madam.abuse
Оружие на 3D-принтере ( 7 фото )
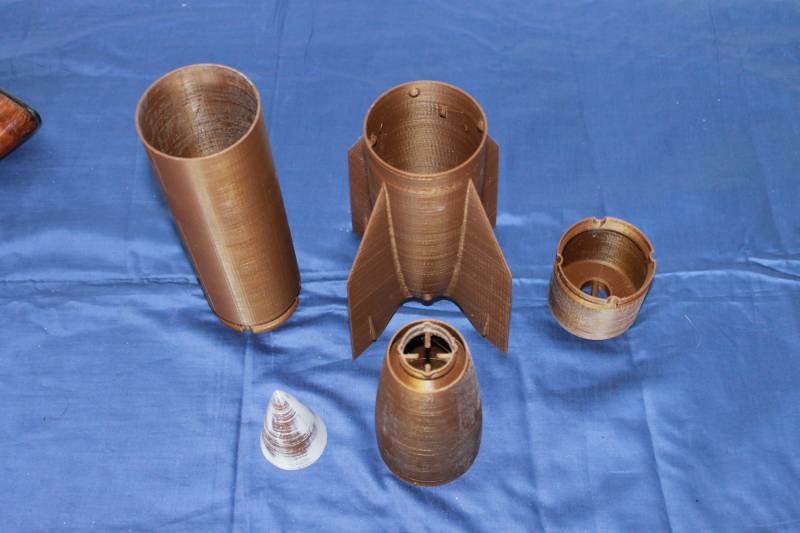
Детали реактивного снаряда ближнего радиуса действия, изготовленные в технологии 3D
Оружие XXI века. Оружия никогда много не бывает. Излишки, если кто-то решил, что это излишки, всегда можно продать, подарить и даже просто с выгодой утилизировать. Ну, а на войне просто грех экономить боеприпасы – чем больше мы перекинем противнику взрывчатки, тем… быстрее реализуем цели военных действий. Но вот проблема… По традиции оружие и боеприпасы делаются из лучших материалов, стали и прочих металлов, а это дорого и неэкологично.
На выплавку одной тонны металла надо потратить четыре тонны пресной воды. Которая после этого будет непригодна для питья. И зачем нам тогда нужны будут тысячи стальных снарядов, если у нас не хватит обычной питьевой воды? К тому же те же корпуса снарядов ещё и обрабатываются на токарных станках. А это стружка, которую надо собирать и опять плавить. То есть производство прежнего времени очень нерационально с технологической точки зрения: много воды, много отходов, много человеко-часов, которые нужно оплачивать.
В ХХI веке оружие и боеприпасы нужно производить иначе.
«Печатное оружие»
В частности, сегодня для этого можно использовать технологии 3D-печати. Пример, ставший хрестоматийным, относится к событию 10-летней давности. Тогда в 2013 году американский студент Коди Уилсон напечатал на 3D-принтере самый первый пистолет из пластика, который мог стрелять боевыми патронами.
Дальше больше – в 2017 году в Научно-исследовательском центре вооружений армии США распечатали на 3D-принтере ручной гранатомет и ещё боеприпасы к нему. Причем подчеркивалось, что все детали были изготовлены именно в технологии 3D. За основу конструкции был взят известный ручной 40-миллиметровый гранатомет M203 A1 и учебная граната M781, поскольку боевые к нему делать запретили.
Гранатомет из печати…
Для «печати» гранатомета и гранат к нему использовались сразу несколько видов трехмерной печати. Первый – это прямое металлическое лазерное спекание, когда лазер послойно сплавляет исходный металлический порошок в одну деталь, 3D-печать из пластмассы и отливка пластмассовых деталей в формах.
Наибольшую трудность представляла печать ствола гранатомета вместе с нарезами, который сделали из алюминия. Алюминиевой сделали и ствольную коробку. Спусковой крючок, ударник и курок гранатомета тоже «напечатали», но только уже из стального сплава марки 4340. Пистолетная рукоятка приклад, понятно, тоже были изготовлены из пластика – самые простые в данном случае детали для такой технологии.
В итоге оказалось, что в гранатомете только пружины, крепежные шпильки и винты были сделаны традиционным способом, а все остальное – в технологии ХХI века.
Правда, и ствол, и ствольную коробку пришлось дополнительно обрабатывать и убирать с поверхности шероховатости, а ещё для большей жесткости анодировать.
В целом изготовление гранатомета потребовало 70 часов на собственно печать и пять часов на анодирование и чистовую механическую обработку. В общем-то, это ни о чем не говорит – много это или мало. Но говорят цены, которые можно сравнить.
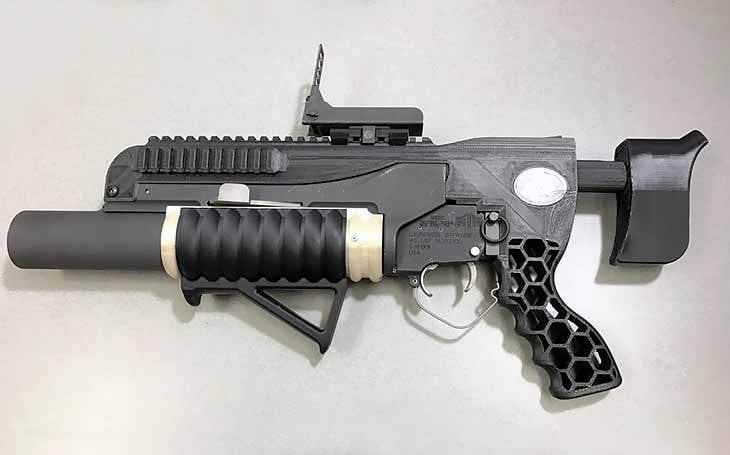
Гранатомет M203 A1, изготовленный по технологии 3D-печати
Так, себестоимость печатного гранатомета оказалась немногим больше ста долларов, причем львиная доля стоимости пришлась на металлические порошки для послойного спекания. Зато гранатомет M203 A1, сделанный по стандартной технологии стоит 1,1 тысячи долларов. То есть 3D-печать по своей ценовой эффективности даже превзошла традиционное производство.
«Лучшее – враг хорошего»
Правда, и на солнце есть пятна. Стандартные корпуса гранат отливают из цинка. А вот печатать их из цинка в силу его специфических свойств не получилось. Напечатали из стали. Но стальная граната обдирала алюминиевый ствол. Покрыли её пластиком. Стал обдираться пластик! Тогда гранату сделали из алюминия, и она оказалась легче цинковой, и дальность стрельбы у неё возросла, что сразу сделало невозможным использование старого прицела. Проблема, конечно, «просто грандиозная».
Ну и по технологии трехмерной печати не были сделаны такие детали, как гильза, капсюль и… метательный пороховой заряд. Просто в США существует запрет на использование взрывчатых веществ в составе изделий, изготовленных в технологии 3D.
А ведь ещё совсем недавно 3D-принтеры можно было встретить разве что в каких-нибудь НИИ. Они помогали создавать прототипы изделий, но и не более. Однако прошло каких-то 10–15 лет и методы аддитивного производства стали активно использоваться и в автомобилестроении, и в авиационной, и в аэрокосмической промышленности, а также в медицине и приборостроении. И выгоды его очевидны: это и более экономный расход сырья и, что главное, возможность производства геометрически очень сложных изделий.
К тому же выгодны и материалы, из которых делают печатные детали. Например, АBS-пластик – современный синтетический термопласт, широко применяемый сегодня среди прочих конструкционных материалов. Обладает высокими показателями прочности и износостойкости, долговечностью в эксплуатации, хотя и «не любит» ультрафиолетового излучения. Допустимо его использовать при температурах до +80 °C, при сохранении всех его технических свойств. Важно, что он не токсичен и может кратковременно выдержать нагрев до 100 °C. А ещё АBS-пластик отлично поддается механической обработке.
Известны и другие печатные пластики или филоменты, кроме АВС: PLA, PETG, Flex. У каждого свои определенные характеристики, так что нужный всегда можно подобрать. То есть 3D-печать открывает прямо-таки безграничные возможности по созданию функциональных и высокоэффективных конструкций, в том числе и в военной сфере.
А как с ценой? Например, пластик PETG стоит 10 рублей за грамм, что, в принципе,относительно недорого.
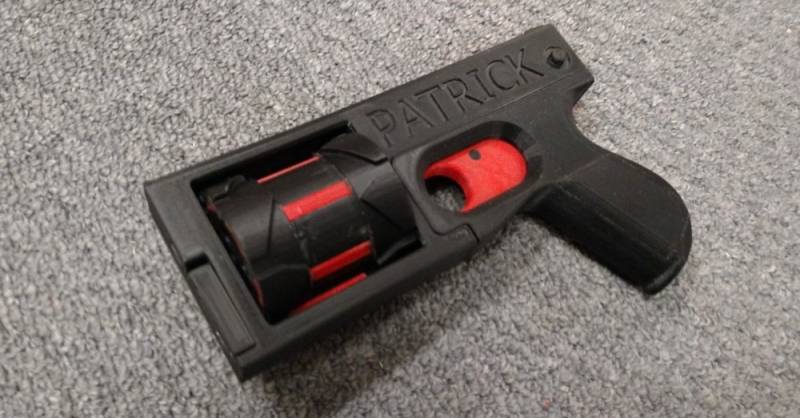
Револьвер Washbear, распечатанный в технологии 3D
«После однозарядного пистолета, восьмизарядный револьвер!»
Кстати, как выше уже отмечалось, прогресс в «печатном оружии» на месте не стоит, и там же в США уже распечатали и оригинальный шести- или восьмизарядный револьвер со сменным барабаном под патроны калибра .22LR. Название у него странное: Washbear, потому как не похож, но действует!
Печать восьмизарядного револьвера осуществлялась из ABS-пластика, усиленного внутри барабана металлическими вставками. А вот шестизарядный и вовсе можно напечатать из специального нейлона Bridge Nylon.
А что у нас?
А у нас компания F2 innovations, основанная выпускниками Пермского национального исследовательского политехнического университета (ПНИПУ), предлагает гранульный 3D-принтер F2 Gigantry, способный печатать самые большие изделия.
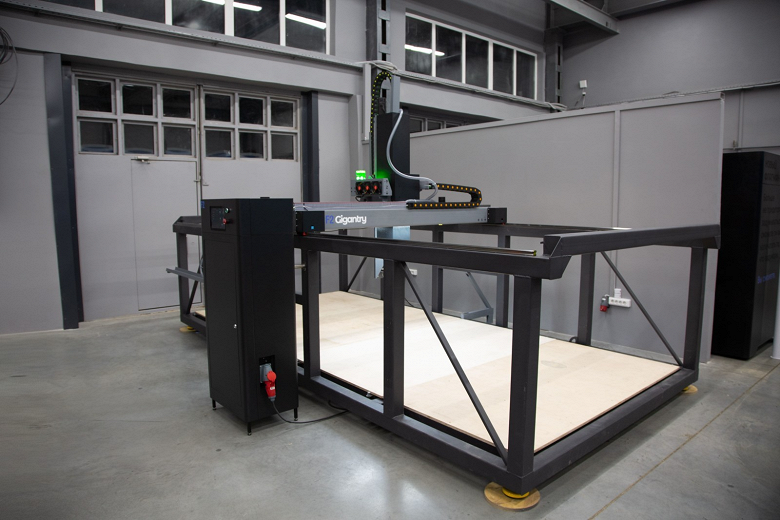
Вот как выглядит F2 Gigantry
F2 Gigantry – это обычная 3D-установка, в которой гранулы полимера расплавляются и подаются на принтер, осуществляющий движение по заданной траектории и послойную печать. Вот только способна она создавать детали до 4 метров в длину, 2 метра в ширину и 1 метр в высоту. При этом она печатает с производительностью до 10 кг/ч, причем может работать и на вторсырье, то есть на переработанном грануляте.
В общем-то, и технология такой печати совсем не нова, только таких больших российских установок, как F2 Gigantry, на нашем рынке ещё не было.
Выгода от F2 Gigantry позволяет заводам и, в частности аэрокосмической отрасли, производить крупногабаритные полимерные детали очень быстро и дёшево. Общие издержки при этом сокращаются примерно 40 раз по сравнению с традиционными технологиями.
Интересно, что первый серийный принтер модели F2 Gigantry был разработан… под персональный заказ для печати оснастки для изготовления композитных крыльев для самолётов. Но F2 Gigantry можно применять в любой сфере, включая и сферу военного производства.
«Ракеты на потоке»
А теперь посмотрим на фотографии. На них, модель ракеты ФАУ-2, собранная из деталей, распечатанных на 3D-принтере. Всего деталей 5. Значит – нужно 5 принтеров и пять рабочих, которые бы обрабатывали готовые детали в то время, когда станок печатает следующие. При этом он же занимается их комплектацией. Тот, кто отвечает за «нос», вставляет в него взрыватель. Те, которым «особо нечего делать», когда деталь обработана, участвует в заливке взрывчаткой готовой ракеты. Ответственный за хвостовую часть вставляет в неё пороховой двигатель, обернутый в асбест.
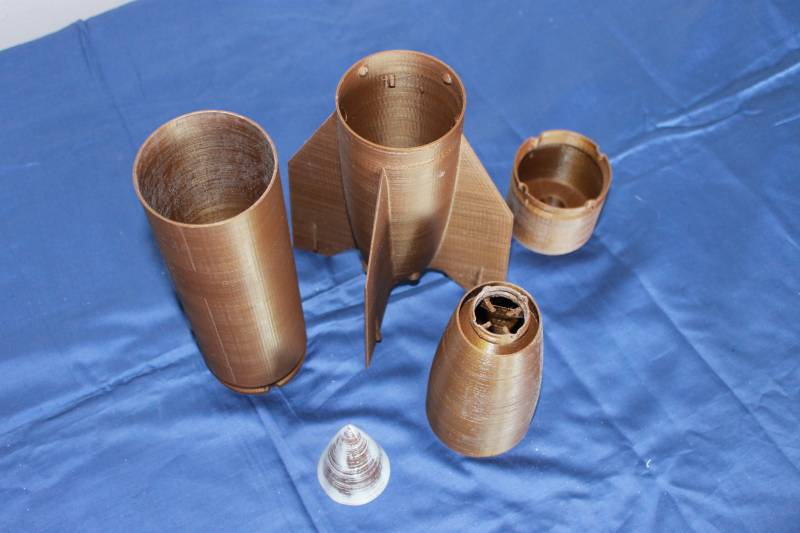
5 деталей реактивного снаряда ближнего действия
Затем, опять же, кто-то один из этих 5 рабочих вставляет готовую ракету в кассету, тоже распечатанную на 3D-принтере, только большого размера, или же изготовленную и собранную из металлического профлиста. Подключается электропроводка электрозапалов, и «изделие Х» отправляется на фронт. Оно легко транспортируется, легко маскируется, а дальность действия позволяет накрывать огнем значительную площадь.
Работает такое производство непрерывно, день и ночь, меняются только вахты. Причем оно может располагаться в бетонном бункере не очень далеко от линии фронта. Тут главное – хорошая маскировка подъездных путей.
А кассета после использования разбирается и отправляется обратно или же используется для обустройства траншей!
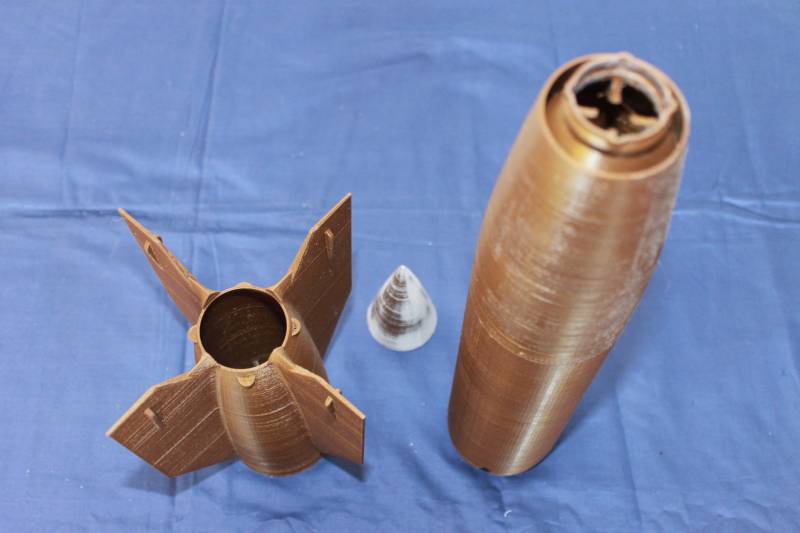
Три последние детали
Аналогичным образом могут распечатываться и беспилотники. Только на крупногабаритном принтере. Печатаем «низ», печатаем «верх», причем с минимальным расходом самого дешевого пластика – полет ведь в один конец. Блок управления – модульный, батарея питания – тоже модуль с быстроразъемными клеммами, бачок с топливом – готовый, заряд – готовый в виде «дыни» с готовыми осколками, кумулятивно-осколочного действия, телекамера – тоже отдельный блок, который прикручивается на место четырьмя шурупами. Обе половины корпуса склеиваются суперклеем. То есть сборка подобна детскому конструктору «Меккано».
Чтобы не ошибиться, сборщику можно все детали пометить хорошо заметными цифрами, и также цифрами их посадочные места: 1+1, 7+7, да, кстати, и сами посадочные гнезда только под эти детали и подходят, так что деталь 8 в гнездо 9 не вставить.
Движок – наш модельный МК-12В или аналоги моторов «Супер тигр» и «Бангей 600», с которым такой «самолет» мог бы развивать скорость до 225 км/ч. Стартует этот БПЛА при помощи стартового ускорителя, который сбрасывается после взлета.
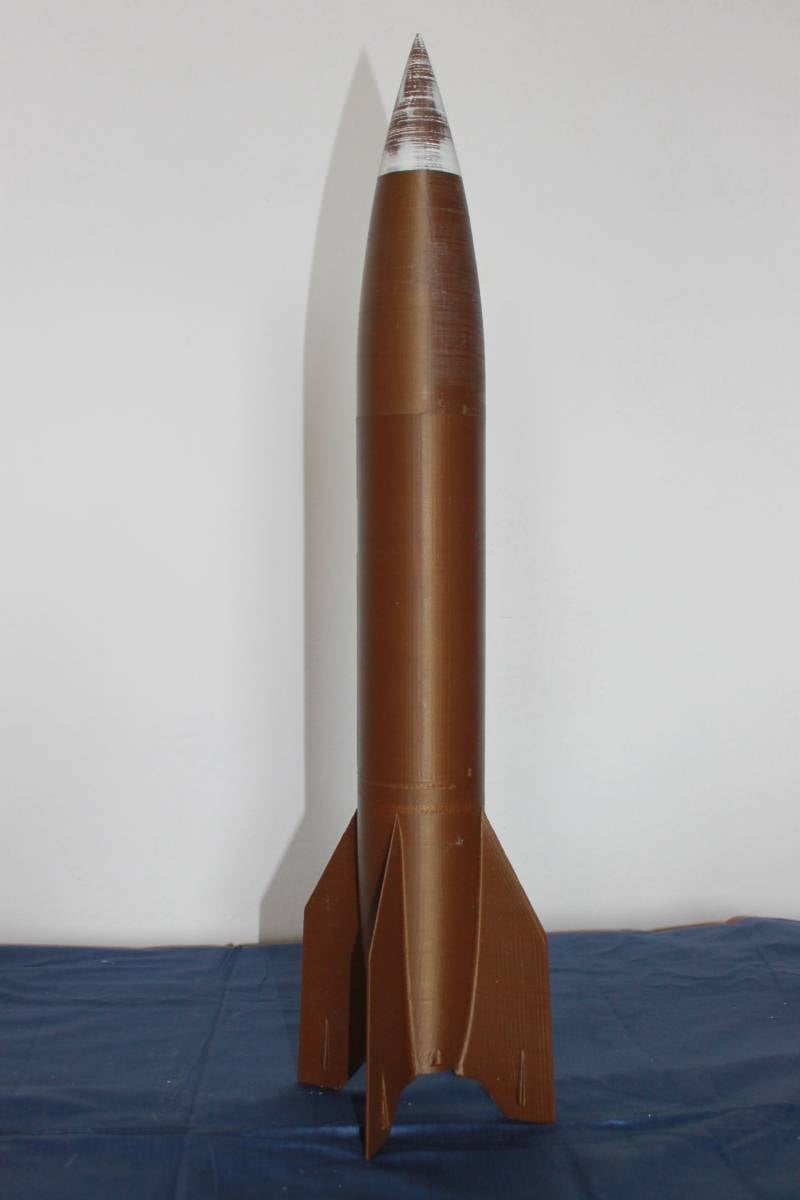
«Изделие Х» полностью готово к запуску
Интересно, что такие «заводы» с большой выгодой можно устанавливать и на кораблях. Ведь готовые БПЛА занимают при хранении много места, а тут складировать их можно по мере производства и запуска, что сэкономит и место, и время на проведение атаки с их помощью.
Такой должна быть война ХХI века (и будет!). И чем скорее люди, «принимающие решения», это поймут – тем лучше.
Автор:Константин Таратынов
Взято: Тут
277