Dagar
Как в Балтийском море укладывали трубы для "Северного потока" ( 6 фото )
Как это возможно — уложить сотни километров стальных труб на огромную глубину, на дно со сложным рельефом? Как добиться, чтобы вся эта конструкция выдерживала огромное давление, не смещалась, не была уничтожена коррозией, выдерживала удары корабельных якорей и рыболовного снаряжения и, наконец, просто работала как надо? Самым свежим примером сооружения подводного мегатрубопровода стал знаменитый «Северный поток», пролегший по балтийскому дну и соединивший российскую и немецкую газотранспортные системы. Две нитки труб, каждая длиной более 1200 км — почти 2,5 млн тонн стали, поглощенных морем по воле человека. Именно на примере «Северного потока» мы попытаемся вкратце рассказать о технологиях создания подводных трубопроводов.
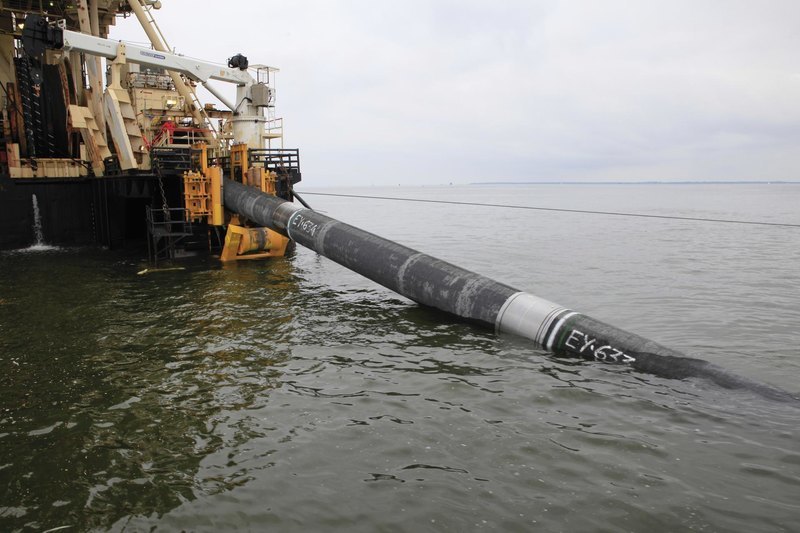
Две нитки газопровода состоят из 199 755 двенадцатиметровых труб, сделанных из высокосортной углеродистой стали. Но коль скоро речь идет о соприкосновении с такой химически агрессивной средой, как морская вода, металлу нужна защита. Для начала на внешнюю поверхность трубы наносят трехслойное покрытие из эпоксидного состава и полиэтилена — это делается прямо на заводе-производителе. Там же, кстати, трубу покрывают и изнутри, правда, задача внутреннего покрытия не в защите от коррозии, а в повышении пропускной способности газопровода. Красно-коричневая эпоксидная краска дает очень гладкую, глянцевую поверхность, снижающую, насколько это возможно, трение молекул газа о стенки трубы.
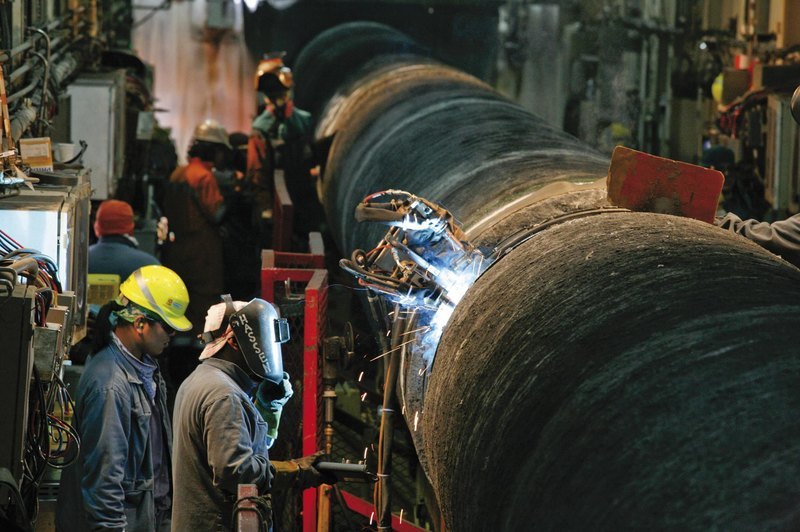
Можно ли укладывать такую трубу на морское дно? Нет, ее требуется дополнительно защищать и усиливать против давления воды и электрохимических процессов. На трубы устанавливают так называемую катодную защиту (наложение отрицательного потенциала на защищаемую поверхность). С определенным шагом к трубам приваривают электроды, соединенные между собой анодным кабелем, который связан с источником постоянного тока. Таким образом, процесс коррозии переносится на аноды, а в защищаемой поверхности проходит только неразрушающий катодный процесс. Но главное, что еще предстоит сделать с трубой, прежде чем она будет готова опуститься на дно, — это обетонирование.
На специальных заводах внешнюю поверхность трубы покрывают слоем бетона толщиной 60−110 мм. Покрытие армируется приваренными к корпусу стальными стержнями, в бетон добавляется наполнитель в виде железной руды — для утяжеления. После обетонирования труба приобретает вес около 24 т. У нее появляется серьезная защита против механических воздействий, а дополнительная масса позволяет ей стабильно лежать на дне.
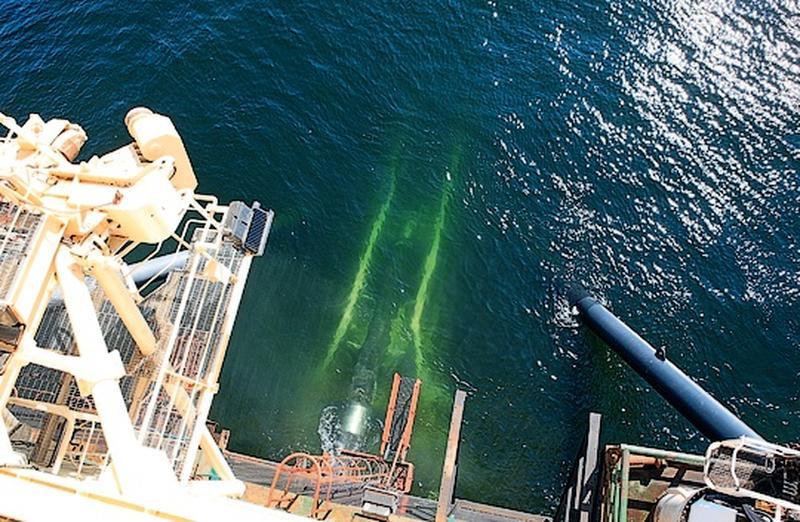
Но надо помнить, что дно даже такого сравнительно неглубокого моря, как Балтийское, не предоставит само по себе удобного и безопасного ложа для газопровода. Есть два фактора, которые неизбежно приходилось учитывать проектировщикам и строителям «Северного потока»: антропогенный и природный.
История судоходства в североевропейском регионе насчитывает тысячелетия, и потому на дне моря скопилось немало всевозможного мусора, а также обломков затонувших кораблей. XX век внес свой страшный вклад: на Балтике в ходе мировых войн велись активные боевые действия, устанавливались сотни тысяч морских мин, а по окончании войн в море же утилизировались боеприпасы, в том числе и химические. Поэтому, во‑первых, при прокладке маршрута газопровода требовалось обходить выявленные скопления опасных артефактов, а во-вторых, тщательно обследовать зону прокладки, включая так называемый якорный коридор (по километру влево и вправо от будущей трассы), то есть зону, в которой бросали якоря суда, задействованные в строительстве.
В частности, для мониторинга боеприпасов применялись корабли, оснащенные эхолокационным оборудованием, а также специальным донным роботом (ROV), связанным кабелем с базовой донной станцией TMS. При обнаружении боеприпасов (морские мины весьма чувствительны к движению) их подрывали на месте, предварительно обеспечив безопасность судоходства в заданном районе и приняв меры по отпугиванию крупных морских животных.

Второй фактор, природный, связан c особенностями рельефа дна. Дно моря сложено из различных пород, оно имеет выступающие гребни, впадины, расселины, и опускать трубы прямо на все это геологическое разнообразие не всегда возможно. Если допустить большое провисание нитки газопровода между двумя естественными опорами, конструкция может со временем разрушиться со всеми вытекающими из этого неприятностями. Поэтому донный рельеф для прокладки необходимо искусственным образом исправлять.
Если требовалось выровнять рельеф дна, использовалась так называемая каменная наброска. Специальное судно, нагруженное гравием и мелкими камнями, с помощью трубы, нижний конец которой оборудован соплами, «прицельно» заполняло полости дна, придавая ему более подходящий профиль. Иногда вместо камней вниз опускались целые бетонные плиты. Другой вариант — выкапывание в дне траншеи для прокладки труб.
Логично предположить, что создание траншей предшествовало прокладке труб, однако далеко не всегда это происходило именно так. Существует техническая возможность стабилизации положения нитки на дне уже тогда, когда трубопровод проложен (при условии, что глубина моря в данной точке не превышает 15−20 м). В этом случае с судна на дно опускается траншеекопатель, имеющий роликовые захваты. С их помощью трубопровод приподнимается со дна, и под ним пропахивается траншея. После проведения этой операции трубы укладываются в получившееся углубление.
Сыпать тяжелый грунт на дно можно не всегда: масса гравия продавливает мягкие породы. В этом случае для «спрямления» рельефа используют более легкие опоры из металлических или пластиковых конструкций.

Теперь, пожалуй, самое интересное: как трубы оказываются на дне? Разумеется, сложно себе представить, что каждая отдельная 12-метровая труба приваривается к нитке газопровода прямо в море на глубине. Значит, эту процедуру необходимо проделывать до укладки. Что, собственно, и происходит на борту трубоукладочного судна.
Тут необходимо ненадолго вернуться к конструкции самой трубы и заметить, что после нанесения на нее антикоррозионной защиты и утяжеляющего бетонирования оконцовки труб остаются открытыми и незащищенными, — иначе сварка была бы затруднена. Поэтому участки соединений защищаются от коррозии уже после сварки. Сначала монтажные стыки изолируются с помощью полиэтиленового термоусадочного рукава, затем закрываются металлическим кожухом, а полость между кожухом и рукавом заполняется полиуретановой пеной, придающей месту стыка необходимую механическую прочность.
Далее происходит укладка S-образным способом. Сваренная из труб плеть приобретает в процессе укладки форму, напоминающую латинскую букву S. Плеть под небольшим углом выходит из кормы корабля, достаточно резко опускается вниз и достигает дна, где принимает горизонтальное положение. Труднее всего представить себе, что нить из стальных, покрытых бетоном 24-тонных труб способна к таким резким изгибам без разрушения, однако все происходит именно так.
Разумеется, для того чтобы плеть не сломалась, применяются разнообразные технологические хитрости. За трубоукладочным судном на десятки метров тянется стингер — специальное ложе, уменьшающее радиус наклона уходящей вниз плети. На судне также установлено натяжное устройство, прижимающее трубы книзу и снижающее нагрузки на изгибы. Наконец, система позиционирования точно контролирует положение судна, исключая рывки и резкие смещения, способные повредить трубопровод. Если укладку почему-либо требуется прервать, вместо очередной трубы к плети приваривают герметичную заглушку с креплениями и плеть «сбрасывают» на дно. При возобновлении работ другой корабль подцепит заглушку тросом и вытянет плеть обратно наверх.
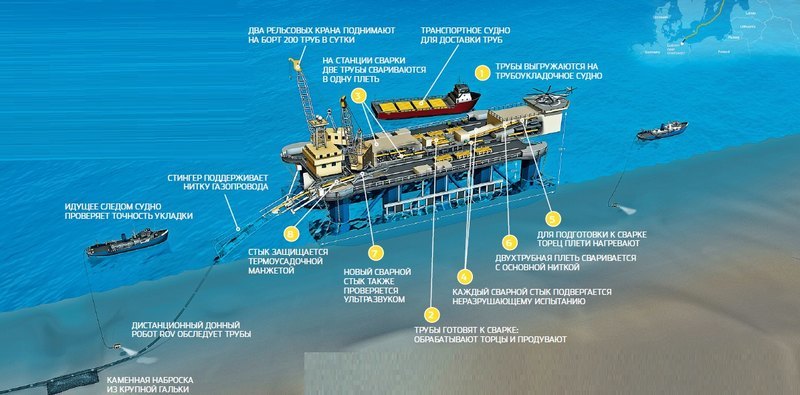
И все же без подводной сварки не обошлось. Дело в том, что каждая из ниток «Северного потока» состоит из трех секций. Различие между секциями — разная толщина стенок используемых труб. Пока газ идет от терминала в российской бухте Портовая к приемному терминалу на немецком берегу, давление газа постепенно падает. Это дало возможность использовать в центральной и финальной секциях более тонкостенные трубы и таким образом экономить металл. Вот только обеспечить соединение разных труб на борту трубоукладочных судов не представляется возможным. Сочленение секций происходило уже на дне — в гидроизолированной сварочной камере.
Для этого на дно опускались трубоподъемные механизмы, которые отрывали от дна и точно позиционировали друг напротив друга плети отдельных секций. Для той же цели применялись надувные мешки с переменной плавучестью, обеспечивавшие вертикальные перемещения труб. Термобарическая сварка велась в автоматическом режиме, однако наладка оборудования сварочной камеры — сложнейшая водолазная операция. Для ее проведения под воду опускалась водолазная камера, где могла проходить декомпрессию целая бригада водолазов, и специальный колокол для спуска ко дну. Сварка секций проводилась на глубине 80−110 м.
Прежде чем использовать газопровод для перекачки топлива, его испытывали… водой. Внутрь секций с помощью поршневого модуля была закачана предварительно отфильтрованная от взвесей и даже бактерий морская вода. Жидкость, нагнетавшаяся со специального судна, создавала внутри плети давление, превышающее рабочее, и такой режим поддерживался в течение суток. Затем вода откачивалась, и секция газопровода осушалась. Еще до того, как в трубопроводе появился природный газ, его трубы заполнялись азотом.
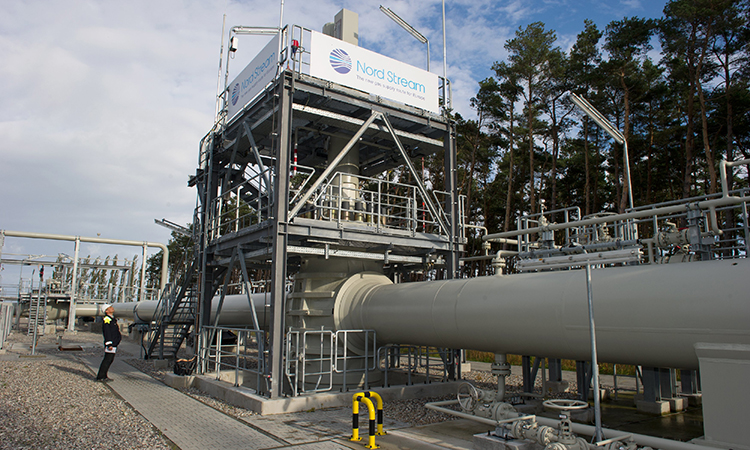
Прокладка газопровода по морскому дну — лишь часть проекта «Северный поток». Немало усилий и затрат потребовалось для оборудования береговой инфраструктуры. Отдельная история — это вытягивание нитки газопровода на берег с помощью мощной лебедки или создание механизма компенсации сезонного сжатия-расширения 1200-километровой нитки.

Строительство «Северного потока» вызвало немало дискуссий на разные околополитические темы — от экологии до чрезмерной роли сырьевого экспорта в экономике России. Но если абстрагироваться от политики, нельзя не заметить: трансбалтийский газопровод — отличный пример того, как продвинутые технологии и международная кооперация способны творить современные чудеса во вполне рабочем рутинном режиме.
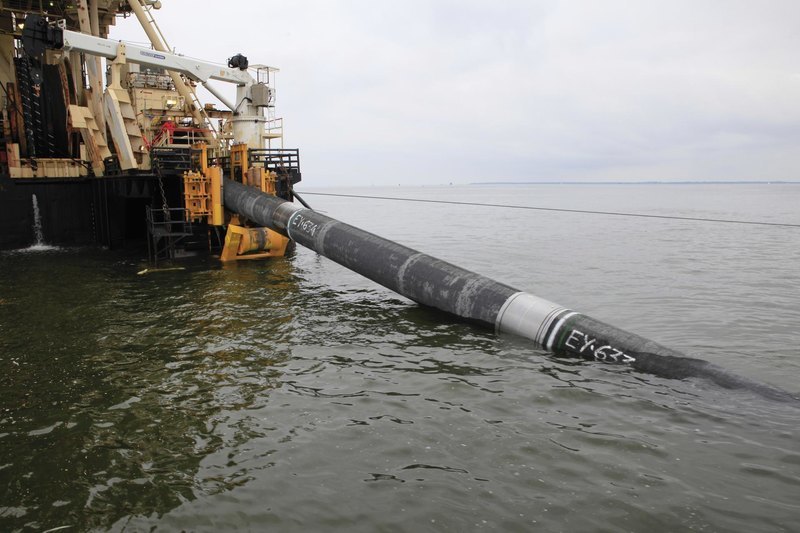
Две нитки газопровода состоят из 199 755 двенадцатиметровых труб, сделанных из высокосортной углеродистой стали. Но коль скоро речь идет о соприкосновении с такой химически агрессивной средой, как морская вода, металлу нужна защита. Для начала на внешнюю поверхность трубы наносят трехслойное покрытие из эпоксидного состава и полиэтилена — это делается прямо на заводе-производителе. Там же, кстати, трубу покрывают и изнутри, правда, задача внутреннего покрытия не в защите от коррозии, а в повышении пропускной способности газопровода. Красно-коричневая эпоксидная краска дает очень гладкую, глянцевую поверхность, снижающую, насколько это возможно, трение молекул газа о стенки трубы.
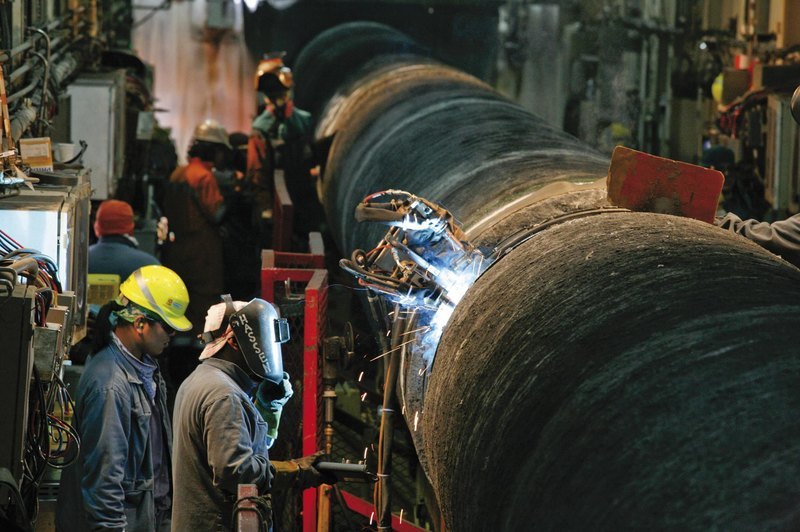
Можно ли укладывать такую трубу на морское дно? Нет, ее требуется дополнительно защищать и усиливать против давления воды и электрохимических процессов. На трубы устанавливают так называемую катодную защиту (наложение отрицательного потенциала на защищаемую поверхность). С определенным шагом к трубам приваривают электроды, соединенные между собой анодным кабелем, который связан с источником постоянного тока. Таким образом, процесс коррозии переносится на аноды, а в защищаемой поверхности проходит только неразрушающий катодный процесс. Но главное, что еще предстоит сделать с трубой, прежде чем она будет готова опуститься на дно, — это обетонирование.
На специальных заводах внешнюю поверхность трубы покрывают слоем бетона толщиной 60−110 мм. Покрытие армируется приваренными к корпусу стальными стержнями, в бетон добавляется наполнитель в виде железной руды — для утяжеления. После обетонирования труба приобретает вес около 24 т. У нее появляется серьезная защита против механических воздействий, а дополнительная масса позволяет ей стабильно лежать на дне.
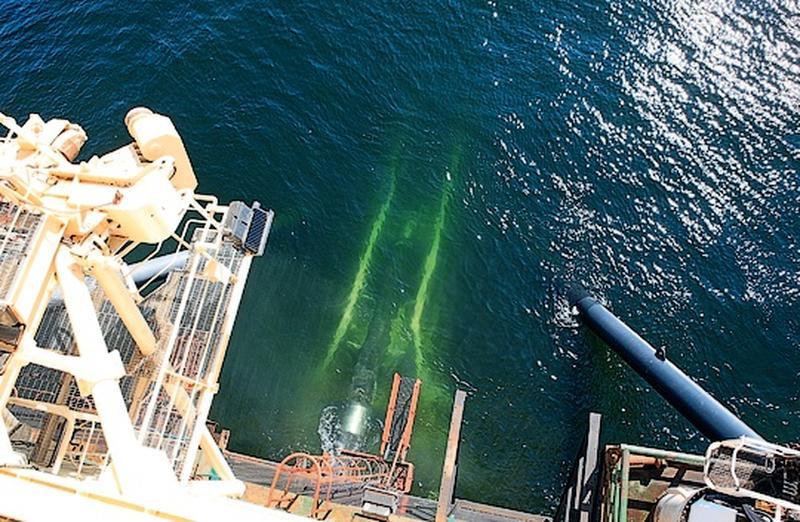
Но надо помнить, что дно даже такого сравнительно неглубокого моря, как Балтийское, не предоставит само по себе удобного и безопасного ложа для газопровода. Есть два фактора, которые неизбежно приходилось учитывать проектировщикам и строителям «Северного потока»: антропогенный и природный.
История судоходства в североевропейском регионе насчитывает тысячелетия, и потому на дне моря скопилось немало всевозможного мусора, а также обломков затонувших кораблей. XX век внес свой страшный вклад: на Балтике в ходе мировых войн велись активные боевые действия, устанавливались сотни тысяч морских мин, а по окончании войн в море же утилизировались боеприпасы, в том числе и химические. Поэтому, во‑первых, при прокладке маршрута газопровода требовалось обходить выявленные скопления опасных артефактов, а во-вторых, тщательно обследовать зону прокладки, включая так называемый якорный коридор (по километру влево и вправо от будущей трассы), то есть зону, в которой бросали якоря суда, задействованные в строительстве.
В частности, для мониторинга боеприпасов применялись корабли, оснащенные эхолокационным оборудованием, а также специальным донным роботом (ROV), связанным кабелем с базовой донной станцией TMS. При обнаружении боеприпасов (морские мины весьма чувствительны к движению) их подрывали на месте, предварительно обеспечив безопасность судоходства в заданном районе и приняв меры по отпугиванию крупных морских животных.
Второй фактор, природный, связан c особенностями рельефа дна. Дно моря сложено из различных пород, оно имеет выступающие гребни, впадины, расселины, и опускать трубы прямо на все это геологическое разнообразие не всегда возможно. Если допустить большое провисание нитки газопровода между двумя естественными опорами, конструкция может со временем разрушиться со всеми вытекающими из этого неприятностями. Поэтому донный рельеф для прокладки необходимо искусственным образом исправлять.
Если требовалось выровнять рельеф дна, использовалась так называемая каменная наброска. Специальное судно, нагруженное гравием и мелкими камнями, с помощью трубы, нижний конец которой оборудован соплами, «прицельно» заполняло полости дна, придавая ему более подходящий профиль. Иногда вместо камней вниз опускались целые бетонные плиты. Другой вариант — выкапывание в дне траншеи для прокладки труб.
Логично предположить, что создание траншей предшествовало прокладке труб, однако далеко не всегда это происходило именно так. Существует техническая возможность стабилизации положения нитки на дне уже тогда, когда трубопровод проложен (при условии, что глубина моря в данной точке не превышает 15−20 м). В этом случае с судна на дно опускается траншеекопатель, имеющий роликовые захваты. С их помощью трубопровод приподнимается со дна, и под ним пропахивается траншея. После проведения этой операции трубы укладываются в получившееся углубление.
Сыпать тяжелый грунт на дно можно не всегда: масса гравия продавливает мягкие породы. В этом случае для «спрямления» рельефа используют более легкие опоры из металлических или пластиковых конструкций.
Теперь, пожалуй, самое интересное: как трубы оказываются на дне? Разумеется, сложно себе представить, что каждая отдельная 12-метровая труба приваривается к нитке газопровода прямо в море на глубине. Значит, эту процедуру необходимо проделывать до укладки. Что, собственно, и происходит на борту трубоукладочного судна.
Тут необходимо ненадолго вернуться к конструкции самой трубы и заметить, что после нанесения на нее антикоррозионной защиты и утяжеляющего бетонирования оконцовки труб остаются открытыми и незащищенными, — иначе сварка была бы затруднена. Поэтому участки соединений защищаются от коррозии уже после сварки. Сначала монтажные стыки изолируются с помощью полиэтиленового термоусадочного рукава, затем закрываются металлическим кожухом, а полость между кожухом и рукавом заполняется полиуретановой пеной, придающей месту стыка необходимую механическую прочность.
Далее происходит укладка S-образным способом. Сваренная из труб плеть приобретает в процессе укладки форму, напоминающую латинскую букву S. Плеть под небольшим углом выходит из кормы корабля, достаточно резко опускается вниз и достигает дна, где принимает горизонтальное положение. Труднее всего представить себе, что нить из стальных, покрытых бетоном 24-тонных труб способна к таким резким изгибам без разрушения, однако все происходит именно так.
Разумеется, для того чтобы плеть не сломалась, применяются разнообразные технологические хитрости. За трубоукладочным судном на десятки метров тянется стингер — специальное ложе, уменьшающее радиус наклона уходящей вниз плети. На судне также установлено натяжное устройство, прижимающее трубы книзу и снижающее нагрузки на изгибы. Наконец, система позиционирования точно контролирует положение судна, исключая рывки и резкие смещения, способные повредить трубопровод. Если укладку почему-либо требуется прервать, вместо очередной трубы к плети приваривают герметичную заглушку с креплениями и плеть «сбрасывают» на дно. При возобновлении работ другой корабль подцепит заглушку тросом и вытянет плеть обратно наверх.
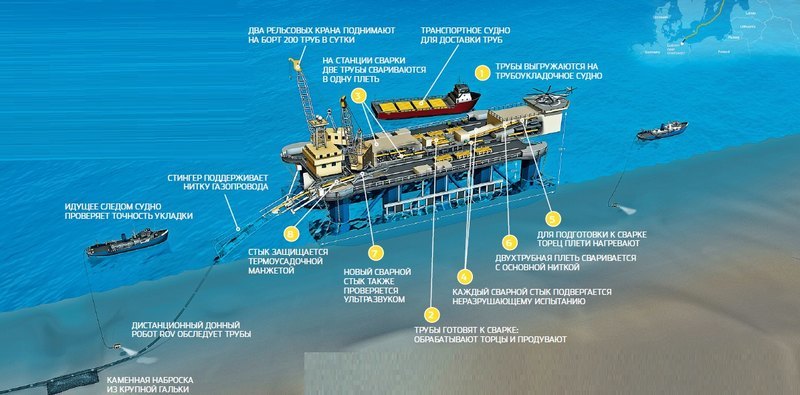
И все же без подводной сварки не обошлось. Дело в том, что каждая из ниток «Северного потока» состоит из трех секций. Различие между секциями — разная толщина стенок используемых труб. Пока газ идет от терминала в российской бухте Портовая к приемному терминалу на немецком берегу, давление газа постепенно падает. Это дало возможность использовать в центральной и финальной секциях более тонкостенные трубы и таким образом экономить металл. Вот только обеспечить соединение разных труб на борту трубоукладочных судов не представляется возможным. Сочленение секций происходило уже на дне — в гидроизолированной сварочной камере.
Для этого на дно опускались трубоподъемные механизмы, которые отрывали от дна и точно позиционировали друг напротив друга плети отдельных секций. Для той же цели применялись надувные мешки с переменной плавучестью, обеспечивавшие вертикальные перемещения труб. Термобарическая сварка велась в автоматическом режиме, однако наладка оборудования сварочной камеры — сложнейшая водолазная операция. Для ее проведения под воду опускалась водолазная камера, где могла проходить декомпрессию целая бригада водолазов, и специальный колокол для спуска ко дну. Сварка секций проводилась на глубине 80−110 м.
Прежде чем использовать газопровод для перекачки топлива, его испытывали… водой. Внутрь секций с помощью поршневого модуля была закачана предварительно отфильтрованная от взвесей и даже бактерий морская вода. Жидкость, нагнетавшаяся со специального судна, создавала внутри плети давление, превышающее рабочее, и такой режим поддерживался в течение суток. Затем вода откачивалась, и секция газопровода осушалась. Еще до того, как в трубопроводе появился природный газ, его трубы заполнялись азотом.
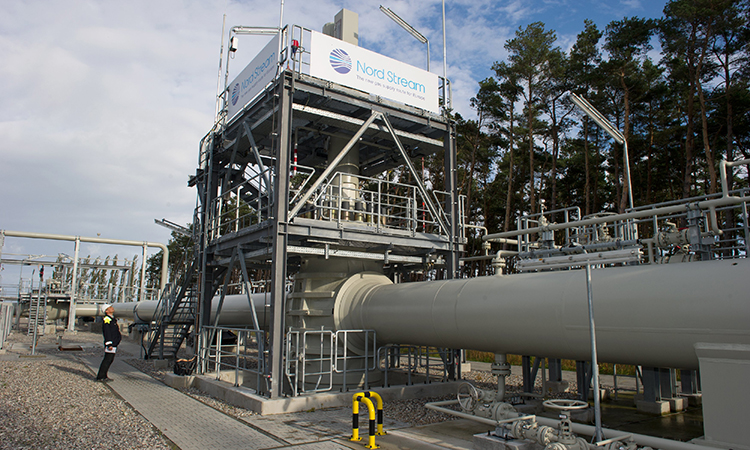
Прокладка газопровода по морскому дну — лишь часть проекта «Северный поток». Немало усилий и затрат потребовалось для оборудования береговой инфраструктуры. Отдельная история — это вытягивание нитки газопровода на берег с помощью мощной лебедки или создание механизма компенсации сезонного сжатия-расширения 1200-километровой нитки.

Строительство «Северного потока» вызвало немало дискуссий на разные околополитические темы — от экологии до чрезмерной роли сырьевого экспорта в экономике России. Но если абстрагироваться от политики, нельзя не заметить: трансбалтийский газопровод — отличный пример того, как продвинутые технологии и международная кооперация способны творить современные чудеса во вполне рабочем рутинном режиме.
Взято: Тут
874