.
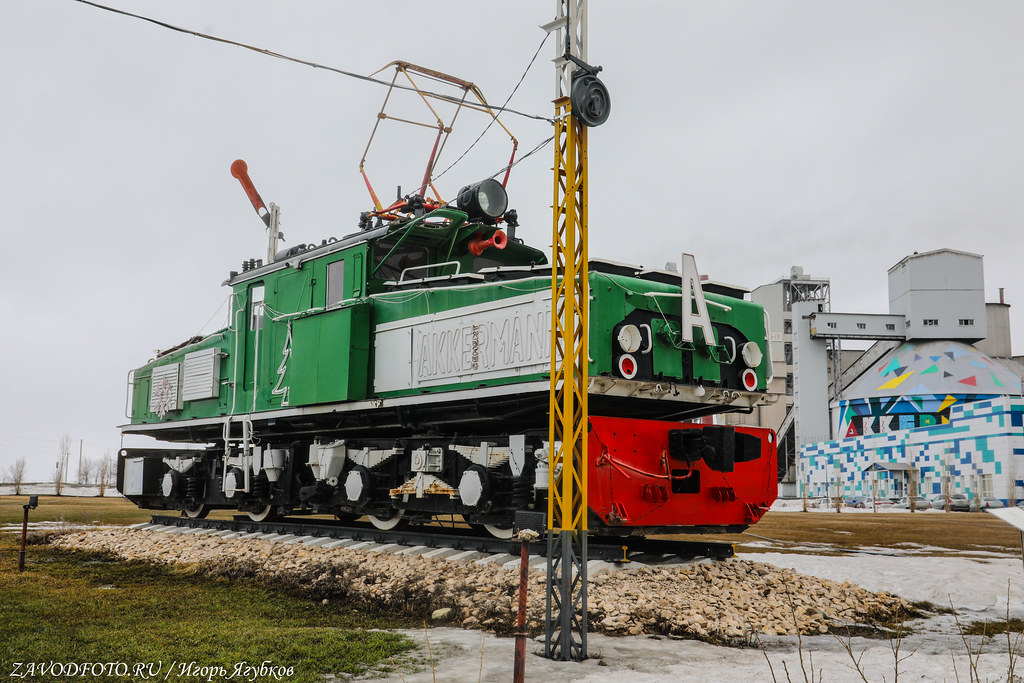
Привет-привет. Как оказалось, наш сегодняшний герой - это один из флагманов отрасли, да еще мы же почти земляки. Дело в том, что в семью AKKERMANN CEMENT входит и Горнозаводскцемент, тот самый, что из Пермского края.
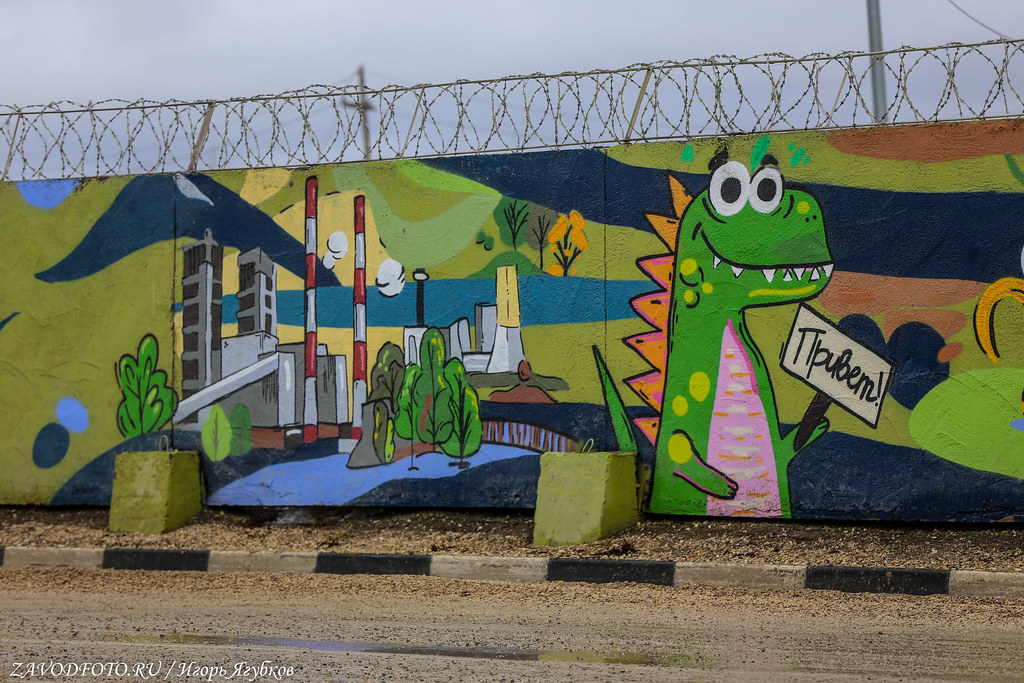
Название завода происходит от близлежащего поселка Аккермановка, на территории которого и располагается завод. По одной из версий благодарные потомки назвали поселок Аккермановка вблизи г. Новотроицка в честь немецкого горного изыскателя Фридриха Аккерманна. Он по инициативе Екатерины II оказался со своей семьей в Оренбургской губернии и получил надел земли недалеко от казачьей станицы Хабарное. До этого времени он объездил уже пол-России, серьезно изучил ее сырьевые запасы и догадывался об оренбургских залежах. Скрупулезно, с немецкой педантичностью и старательностью Фридрих подошел к изучению и этих мест. Уже через несколько лет Аккерманн отыскивает в окрестностях станицы Хабарное месторождение никеля, а позднее и залежи железных руд. Считается, что его данные сильно помогли первооткрывателю и советскому геологу Иосифу Леонтьевичу Рудницкому в обнаружении местных рудных месторождений.
Это такой нарядный один из силосов для хранения клинкера. Его высота составляет 42 метра, длина окружности здания 220 метров, общая площадь 9 000 м2.
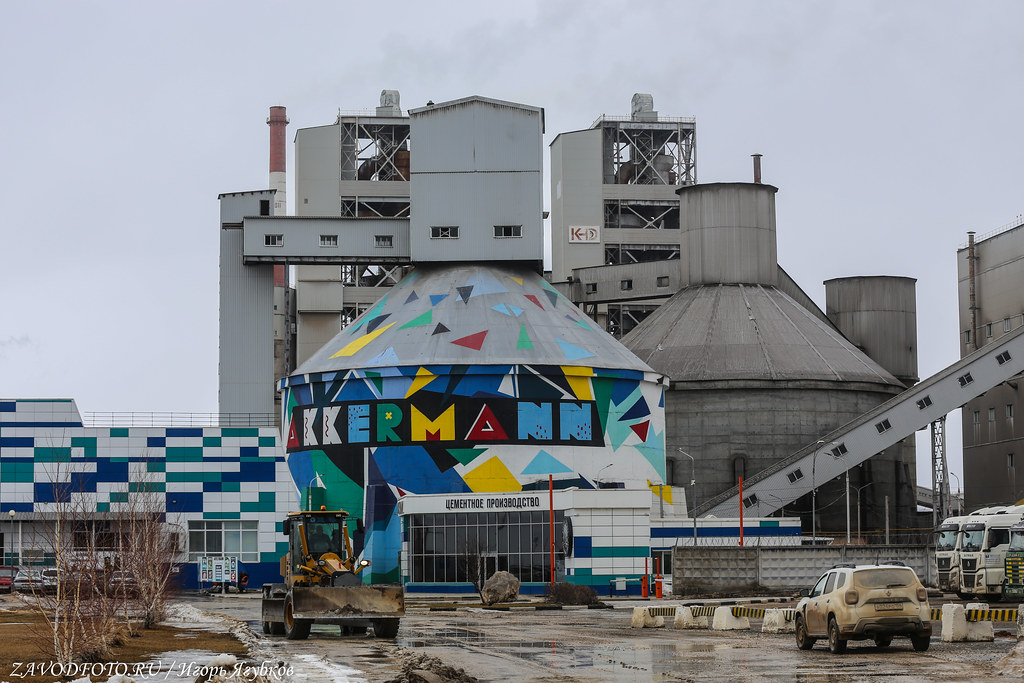
Завод в Новотроицке образован на базе цеха разработки шлаковых отвалов, ранее входившего в состав Орско-Халиловского металлургического комбината. 23 октября 2002 года создается ООО «Южно-уральская Горноперерабатывающая Компания». В 2005 году в её состав входят Аккермановский рудник и известково-обжиговый цех. Сам Аккермановский рудник начали разрабатывать в начале 50-х годов прошлого века. В 2006 году принимается решение о строительстве современного цементного производства. Ответственным за его проектировку был назначен Сибниипроектцемент. На оснащенность завода денег решили не жалеть, тогда выбирали из лучшего в мире. Выбор пал на оборудование немецкой компании KHD HUMBOLDT WEDAG (ZAB Zementanlagenbau GmbH Dessau) – мирового лидера в производстве цемента сухим способом. 15 ноября 2010 года происходит торжественное открытие первой очереди производства, мощность которой составляет 1 млн 300 тысяч тонн цемента в год. А в мае 2013 года здесь запускают вторую очередь с аналогичной мощностью. В 2020 году ООО «Южно-уральская Горноперерабатывающая Компания» получает новое имя ООО «АККЕРМАНН ЦЕМЕНТ».
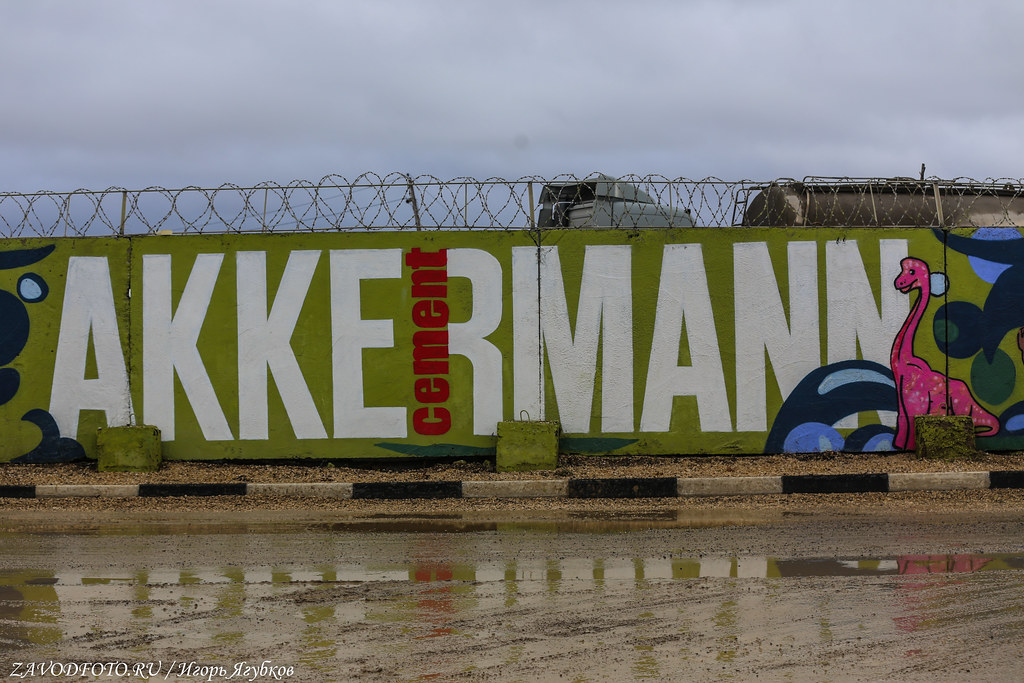
Сегодня Группа предприятий под брендом AKKERMANN (два цементных завода) входит в пятерку крупнейших отечественных производителей цементной продукции. Их цемент широко представлен в 22 регионах нашей страны и Казахстана.
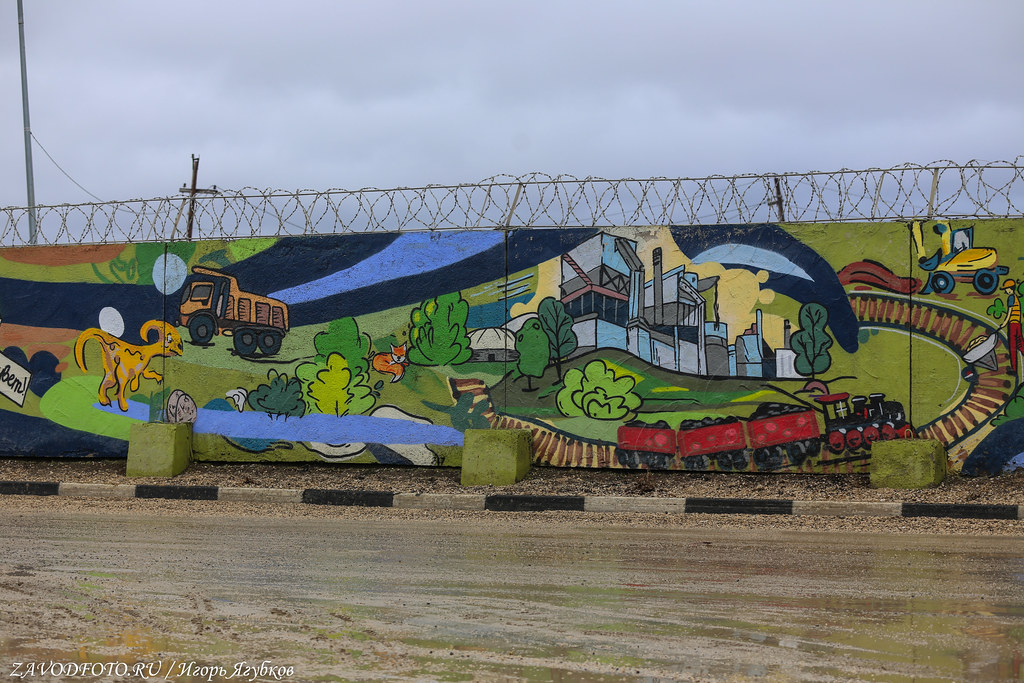
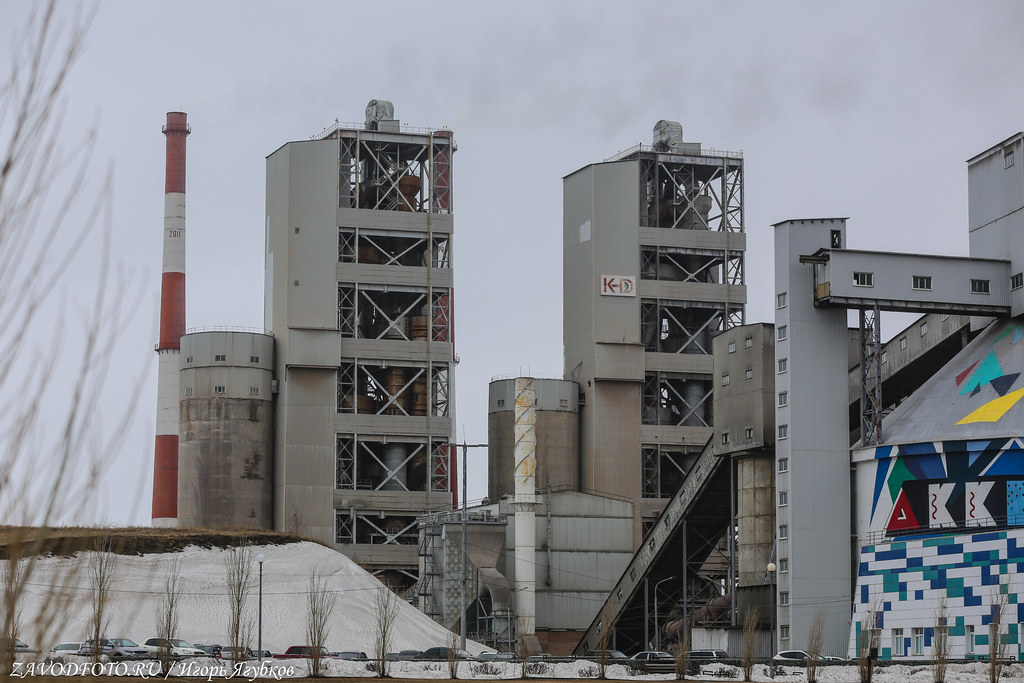
Цемент - это незаменимый материал, без которого нельзя представить ни один строительный объект. Уникальность материала неоспорима, ведь так или иначе он участвует практически во всех строительных этапах. Современные комбинаты используют три базовых метода изготовления цемента, которые зависят от метода подготовки сырьевого материала к обжигу: мокрая технология, сухая и полумокрая (комбинированная). Вроде бы время идет, а на производствах цемента достаточно сложно придумать что-то новое с точки зрения рецептуры или технологий. Каждая компания старается брать большими коммуникациями, цифровизируют продажи, сервисом, скоростью доставки. Даже тот факт, что компании из отрасли стали открываться, это же огромный плюс, и большее доверие к продукции. Кстати, любой из вас может попасть и сюда, завод АККЕРМАНН ЦЕМЕНТ с модным нынче промтуризмом дружит.
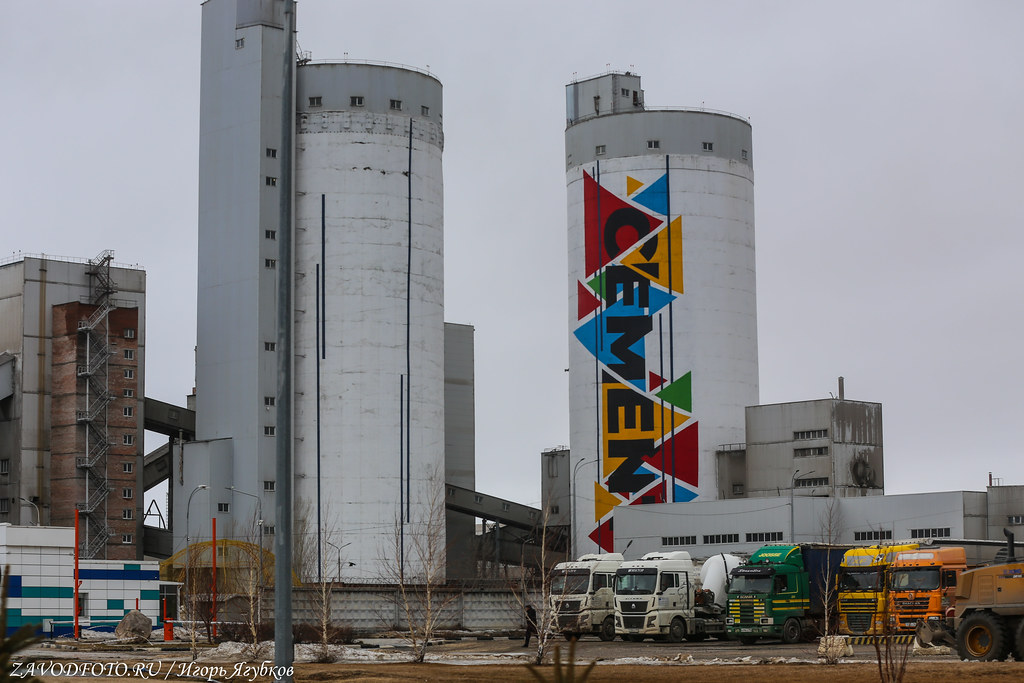
Предприятие полностью автоматизировано. Все производственные участки, от приемки сырья до отгрузки готовой продукции, оборудованы датчиками, сигналы от которых аккумулируются и выводятся на мониторы в центральном пульте управления.
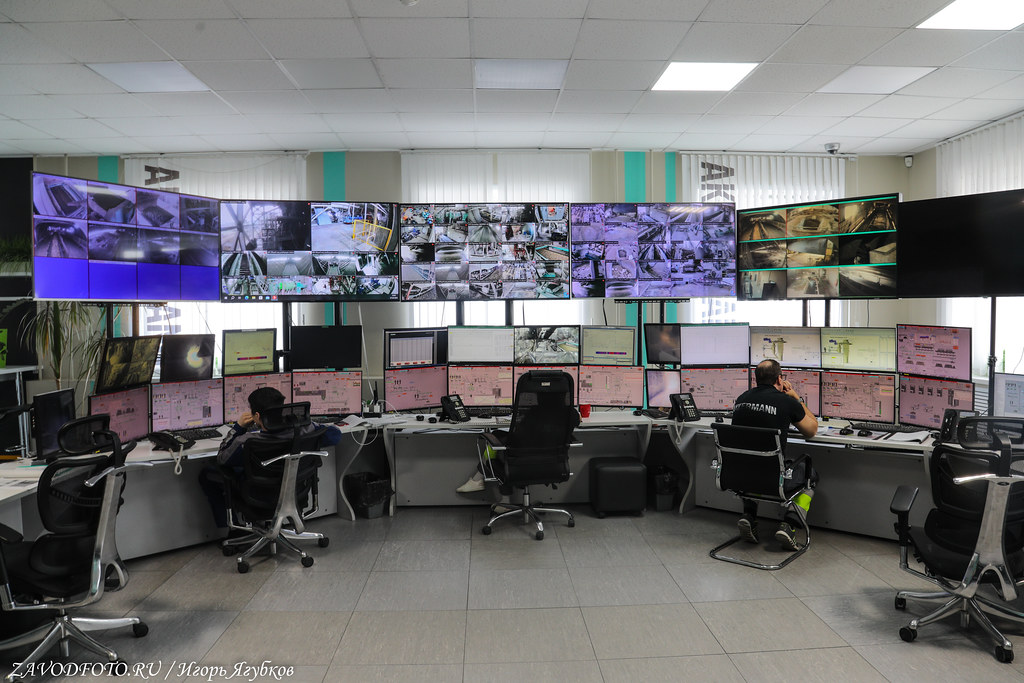
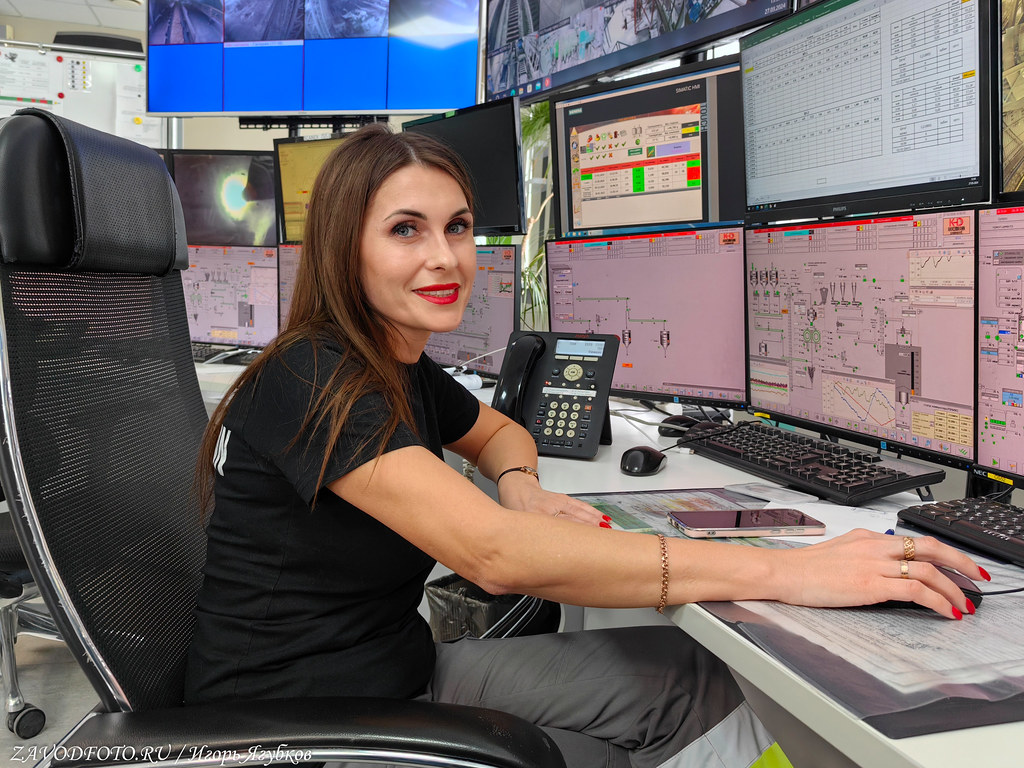
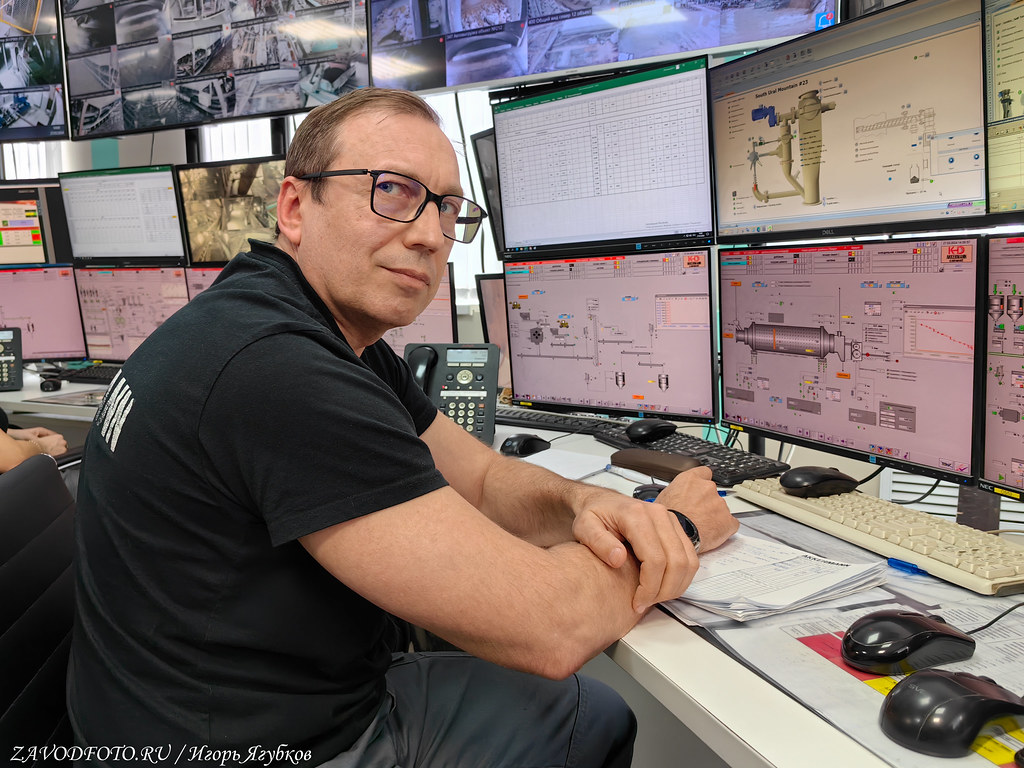
Прямо на ЦПУ можно подвигаться здоровья ради
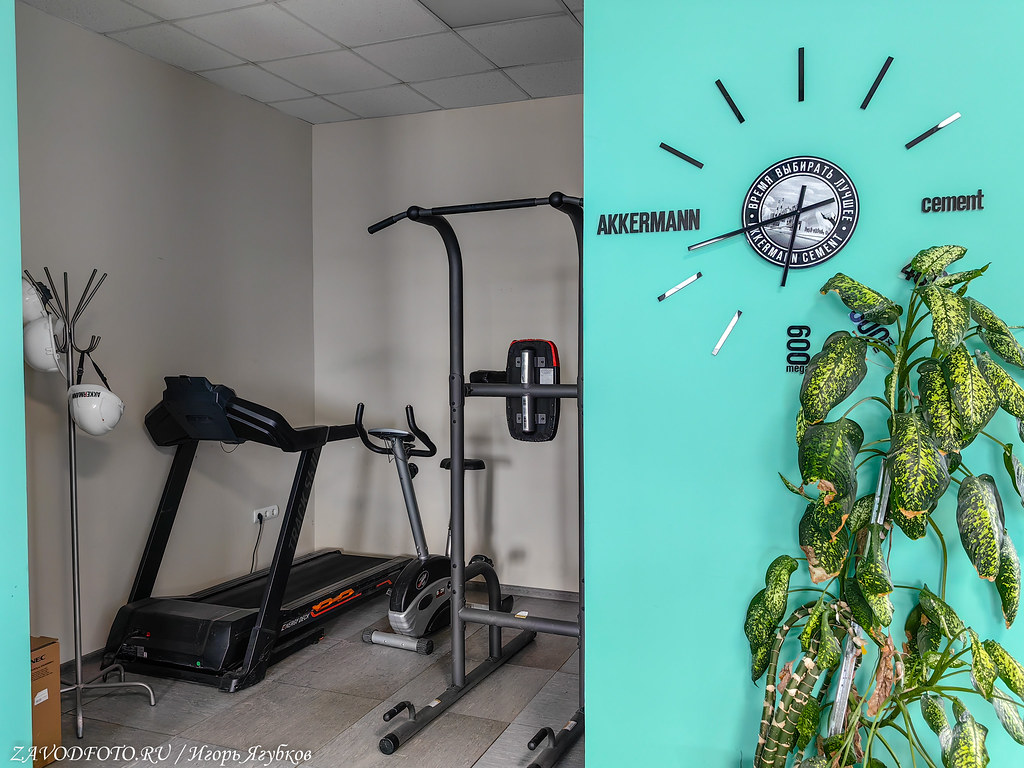
или перекусить...
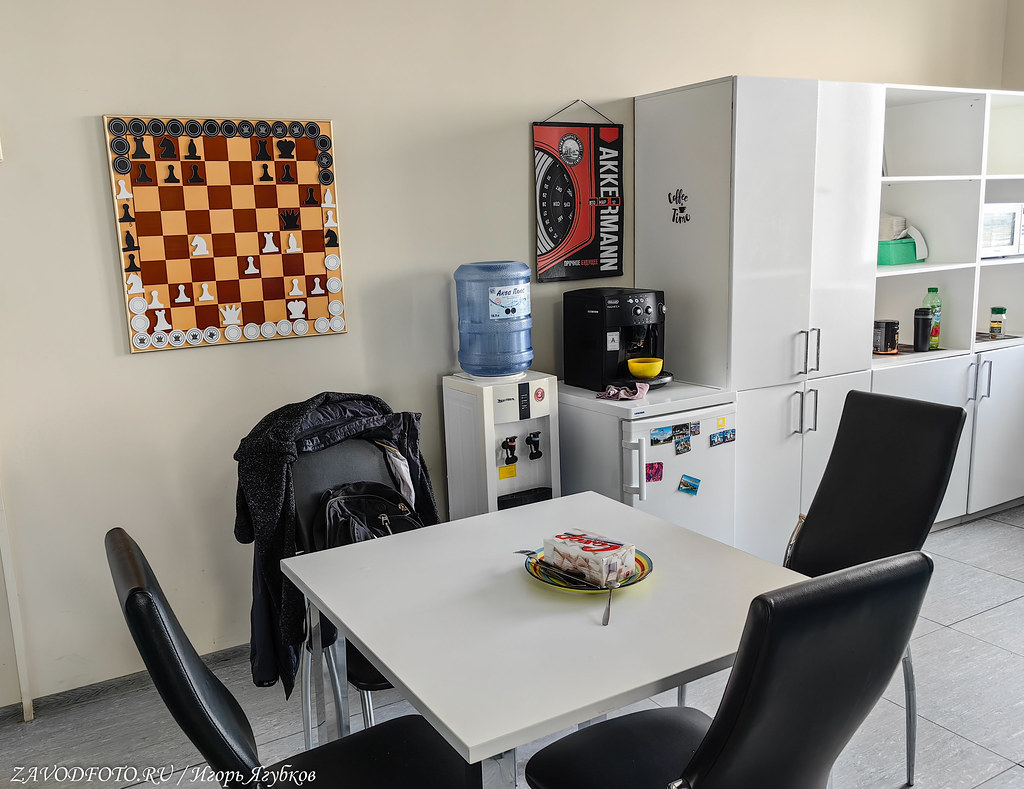
Мощности новотроицкого предприятия позволяют выдавать до 2,3 млн тонн продукции в год. Свой цемент они делают сухим способом. Данная технология более новая. Ведь сухой способ производства (есть еще и мокрый) более экономичен и экологичен, ведь при нем потребляется меньше пресной воды и топлива, а значит экономятся природные ресурсы и снижается уровень выбросов в окружающую среду.
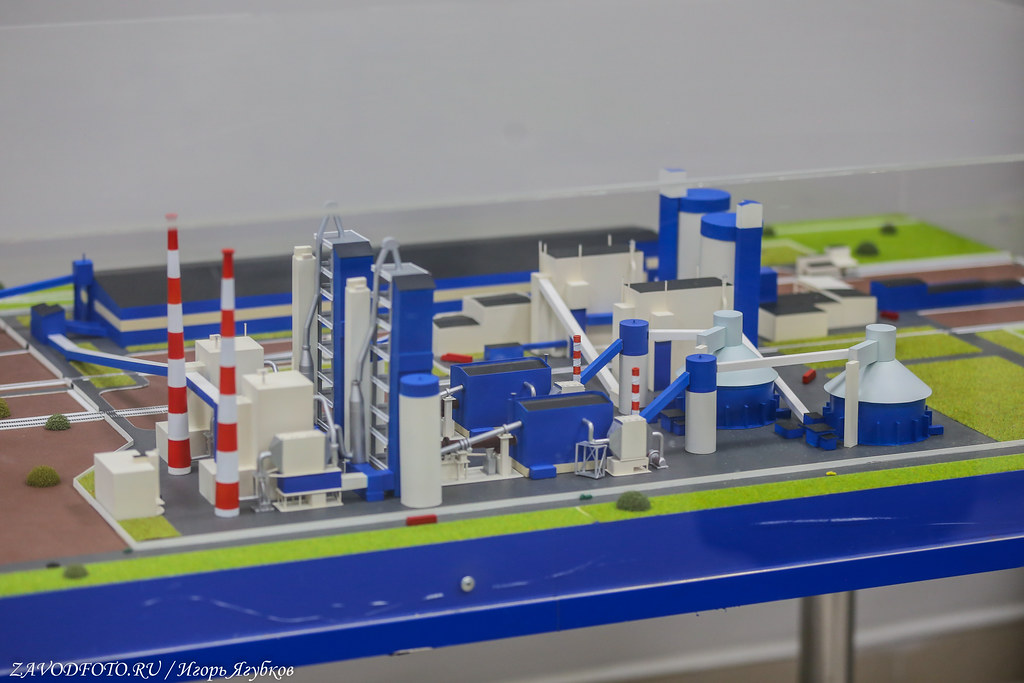
Производство цемента включает четыре основные стадии. Первая стадия - это добыча и подготовка сырьевой смеси. Далее её доводят до ума. На третей стадии сырье обжигают. А на четвертой происходит помол клинкера и добавок. Собственно наш цемент и готов. Стоит отметить, что здесь продукцию делают в том числе по особой технологии. Вместо известняка и глины в цемент добавляют металлургический шлак от «Уральской стали» - таким образом, плюсом перерабатываются отходы производства и не расходуются природные запасы. Завод утилизирует металлургические шлаки в объеме миллиона тонн в год. Запаса этого шлака хватит как минимум на 100 лет. Между прочим, добываемый на Аккермановском месторождением известняк являются первосортным сырьем и считаются лучшими на Урале. Именно он и становится основой цемента, который изготавливается на заводе «АККЕРМАНН ЦЕМЕНТ».
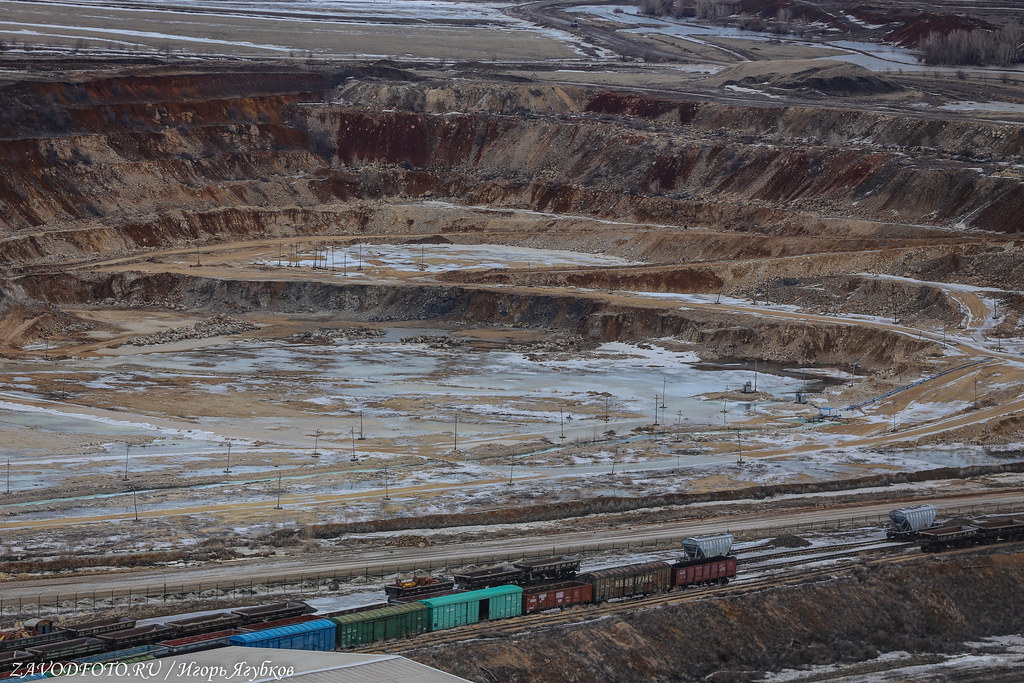
Итак, сырьем для производства цемента выступают известняк, глина и металлургические шлаки (отходы металлургического производства, доменного и электроплавильного). Известняк, добытый в карьере, дробится и подается на склад известняка. К нему далее добавляется около 12 % глины. Таким образом, получается смесь, которую называют микс. Её далее отправляют на другой объединенный склад. Объединенный склад у них разделен на две части, одна часть для микса, а другая часть для шлаков. На каждой из частей формируются по два штабеля. Пока один формируется, другой отправляется в производство. Далее всё сырье подается в отделение помола и сушки, чтобы эту смесь превратить в муку.
Один из складов сырья.
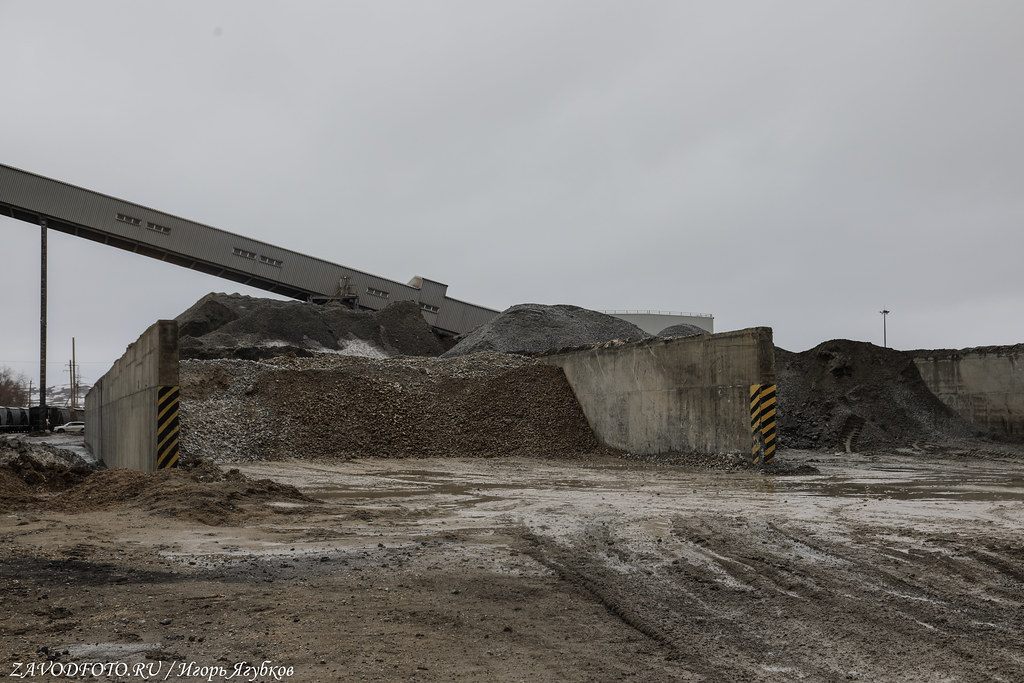
Для производства сырьевой муки используется роллер-пресс. Примерная дозировка микса шлака доменного и шлака ЭСПЦ (электросталеплавильного) составляет 70 %, плюс 25 % чисто доменного и 5 % шлака ЭСПЦ. Всего на предприятии две совершенно одинаковые производственные линии. Вот как раз мы сейчас находимся в отделении помола и сушки сырья, где работает роллер-пресс первой линии.
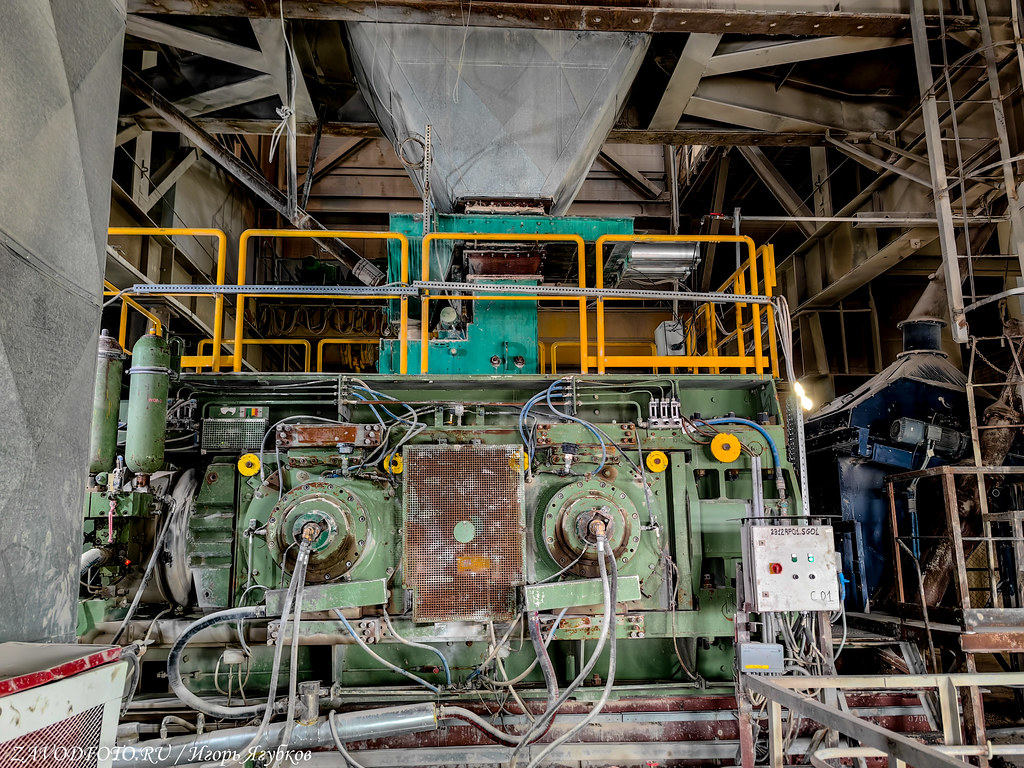
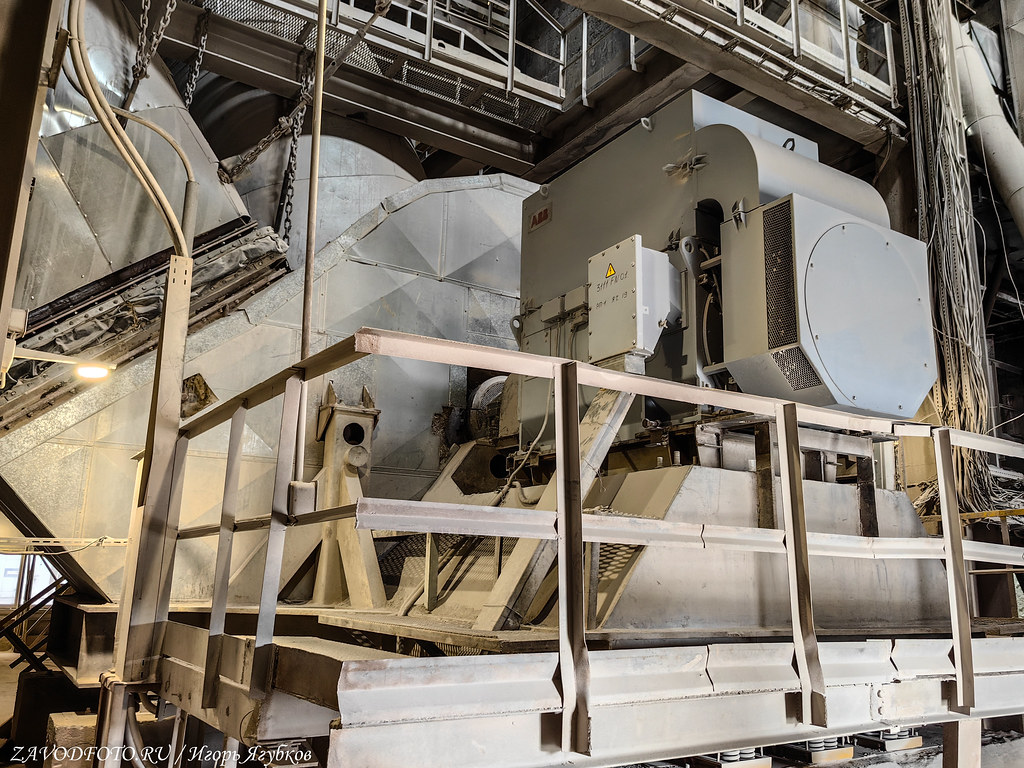
Это самый большой бункер для подачи известняка и глины. Порядка 70 % подается этого компонента. Бункер микса вмещает 600 тонн.
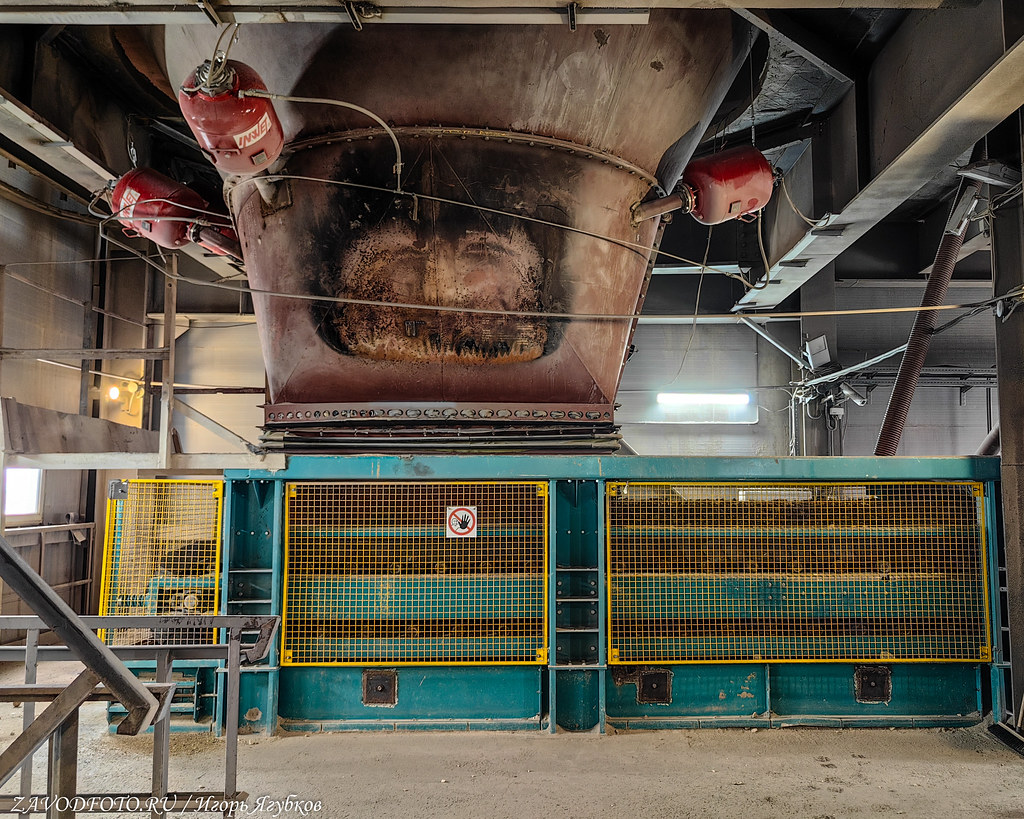
По соседству ещё два бункера поменьше со шлаками металлургического производства. Эти бункера вмещают в себя по 150 тонн.
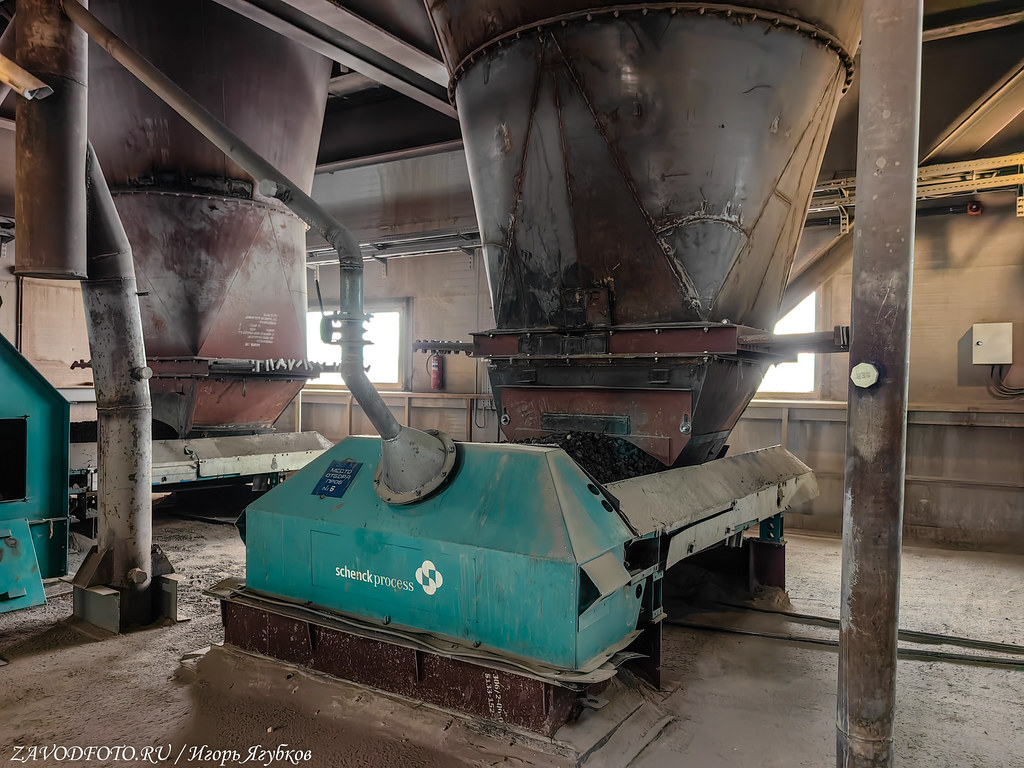
Вся эта солянка по конвейеру подается и в итоге смешивается. Специальный металлосепаратор отслеживает, чтоб ненужные частицы не попали в работу.
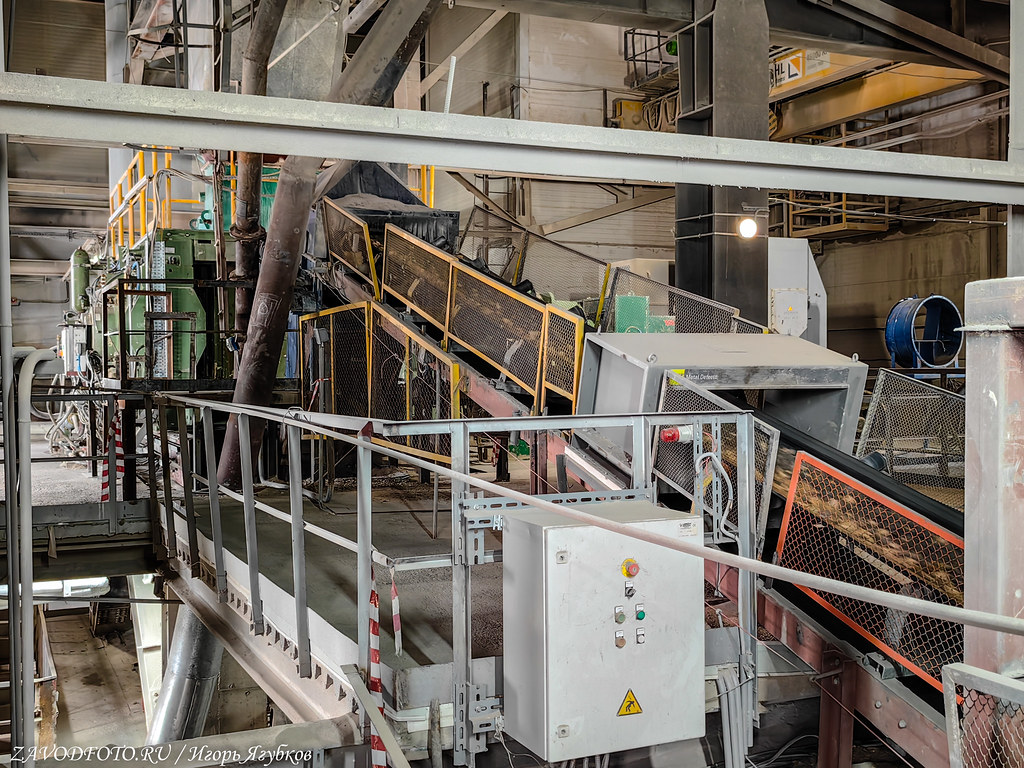
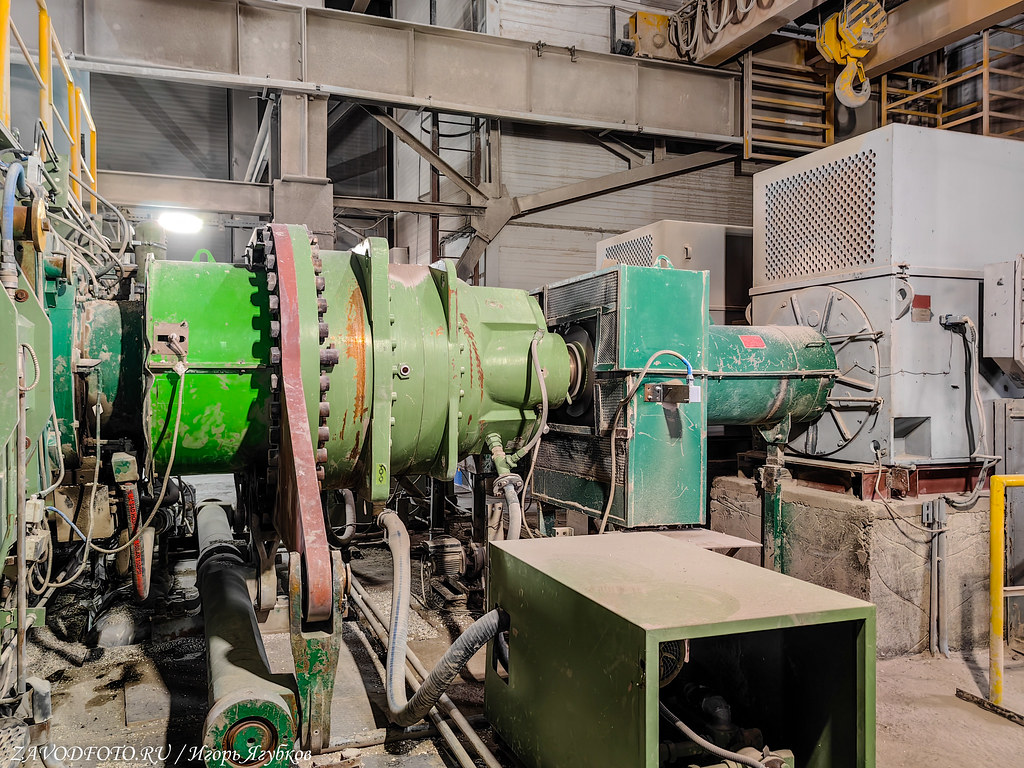
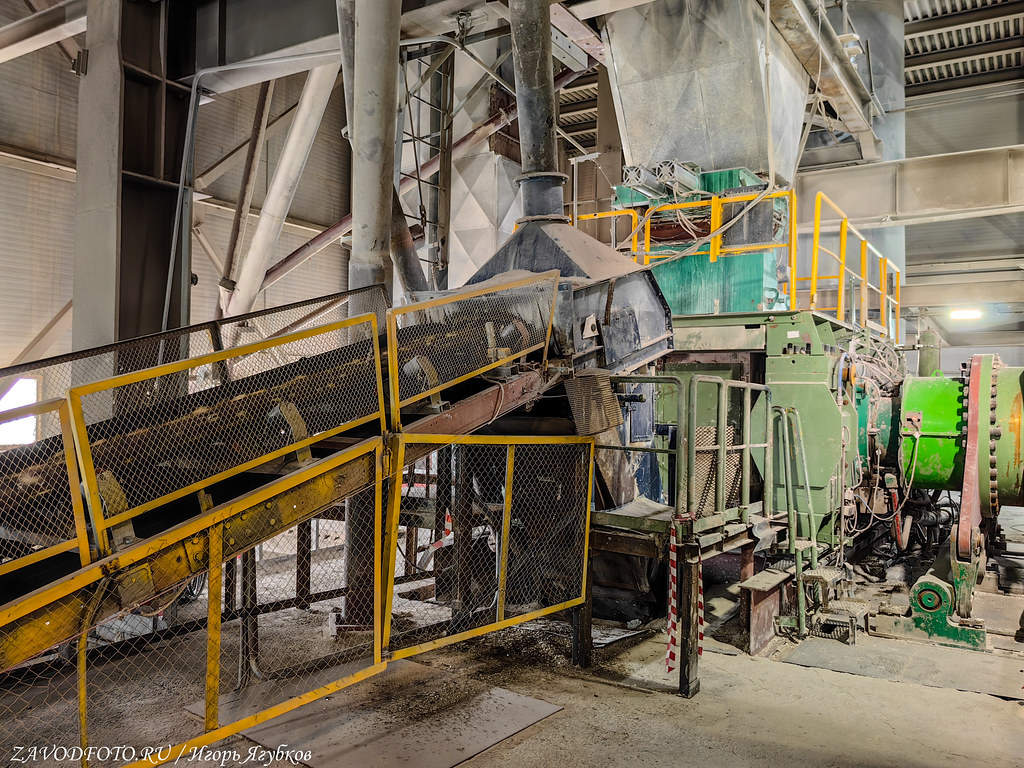
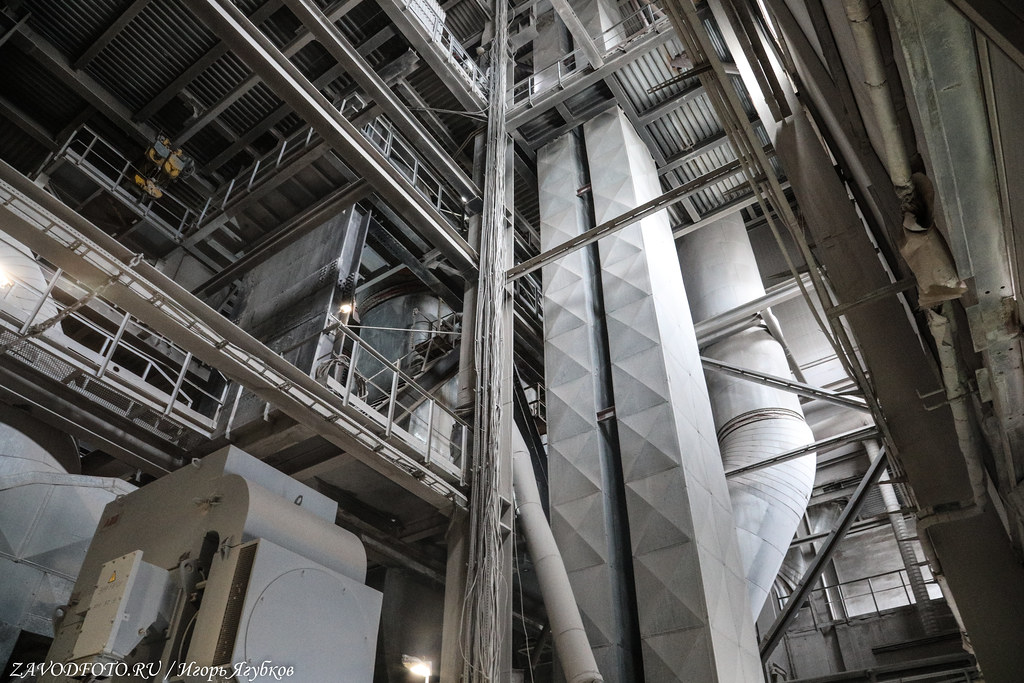
На этом участке идет оперативный отбор проб муки, и по пневмопочте заборы отправляются сразу в лабораторию.
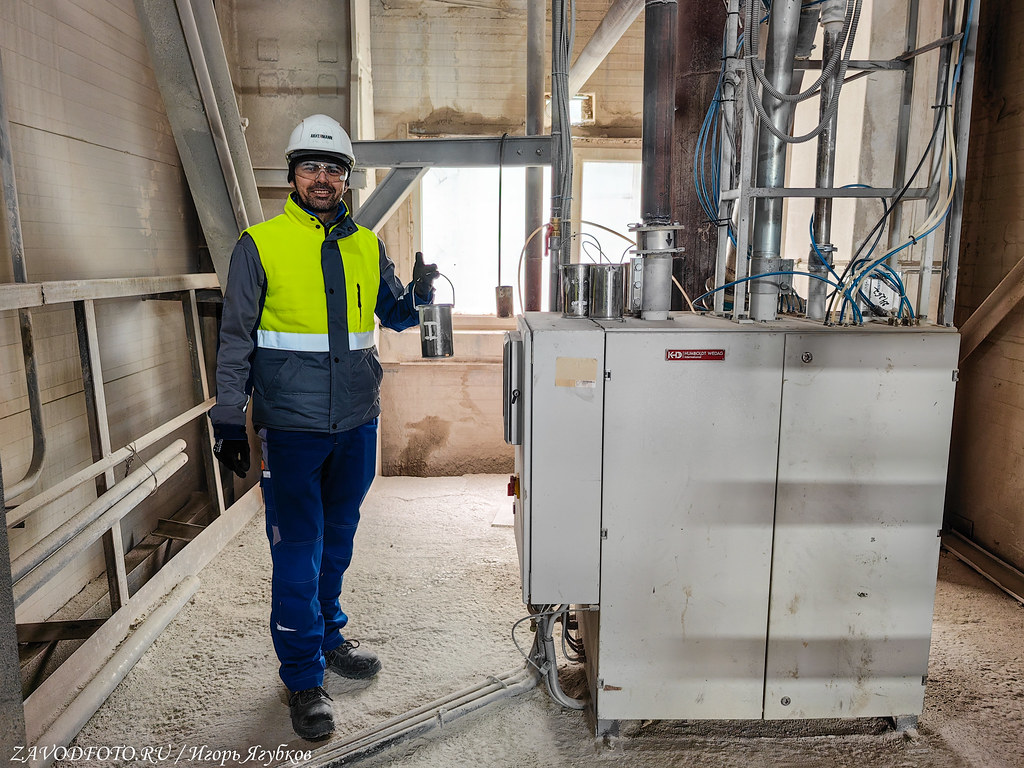
На следующей стадии эстафету подхватывают вращающие печи длиной 62 м. В них происходит процесс обжига клинкера. Обжиг смеси и получение клинкера - это самая важная стадия. Всё дело в том, что эксплуатационные свойства цемента напрямую зависят от качества клинкера, температуры и времени обжигания. Так как в естественных условиях основные компоненты сырьевой смеси не вступают в химическую реакцию друг с другом, поэтому процесс взаимодействия между глиной, известняком и другими компонентами запускается при нагревании.
Температура в печах может достигать до 1400°C. Сырье на максимальной производительности в печи находится порядка 20-25 минут.
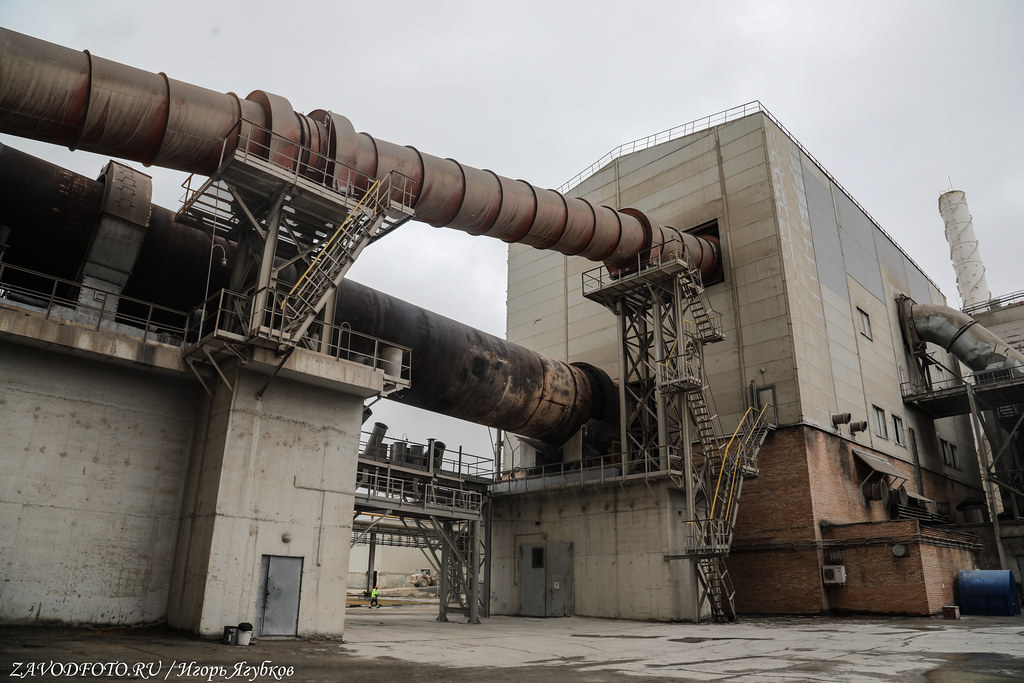
По мере прохождения сырья через печь происходят различные сложные химические реакции. Декарбонизация: известняк (карбонат кальция) разлагается на оксид кальция (негашеную известь) и углекислый газ. Дегидратация: вода удаляется из глинистых (алюмосиликатных) минералов, что приводит к образованию алюмината кальция и силикатных соединений. Реакция железной руды. Железная руда реагирует с оксидом кальция с образованием феррита кальция, важнейшего компонента цементного клинкера.
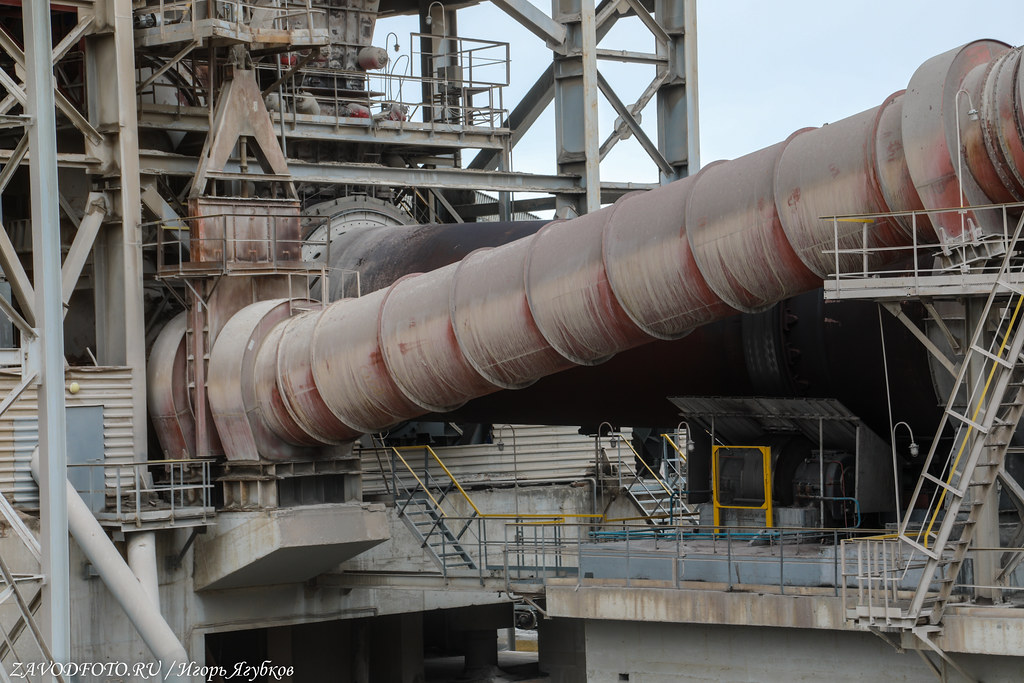
Кстати, печи сухого способа производства примерно в два раза короче печей мокрого способа при равной или даже большей производительности. Уменьшение длины печи связано с двумя основными факторами: во-первых, в печах сухого способа в принципе отсутствует зона сушки, во-вторых, часть процессов выносится из печи в запечные теплообменные устройства.
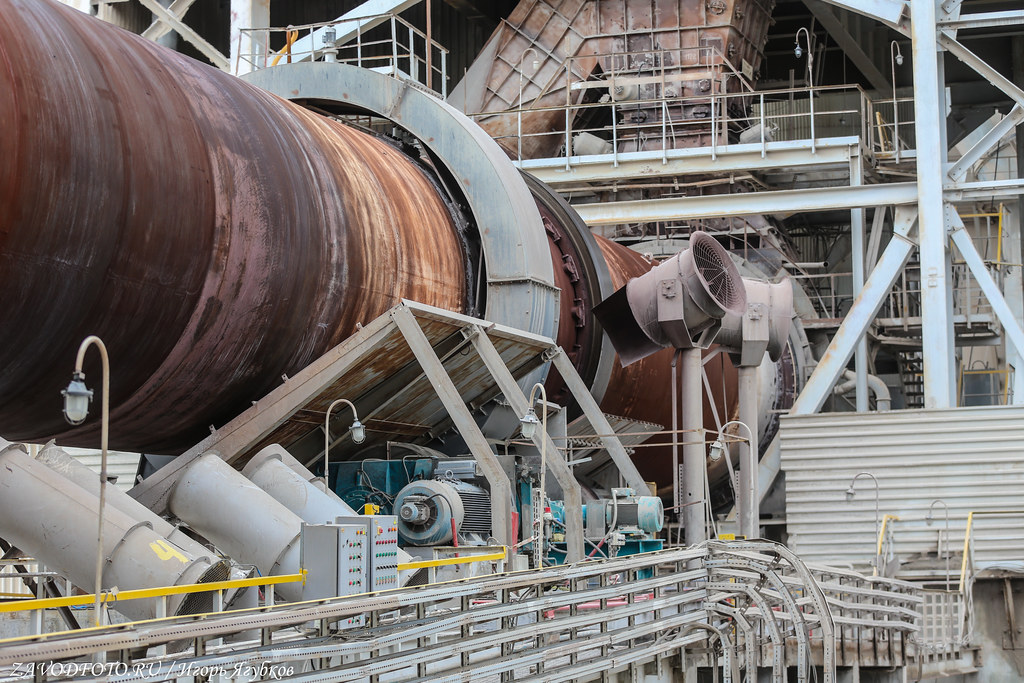
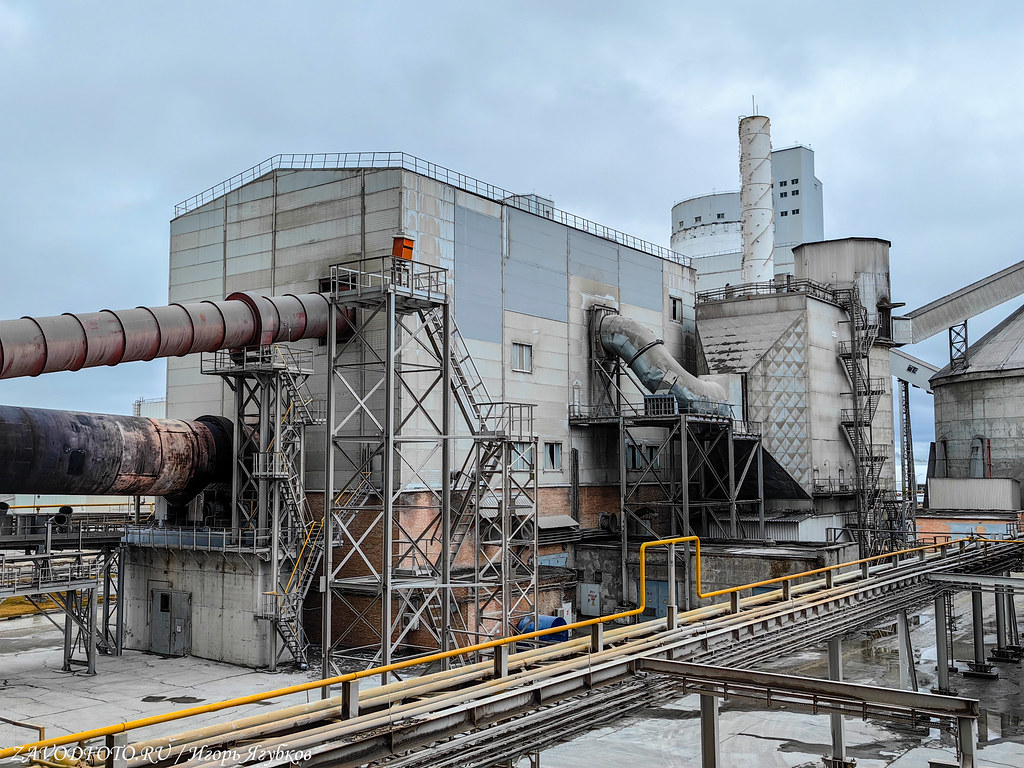
Чтобы с природой шутки не шутить, на заводе предусмотрены электрофильтры для очистки отходящих газов от пыли.
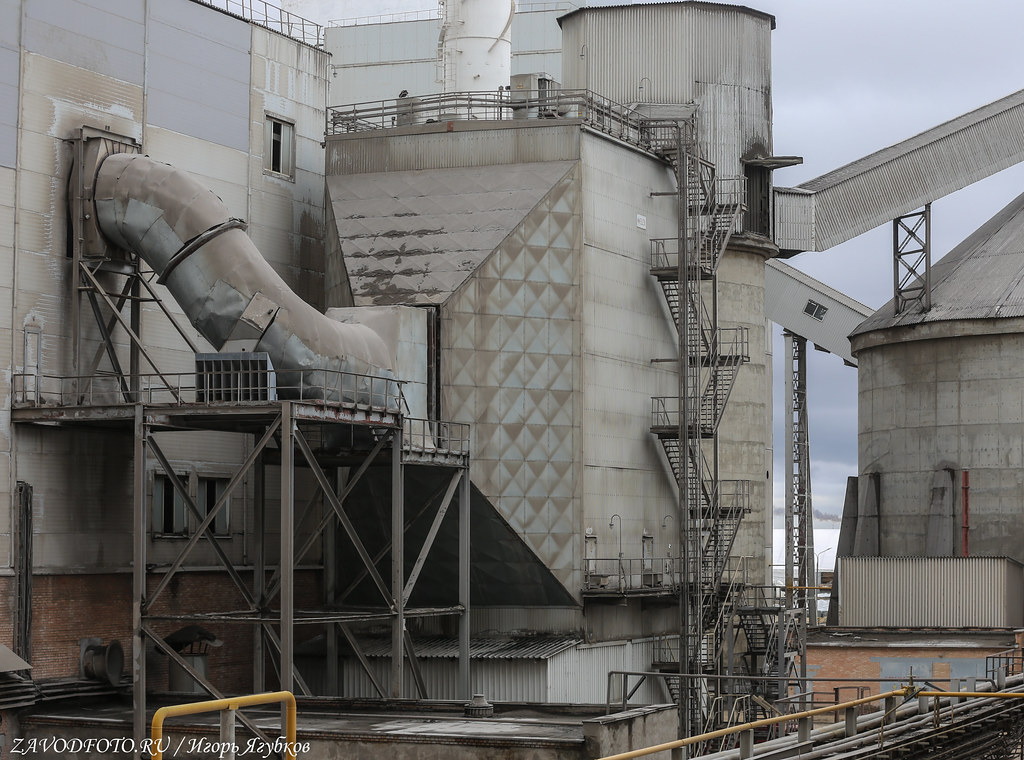
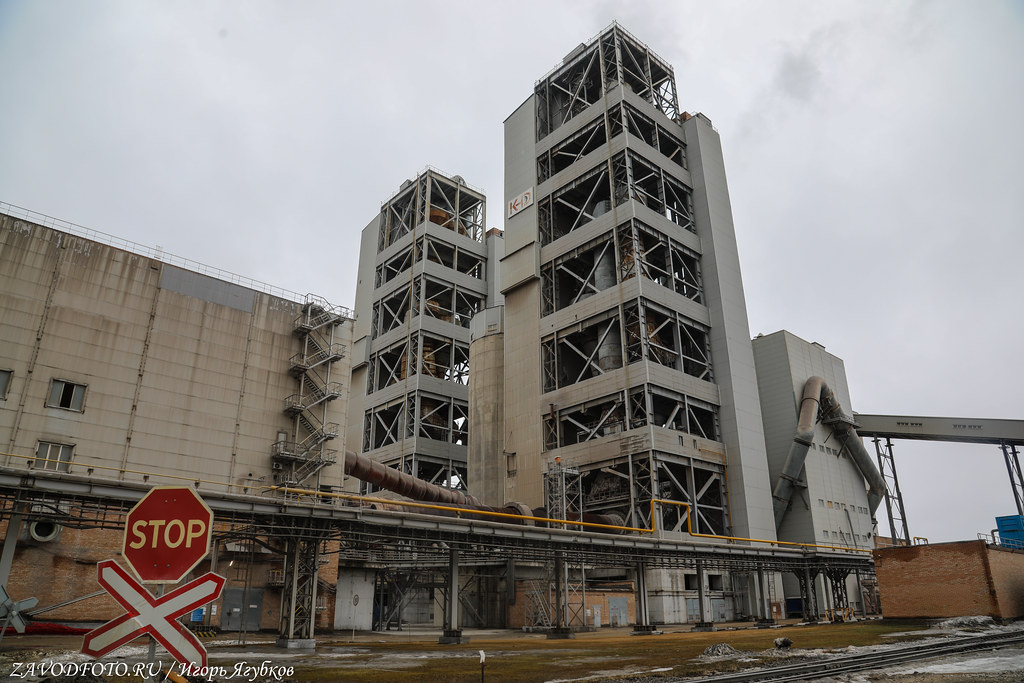
Что ещё для счастья надо? Правильно - залезть повыше. Мы на высоте где-то 140 метров.
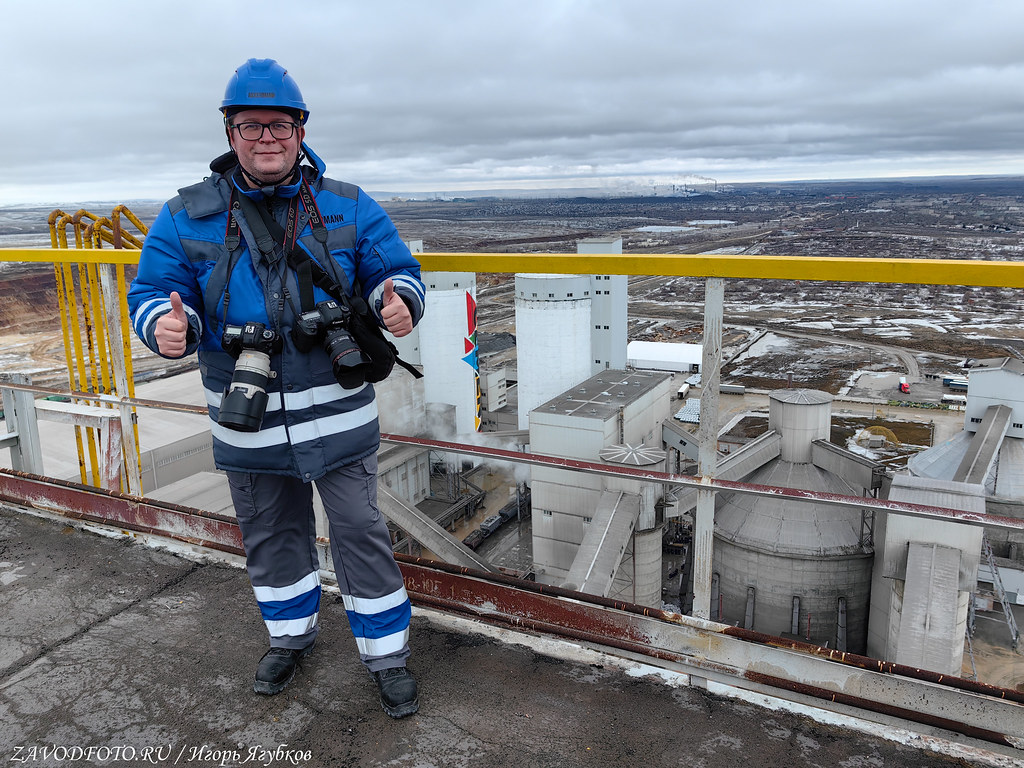
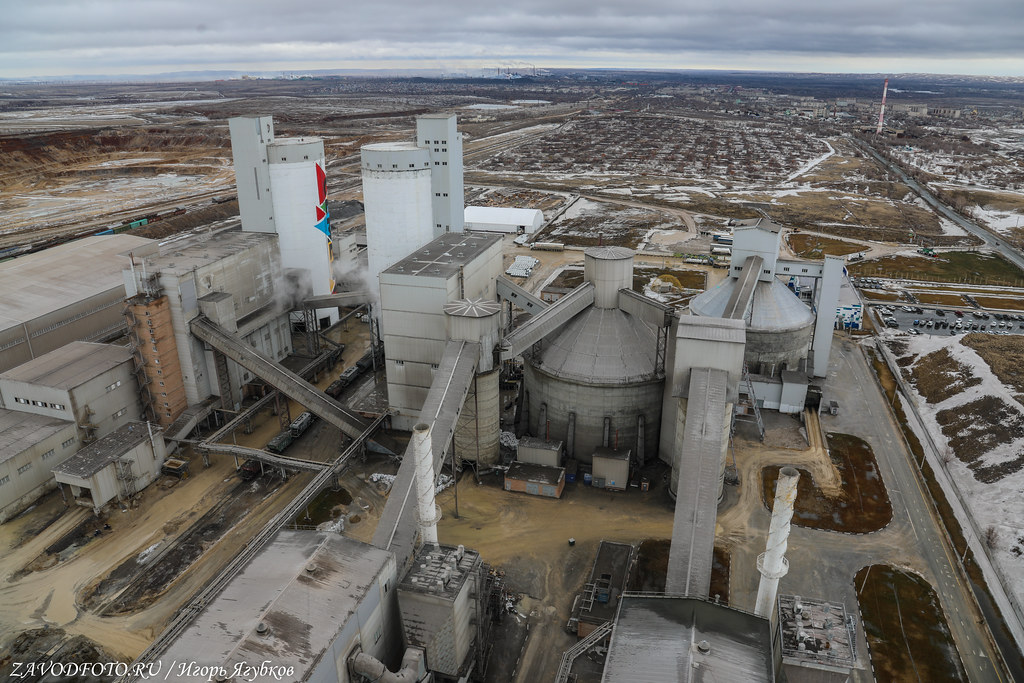
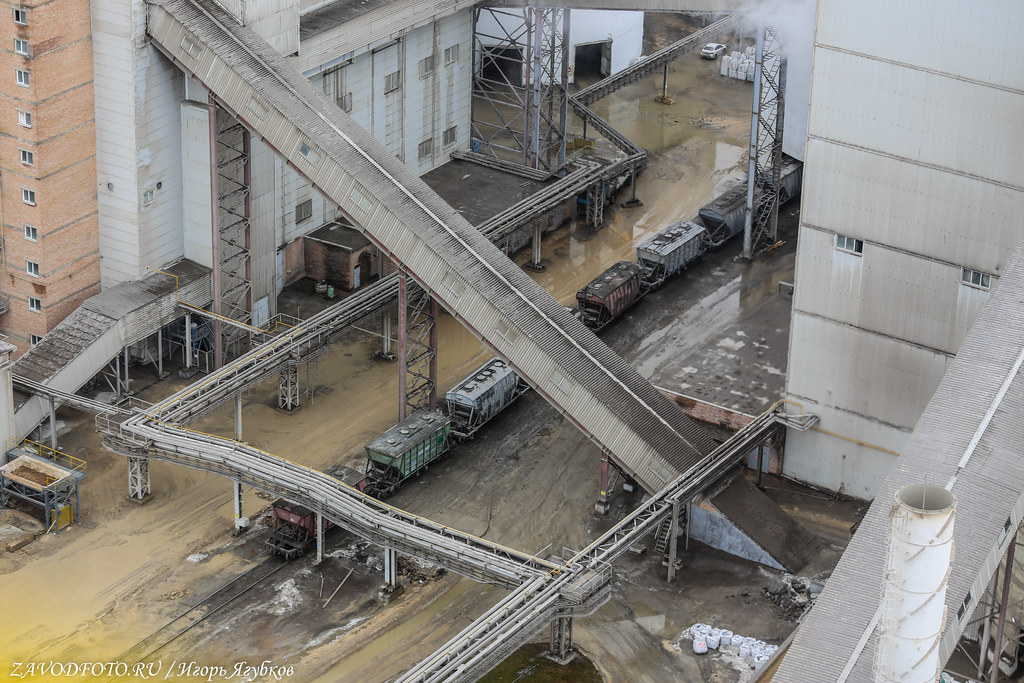
Эти два великана - многосекционные силосы для цемента. Внизу у них предусмотрена отгрузка в ж/д и автотранспорт.
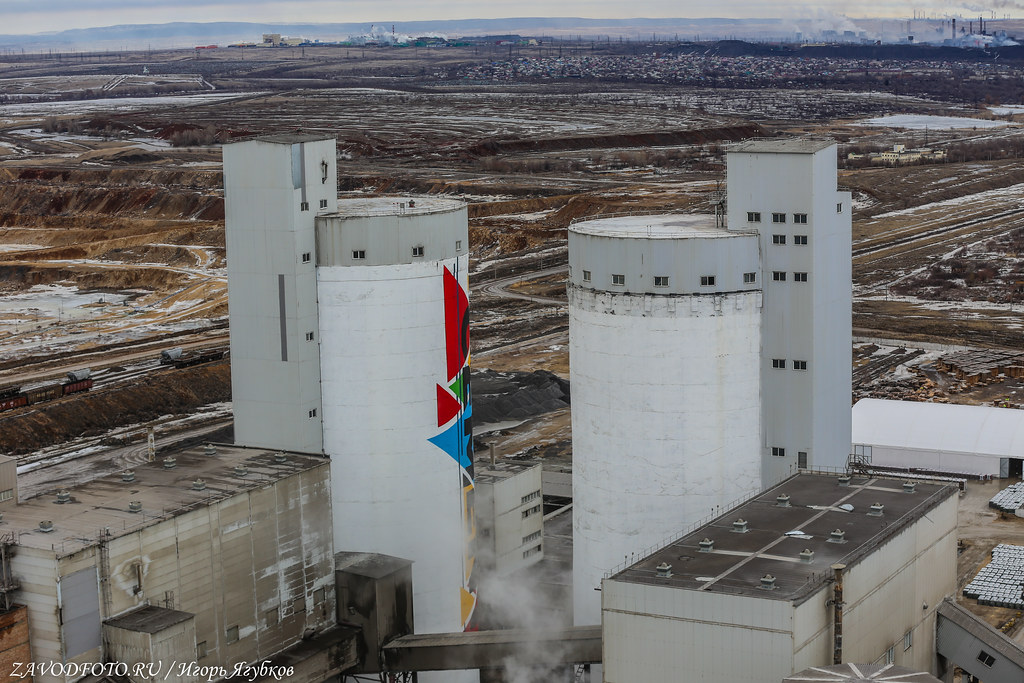
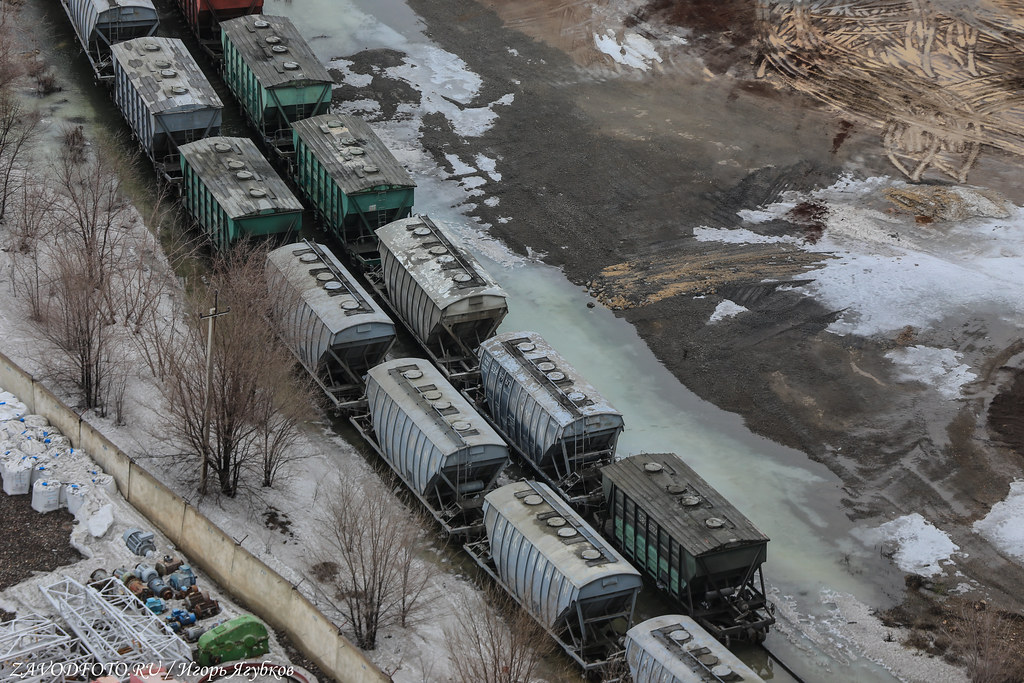
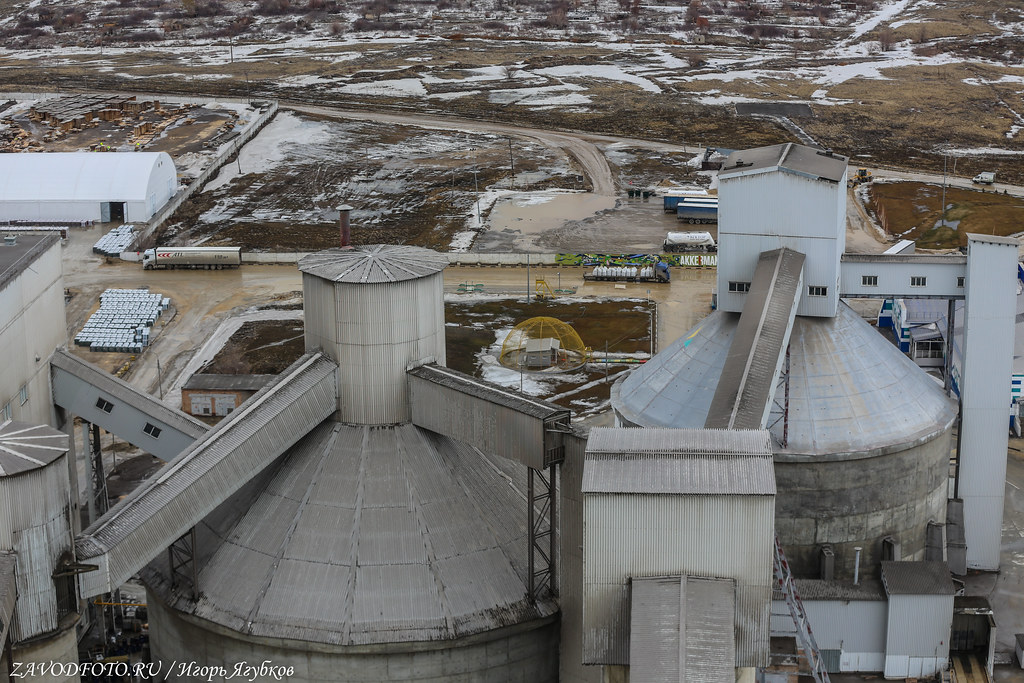
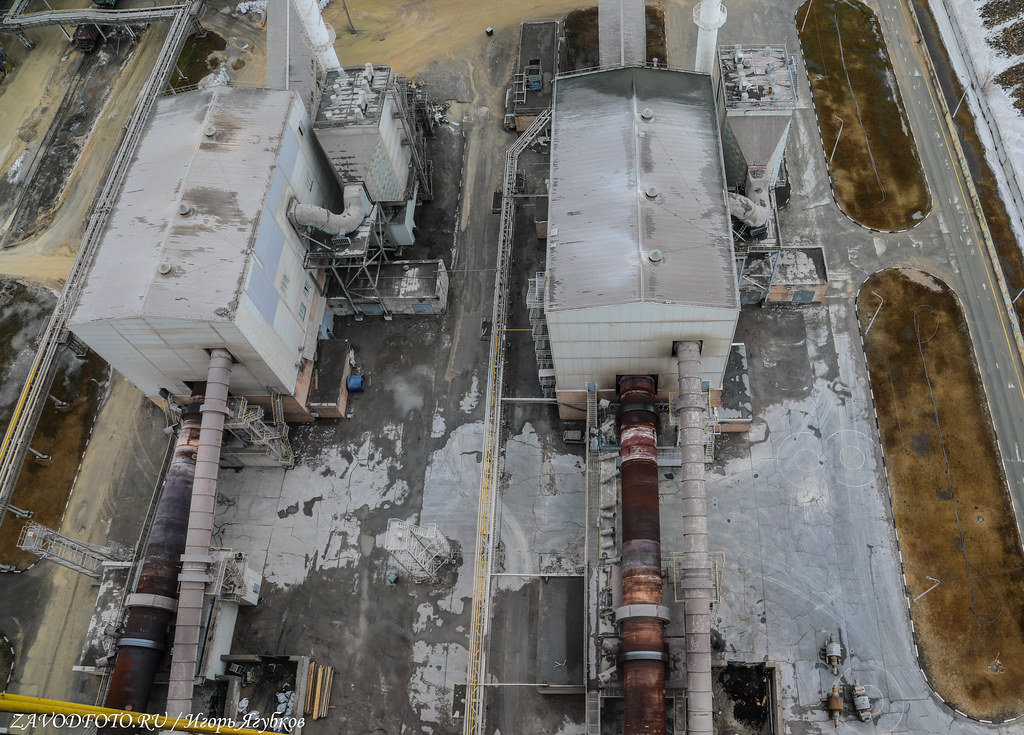
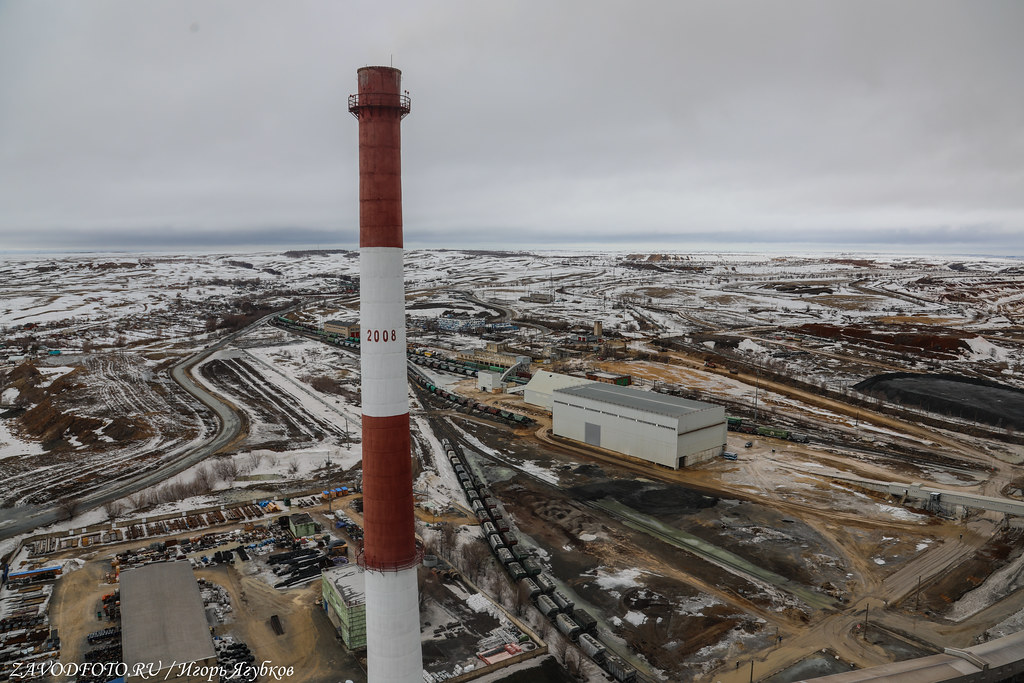

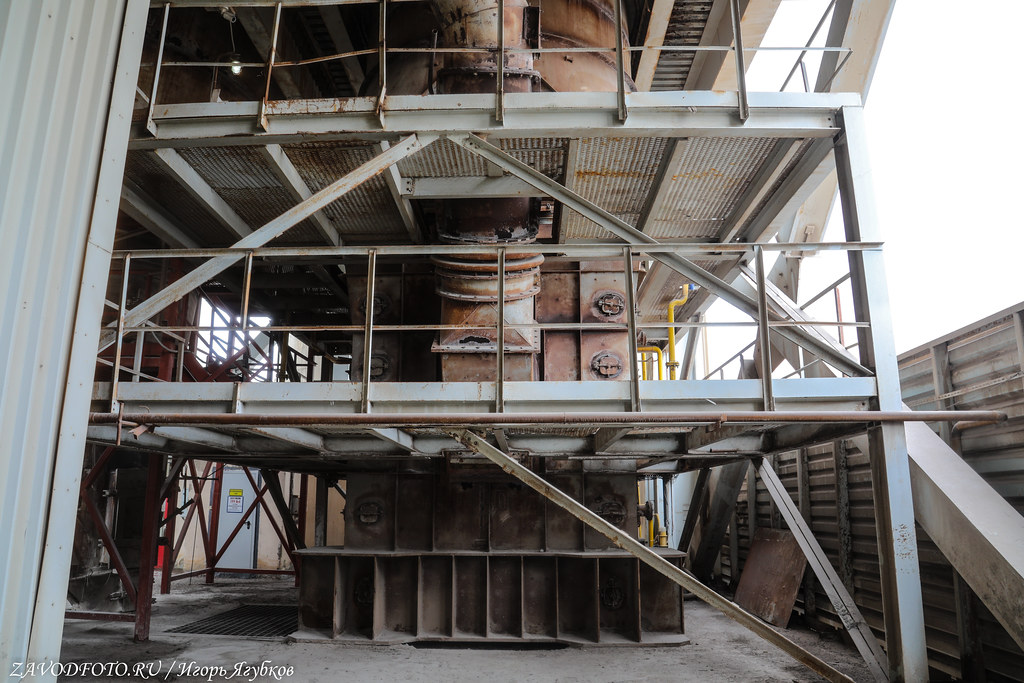
Перед нами главная горелка печи. Потребляет в среднем 5 000 м3 газа в час. В час она производит около 106 тонн клинкера в час. Цементный клинкер является основным ингредиентом в производстве цемента. Как мы уже поняли, это мелкий порошок, получаемый путем нагревания смеси известняка, глины и других минералов при высоких температурах. Впервые он был получен французом Луи Вика в 1817 году. Название клинкер происходит от его сходства с обожженным кирпичом (Клинкерный кирпич).
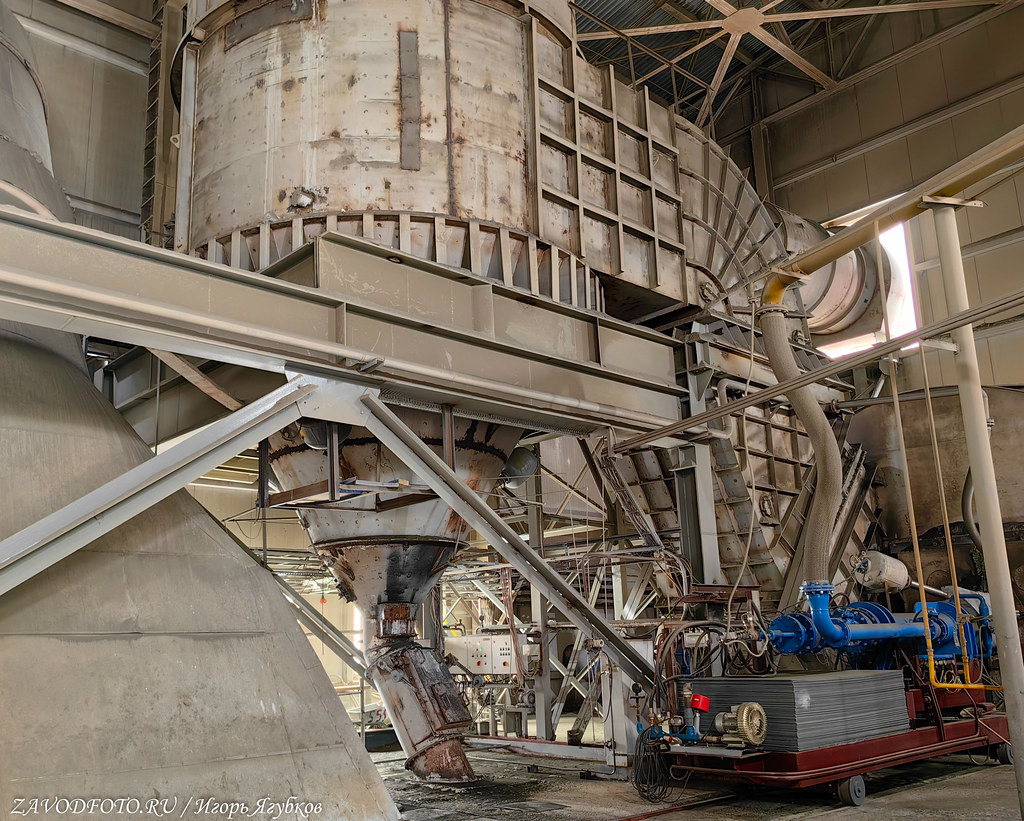
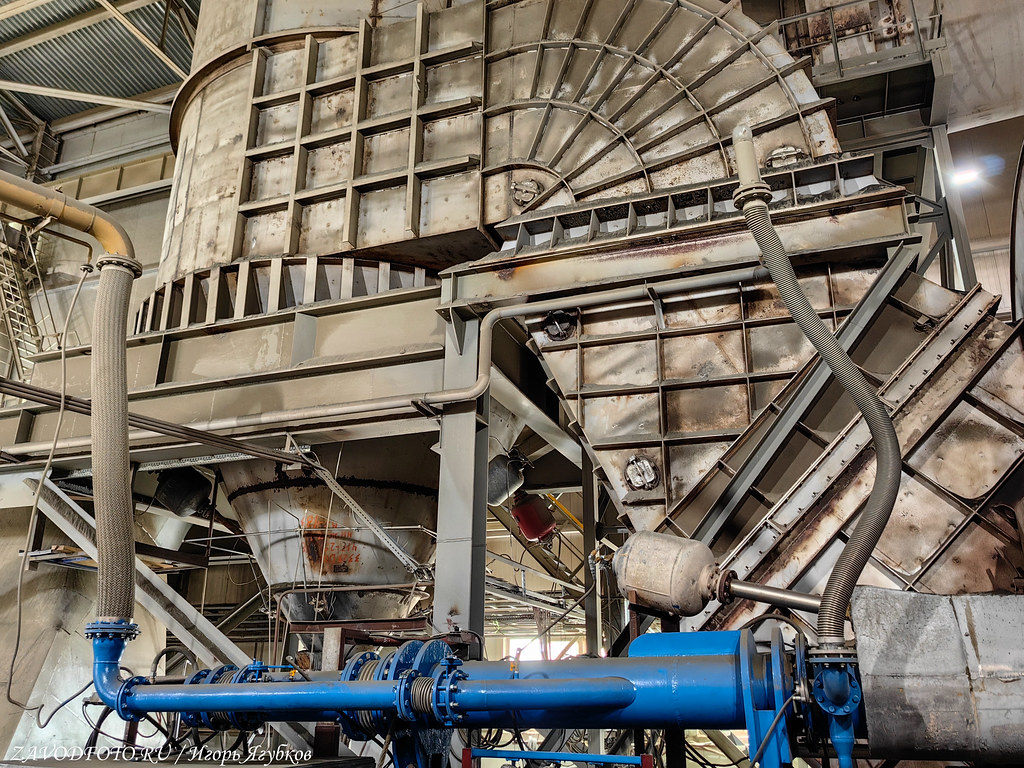

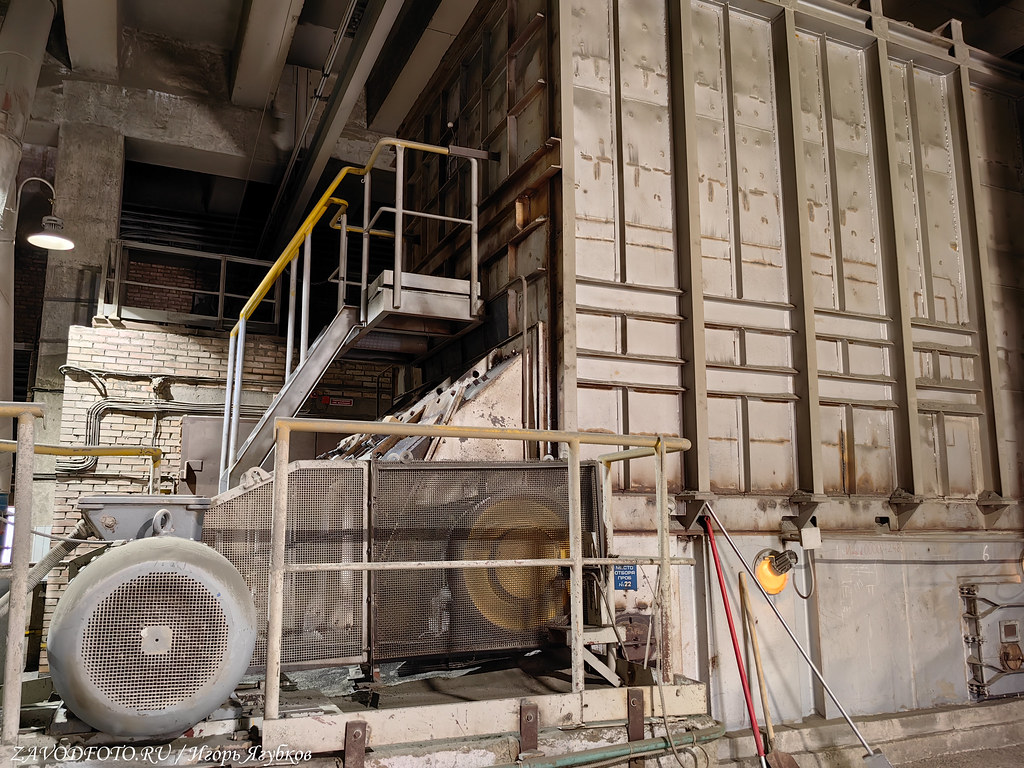
А это умный анализатор свободной извести по имени KLC 3. Вообще на предприятии много времени и сил отдают проверке на качество. К примеру, в соответствии с технологической документацией производства сырьевые материалы отбираются до 3-4 раз в смену, а пробы цемента и клинкера - каждые 2 часа. Оперативный контроль качества обжига клинкера осуществляют путем определения содержания свободной окиси кальция в клинкера, как химическим, так и петрографическим методом. Методом рентгеновской дифракции традиционно определяется фазовый состав материалов. Кроме того, рентгеновская дифрактометрия является наиболее прямым и эффективным способом определения количественных соотношений кристаллических и аморфных фаз материалов, определения их микроструктурных свойств, таких, как размеры кристаллитов, микродеформации, а также величина остаточных напряжений.
Не секрет, что повышенное содержание щелочей в цементе (более 0,8%) вызывает щелочную коррозию бетона, а это способствует образованию трещин. А повышенное содержание свободной окиси кальция CaOсв (более 1,5%) и окиси магния MgO (более 5%) оказывает значительное влияние на равномерность изменения объема при твердении цемента, вызывает усадочные деформации в бетонах. Повышенное содержание хлор-ионов Cl- - более 0,1% сказывается на возникновении коррозии арматуры в бетоне. Тонкость помола, гранулометрический состав цемента и удельная поверхность влияет на показатель НГЦТ, а, соответственно, на водопотребность цемента и бетонной смеси. Чем тоньше помол – тем больше воды потребляет цемент, и тем активнее происходит процесс гидратации. Сроки схватывания позволяют оценить время живучести (сохраняемости свойств) бетонной смеси, то есть в течение какого времени она останется подвижной и ее можно будет без проблем уложить в опалубку.
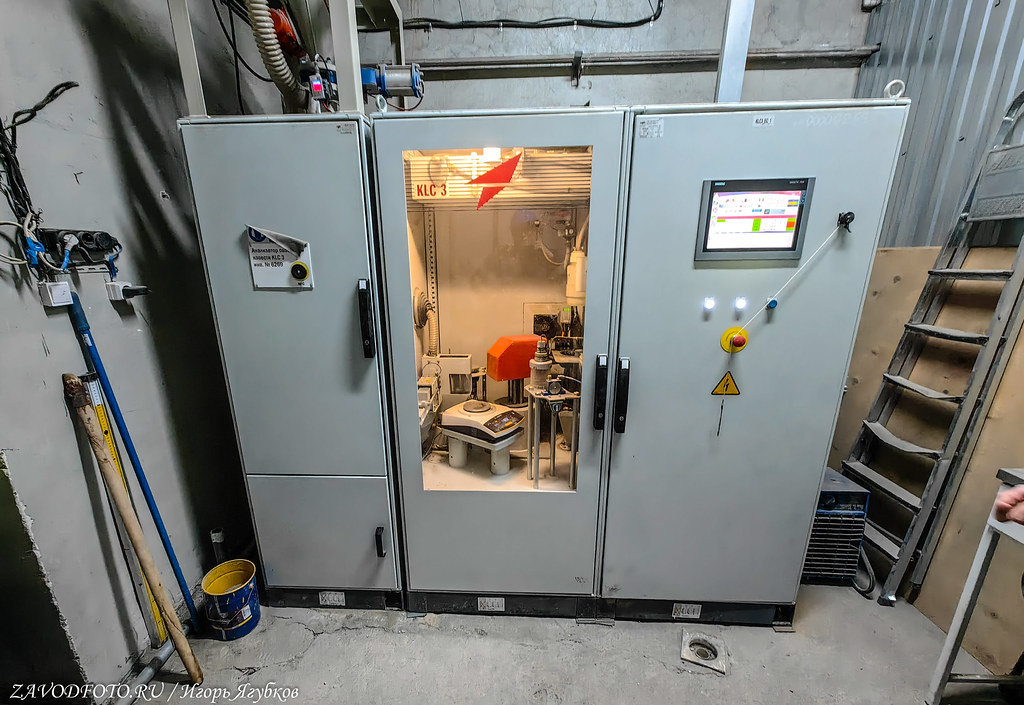
Далее клинкерную массу охлаждают, и отправляют в силосы ожидать дальнейшей переработки.
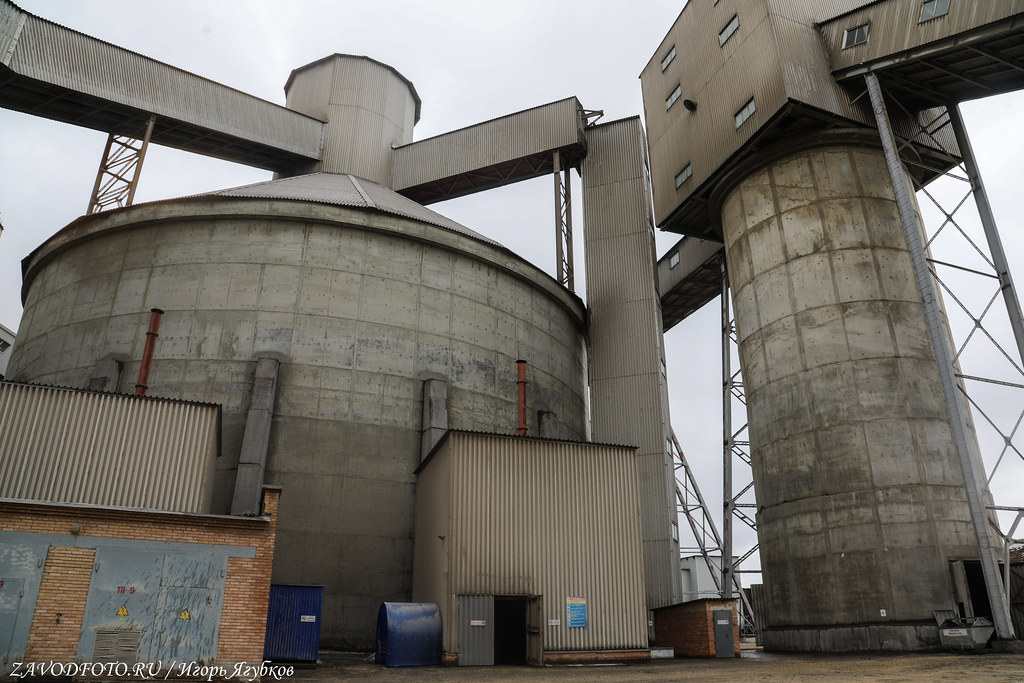
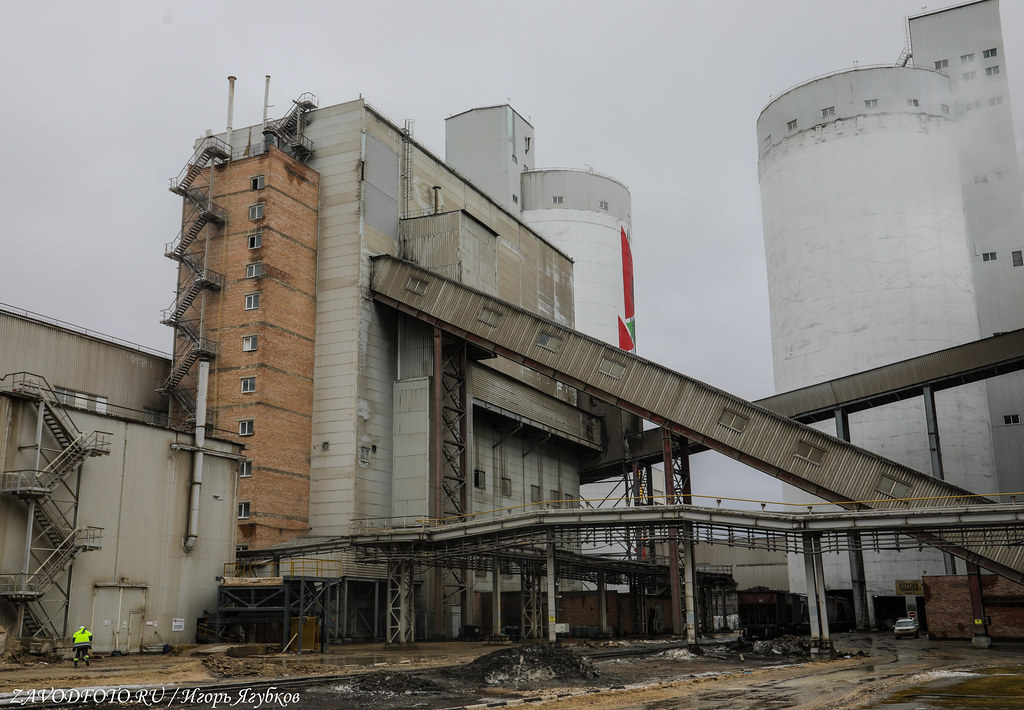

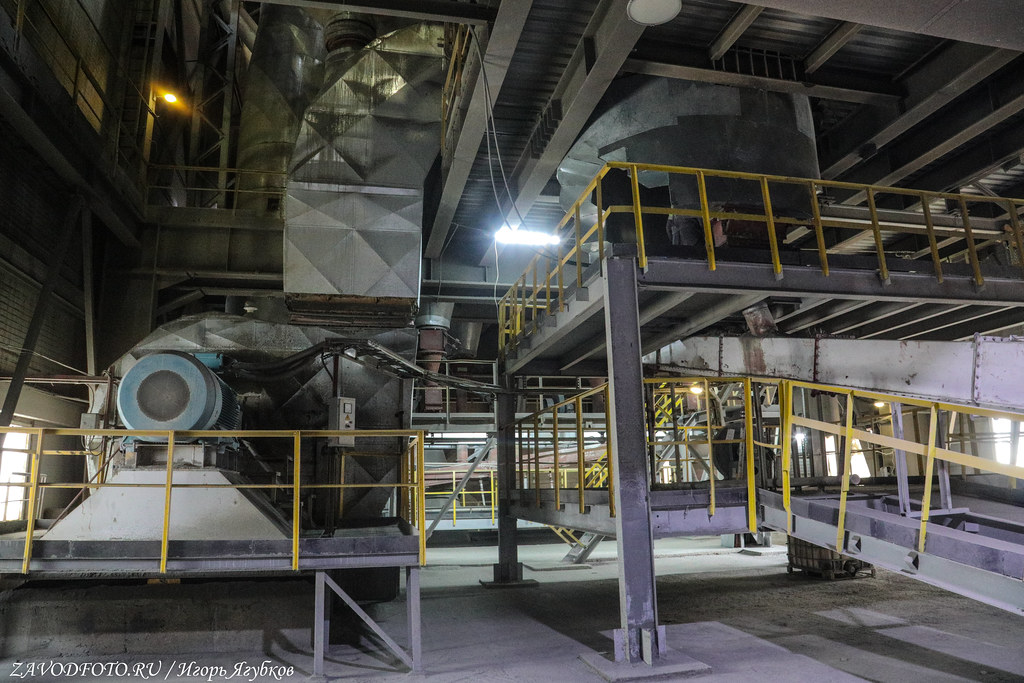
Дробилка для гипса.
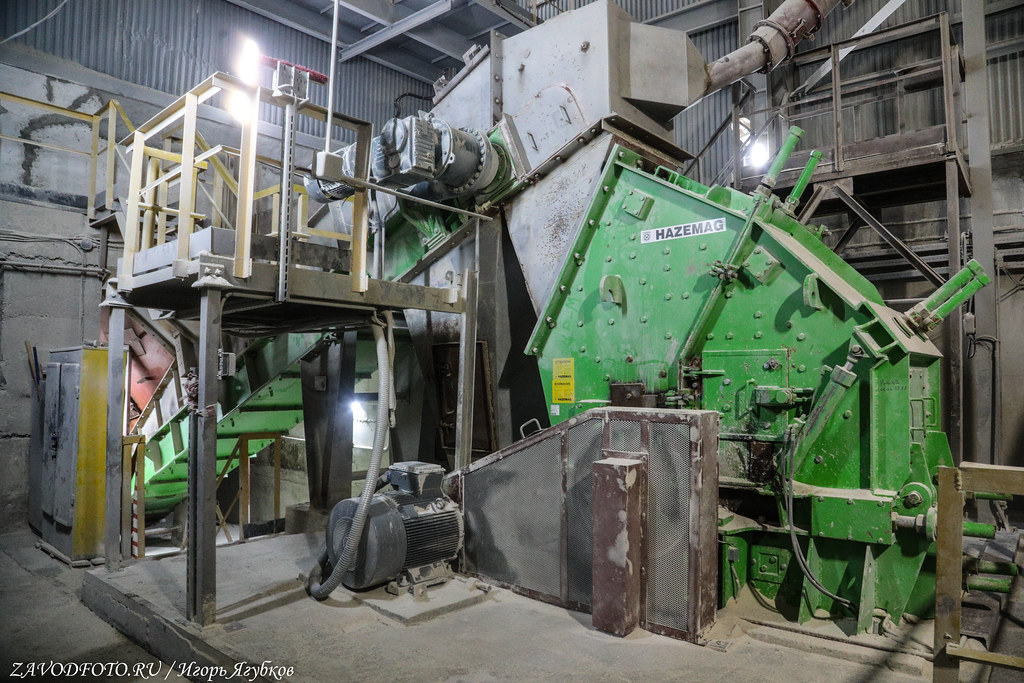
В настоящее время на заводе работают около 1300 человек.
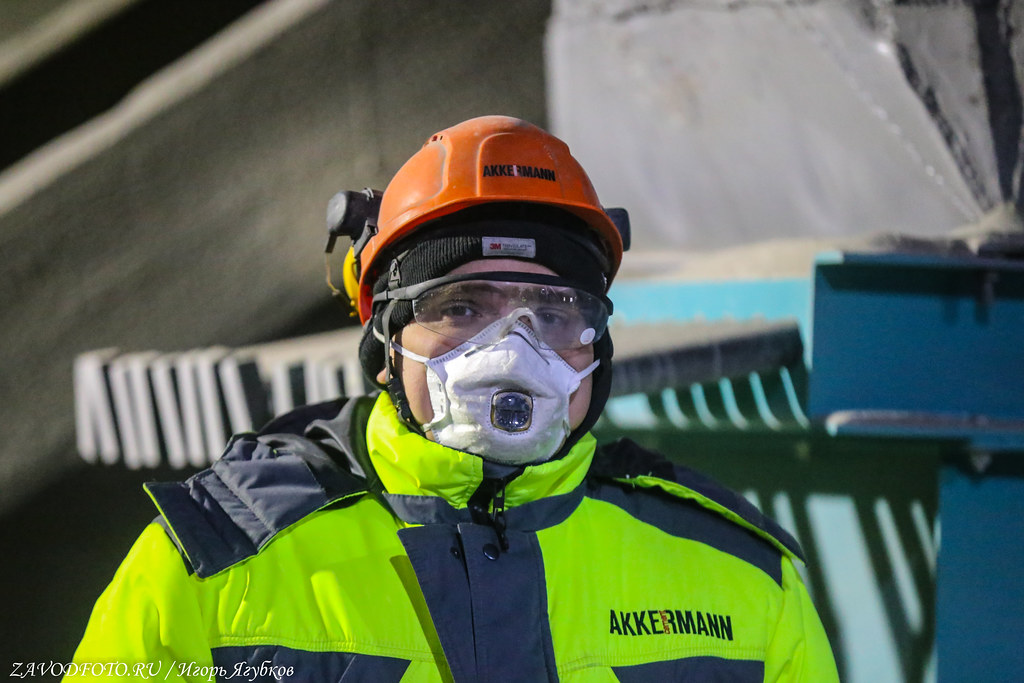
Дозаторы известняка
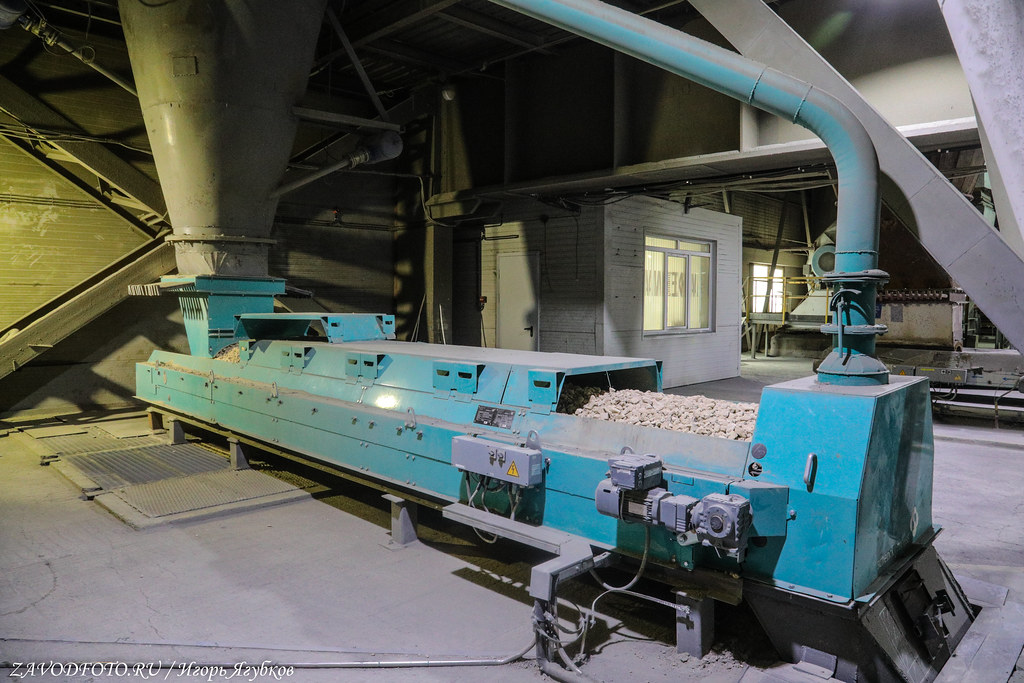
Теперь переходим непосредственно к производству цемента. Тонкоизмельченную смесь цементного клинкера смешивают с небольшим количеством других материалов, измельчают и получается цемент нужной марки. Все это происходит в мельнице. Она делает 14 оборотов в минуту.
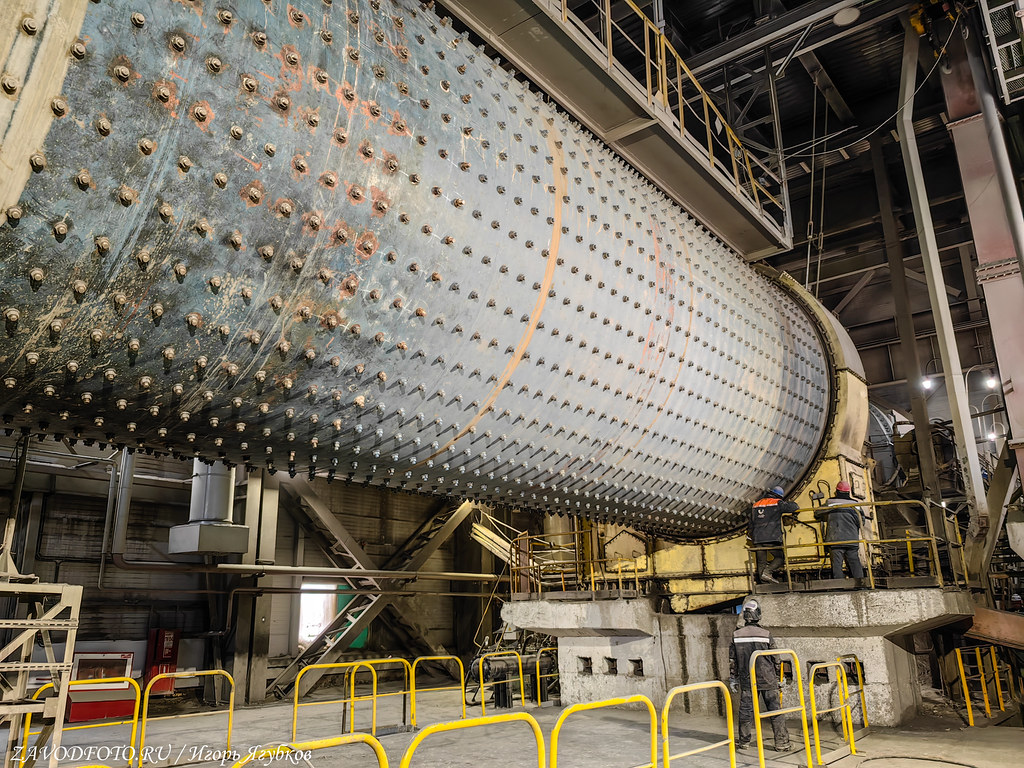
Правильно измельчать помогает вот такое умное ухо.
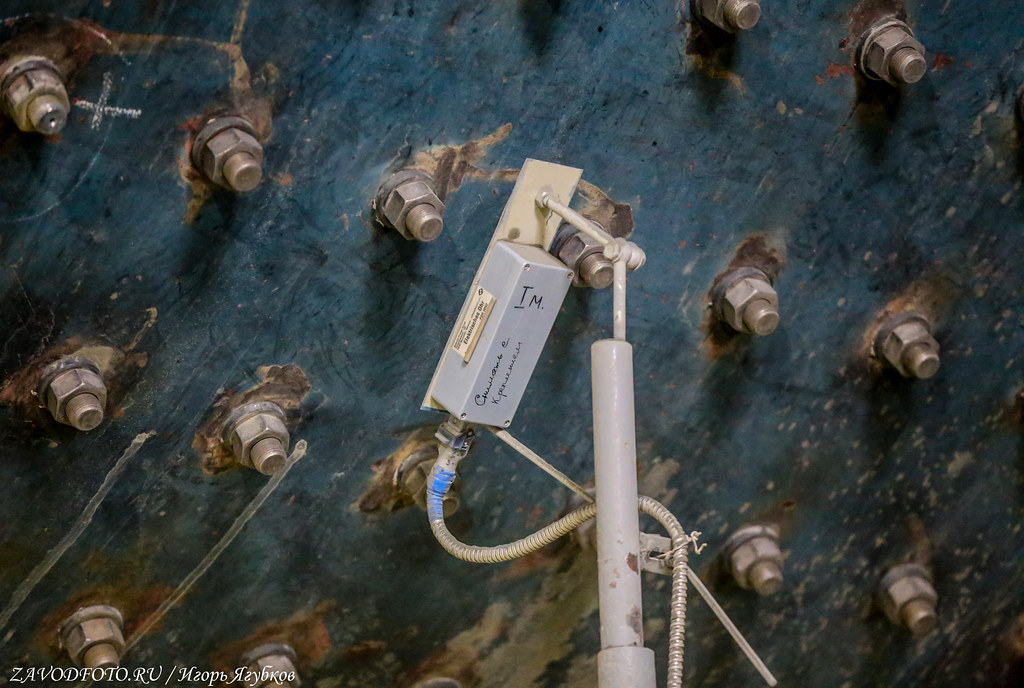
На этой установке получают нано-цемент. Он относится к цементам нового поколения по сравнению с портландцементом.
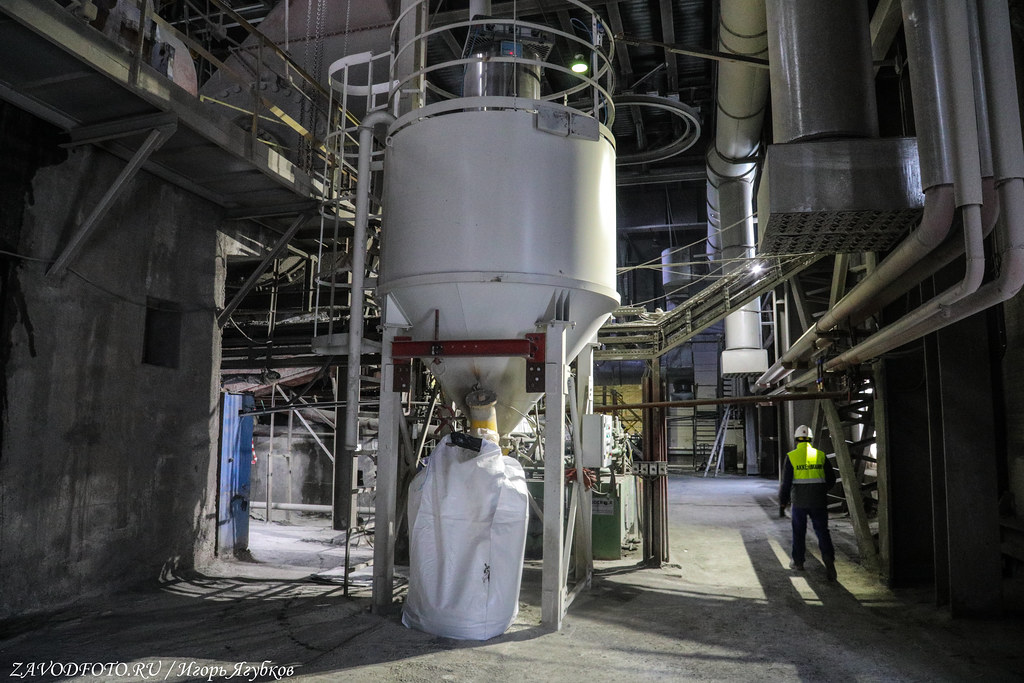
Далее цемент упаковывают в мешки по 50 кг и по 1 тонне. Его грузят в автотранспорт или вагоны. С территории завода уходит по 60-90 цементовозов в день. Так и начинается путешествие цемента под брендом AKKERMANN по России и не только.
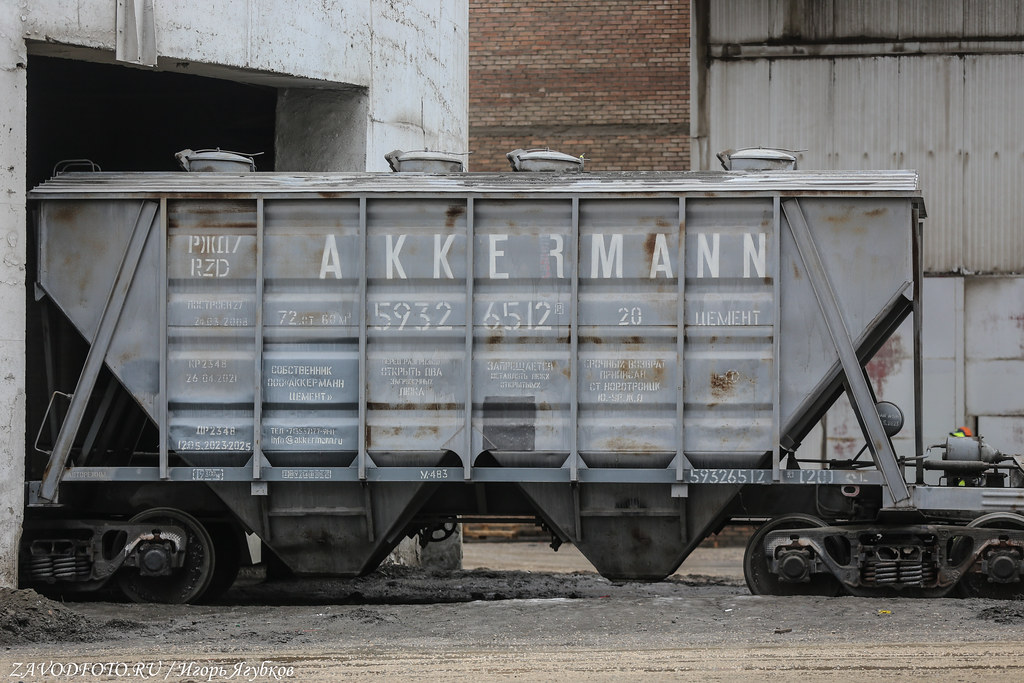
Большое спасибо компании ООО «АККЕРМАНН ЦЕМЕНТ» за открытость и тёплый приём! И в этот раз хочется снова упомянуть особую экономическую зону (ОЭЗ) «Оренбуржье», они такие молодцы, что готовы не только про себя рассказывать, но и со мной делиться полезными контактами, ведь благодаря им я попал и на это предприятие. Я добро помню, поэтому мне несложно и их в ответ похвалить. ОЭЗ «Оренбуржье» входит в ТОП самых инвестиционно привлекательных экономических зон в своей категории в России! Всего за несколько лет они смогли привлечь уже 15 резидентов, и это, я так понимаю, только начало. Территориально данная ОЭЗ располагается на двух площадках: в Оренбурге (380 га) и в Орске (180 га).
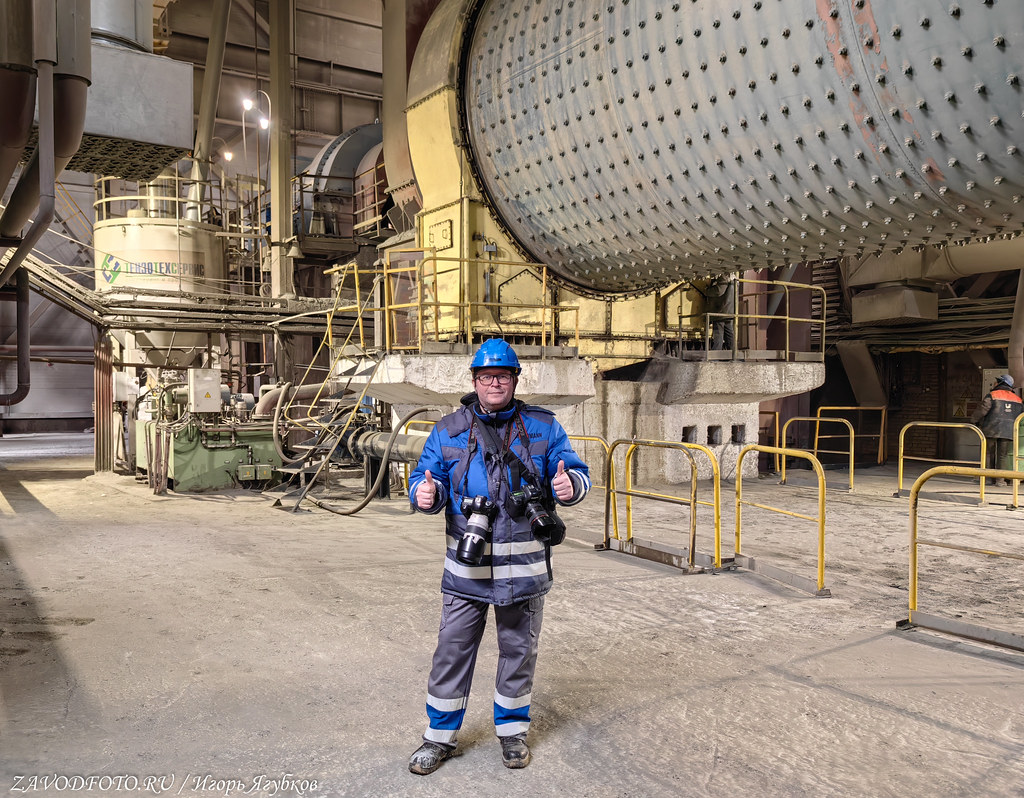
Ещё из моих поездок в Оренбургскую область:

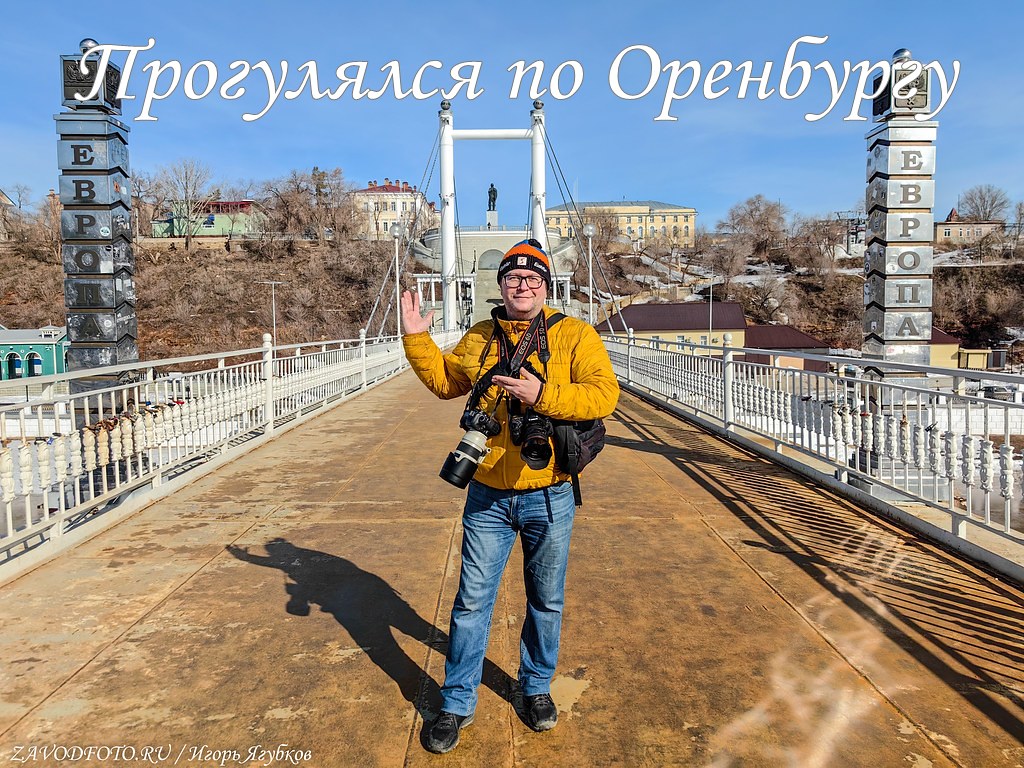
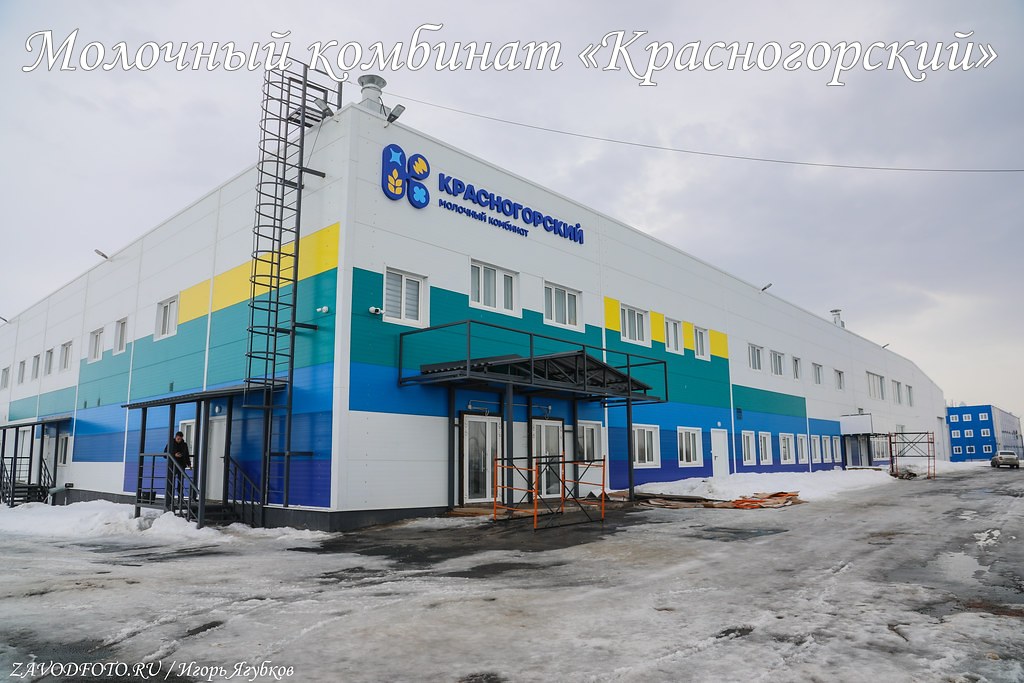

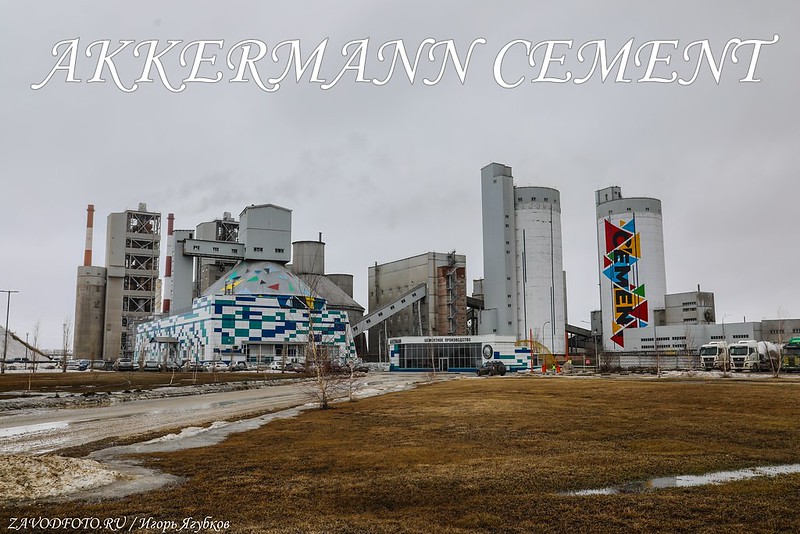
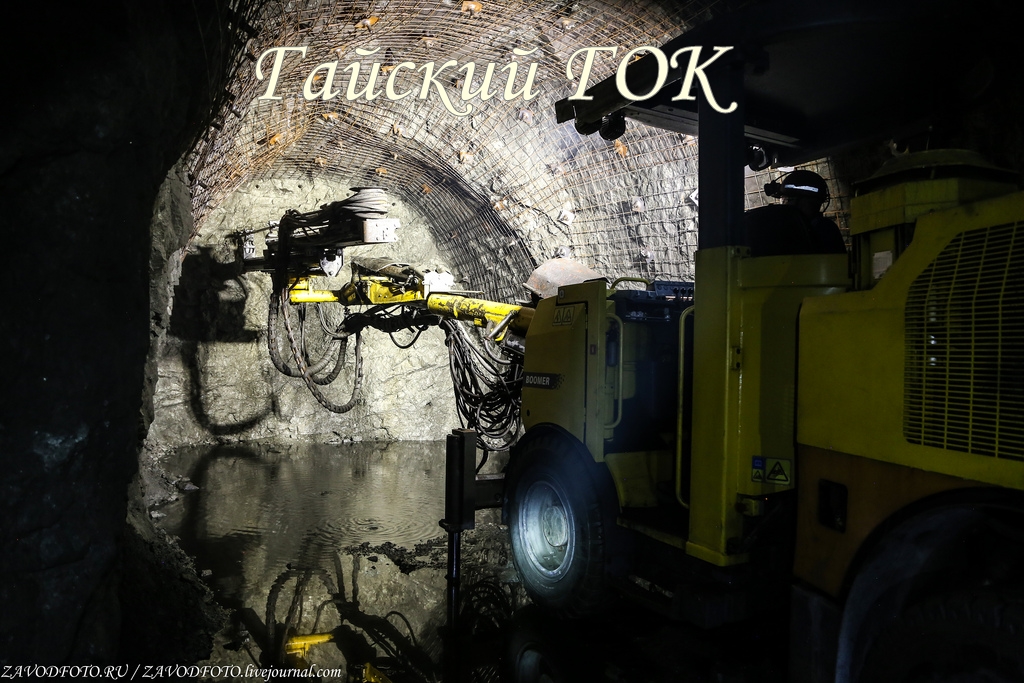
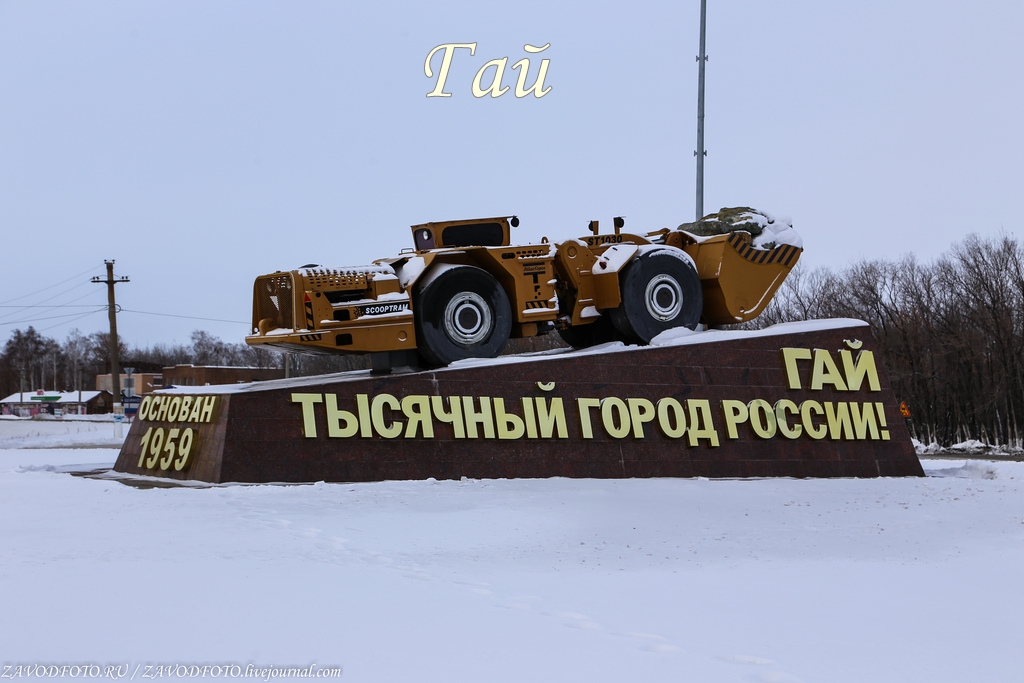
P. S. Уважаемые собственники и акционеры, представители пресс-служб компаний, отделы маркетинга и другие заинтересованные лица, если на Вашем предприятии есть, что показать - "Как это делается и почему именно так!", смело приглашайте в гости. Для этого пишите мне сюда: akciirosta@yandex.ru Берите пример с лидеров! На данный момент я уже лично посетил более 600 предприятий, а вот и ссылки на все мои промрепортажи:
Почему наша промышленность самая лучшая в мире: http://zavodfoto.livejournal.com/4701859.html
Я всегда рад новым друзьям, добавляйтесь и читайте меня в:
Дзен / LiveJournal / ВК / Одноклассники
Есть возможность внести свою лепту в развитие блога, будем рады донату (реквизиты карты): 5536 9177 1972 2396
Взято: Тут
884